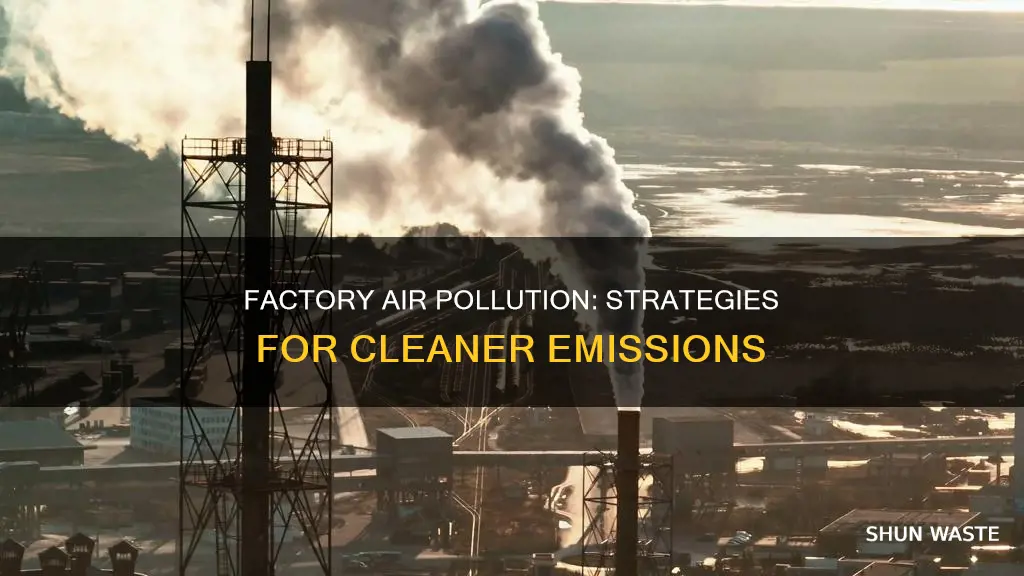
Air pollution from factories is a critical issue that needs to be addressed. Energy consumption is a major contributor to this type of pollution, so reducing energy use and switching to renewable energy sources are key ways to tackle it. Factories can also employ abatement mechanisms to destroy pollutants before they enter the environment. In addition, government agencies can implement environmental regulations and offer rewards to companies that operate within guidelines.
Characteristics | Values |
---|---|
Use public transport | Reduce air pollution by using public transport to travel to and from the factory |
Increase equipment efficiency | Consume less energy by optimising different parts of the operation |
Use natural gas | Reduce operating costs and extend the life of the plant by eliminating corrosion from fuels |
Use renewable energy sources | Reduce pollution over time and save money in the long run |
Implement environmental regulations | Levies, cap-and-trade systems, waste reduction techniques |
Take action against non-compliant industries | Offer significant rewards for companies that operate within guidelines |
Use efficient, low-polluting or zero-emission vehicles | Reduce air pollution from company vehicles |
Encourage bicycle use | Encourage employees to use bicycles for their daily commute |
Ensure traffic law compliance | Ensure drivers obey traffic laws, speed limits, maintain vehicles properly and keep optimum air pressure in tyres |
Use energy-efficient light bulbs | Reduce energy consumption by replacing lights with energy-efficient bulbs |
Limit paper use | Go green by limiting the use of paper |
Use recycled materials | Choose materials made from recycled content |
Maintain boilers properly | Reduce air pollution by properly maintaining boilers, e.g. blowing dust from the surface, reducing excess air |
Reduce steam usage | Identify leaks to reduce the need for steam |
What You'll Learn
Using renewable energy sources to power factories
Energy consumption is one of the main contributors to factory air pollution. Factories that require less energy to operate produce less air pollution. Renewable energy sources can power factories, resulting in less pollution over time and saving money in the long run. However, the initial investment in greener energy sources is often a hurdle that prevents many factories from making the switch to renewables.
Factories can reduce their energy consumption by increasing the efficiency of their equipment. This can be done by using electric motors with higher efficiencies, such as those with 95% efficiency now available. Proper maintenance of boilers, such as blowing dust from the surface and reducing excess air, can also reduce air pollution. In addition, identifying and fixing leaks in the boiler system can boost the system's efficiency by 10-50%.
Another way to reduce air pollution from factories is to switch from coal and oil to natural gas. This can reduce operating costs and extend the plant's life by eliminating corrosion from fuels. Factory operators can also employ abatement mechanisms that help destroy VOCs, HAPs, and other pollutants before they enter the environment.
Government agencies have experimented with various environmental regulations to reduce factory pollution, including levies, cap-and-trade systems, and waste reduction techniques. However, it often takes more stringent regulation to decrease factory pollution because many measures that reduce pollution cost money and take time to implement.
Soil Pollution: Silver's Toxic Legacy?
You may want to see also
Optimising operations to save energy
There are several ways that factories can reduce their energy consumption. Firstly, they can switch to renewable energy sources. Although the initial investment in greener energy sources can be costly, it could save factories money in the long run. Secondly, factories can increase the efficiency of their equipment. For example, they can replace lights with energy-efficient bulbs, and switch to electric motors with 95% efficiency.
Another way to reduce air pollution from factories is to employ abatement mechanisms that help destroy VOCs, HAPs, and other pollutants before they enter the environment. Factories can also reduce their reliance on boilers by identifying leaks, and switching from coal and oil to natural gas, which can reduce operating costs and extend the life of the plant.
