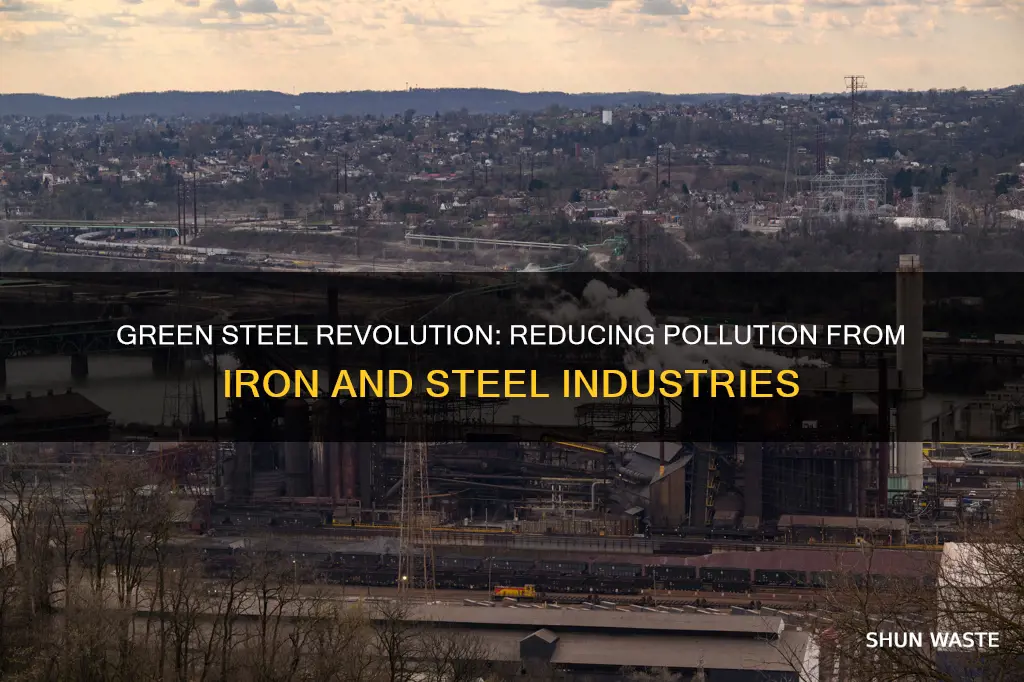
The iron and steel industry is one of the largest industrial emitters of CO2, accounting for about 7% of global anthropogenic carbon dioxide emissions. As the industry refers to the largest energy-consuming manufacturing sector in the world, it is responsible for producing steel through processes such as Blast Furnace/Basic Oxygen Furnace (BF/BOF) and Electric Arc Furnace (EAF). The production of steel is an energy-intensive process that has a significant environmental impact. It is one of the major air-polluting industries due to its heavy dependence on fossil fuels, especially coal, as its primary source of energy. The combustion of these fossil fuels releases harmful emissions, including metal oxides, smoke, fumes, dust, organic and inorganic gases, and fluorides, which have adverse effects on human health and the environment. To reduce pollution caused by the iron and steel industry, there is a need to explore and implement techniques for effective emissions reduction, such as energy optimization, fuel change, recycling scrap metal, and training workers on optimizing processes to reduce carbon emissions.
Characteristics | Values |
---|---|
Energy optimization | Upgrading to newer technologies that use energy more efficiently |
Fuel change | Using an alternative cleaner and less expensive fuel instead of coal |
Recycling | Recycling scrap metal instead of forging new steel |
Training | Training workers on ways to optimize the use of machines, equipment, and processes to reduce CO2 emissions |
Wastewater | Reducing water consumption and improving wastewater quality |
Electrification | Replacing fossil fuel-based heating with electric power sources |
What You'll Learn
Use hydrogen plasma smelting to reduce iron ore
The iron and steel industry is the largest industrial emitter of CO2, accounting for about 7% of global emissions. This has prompted researchers to shift their attention towards reducing CO2 emissions from this sector.
One promising route to achieving carbon-lean steel production is Hydrogen Plasma Reduction (HPR). HPR is a sustainable alternative for ironmaking, as the associated byproduct is water. In this process, a hydrogen plasma arc is ignited between an