In addition to measures taken by individual factories, government agencies can also play a role in reducing factory pollution. This can include implementing environmental regulations, such as levies on pollution, cap-and-trade systems, and waste reduction techniques. Government agencies can also offer rewards for companies that operate within guidelines, and take action against those that do not.
Fracking's Impact: Groundwater Pollution's Extent and Danger
You may want to see also
Using abatement mechanisms to destroy VOCs, HAPs, and other pollutants
Factory operators can employ abatement mechanisms to destroy VOCs, HAPs, and other pollutants before they enter the environment. This is one of many ways to reduce air pollution from factories.
VOCs (volatile organic compounds) and HAPs (hazardous air pollutants) are released into the atmosphere as a result of industrial activities and can have detrimental effects on human health and the environment. Abatement mechanisms are designed to capture and destroy these pollutants, reducing their impact on air quality.
There are a variety of abatement mechanisms available, each with its own advantages and disadvantages. Some common types include thermal oxidisers, which use high temperatures to break down pollutants, and scrubbers, which use a liquid to absorb pollutants from the air. Other mechanisms may utilise filtration, adsorption, or biological treatment processes to remove pollutants.
When selecting an abatement mechanism, factory operators must consider the specific pollutants being emitted, the volume of emissions, and the unique characteristics of their facility. By carefully matching the abatement technology to the pollution source, operators can maximise the mechanism's effectiveness.
Additionally, regular maintenance and optimisation of abatement mechanisms are crucial to ensure their long-term performance. Factory operators should establish routine inspection and maintenance schedules to identify and address any issues promptly. This proactive approach helps maintain the efficiency of the abatement mechanisms, ensuring their continued success in reducing air pollution.
Stopping Air Pollution: Effective Strategies and Solutions
You may want to see also
Using electric vehicles for company vehicles
Using electric vehicles for company cars is one of the most effective ways to reduce air pollution from factories. Electric vehicles are more efficient and produce fewer emissions than traditional cars, which means they contribute less to air pollution.
When purchasing company vehicles, it is important to consider the most efficient, lowest-polluting options available. Electric vehicles are a great choice as they produce zero emissions. Not only are they better for the environment, but they can also save companies money in the long run. The initial investment in an electric vehicle may be higher, but the running costs are often lower due to the reduced need for fuel.
To further reduce air pollution, companies can encourage employees to use electric vehicles for their daily commute. This can be done through incentives such as providing charging stations or offering discounts on electric car leases. Additionally, companies can ensure that their drivers are obeying traffic laws, maintaining proper vehicle maintenance, and keeping optimum air pressure in their tyres.
Another way to reduce air pollution from company vehicles is to switch to renewable energy sources for powering the fleet. This can be done through the use of solar panels or wind turbines, which produce less pollution than traditional power sources. While the initial investment in renewable energy sources may be high, it will result in less pollution over time and could save companies money in the long run.
Overall, using electric vehicles for company cars is a great way to reduce air pollution from factories. By considering the most efficient and lowest-polluting options, encouraging employees to use electric vehicles, and switching to renewable energy sources, companies can make a significant impact on reducing air pollution.
Water Pollution's Impact on Biodiversity and Ecosystems
You may want to see also
Using energy-efficient lightbulbs
Energy consumption is one of the main contributors to air pollution from factories. Therefore, factories that require less energy to operate produce less air pollution. A large-scale shift to using renewable energy sources to power factories would result in less pollution over time and could also save factories money in the long run. However, the initial investment in greener energy sources is often a hurdle that prevents many factories from making the switch to renewables, even if it makes financial and environmental sense when looking at the bigger picture.
Factories can reduce their energy consumption by using energy-efficient lightbulbs. Energy-efficient lightbulbs use less energy to produce the same amount of light as traditional incandescent bulbs. This means that factories that switch to energy-efficient lightbulbs will use less energy and produce less pollution.
There are several types of energy-efficient lightbulbs available, including compact fluorescent lamps (CFLs) and light-emitting diodes (LEDs). CFLs use about one-third the energy of incandescent bulbs and last up to 10 times longer. LEDs use even less energy than CFLs and have a longer lifespan. They are also more durable and can be used in a wider range of temperatures.
Factories can also reduce their energy consumption by using energy-efficient equipment and appliances. For example, electric motors with 95% efficiency are now available, compared to earlier motors with 60-90% efficiency. Proper maintenance of boilers can also reduce energy consumption and air pollution. For example, reducing the excess air in a boiler can improve its efficiency by 10-50%.
In addition to using energy-efficient lightbulbs and equipment, factories can also reduce their energy consumption by optimising their operations. This includes measures such as improving insulation, using natural gas instead of coal or oil, and employing abatement mechanisms that help destroy VOCs, HAPs, and other pollutants before they enter the environment.
Oyster Power: Transforming Nutrient Pollution's Impact
You may want to see also
Frequently asked questions
Factories can reduce air pollution by using renewable energy sources, such as natural gas, instead of coal and oil.
Factories can also employ abatement mechanisms that help destroy VOCs, HAPs, and other pollutants before they enter the environment.
Governments can implement environmental regulations, such as levies that make polluters pay a fixed amount for pollution, and cap-and-trade systems that set the amount of emissions.
Individuals can use public transport or bicycles to commute to work, and ensure that their vehicles are properly maintained and have optimum tyre pressure.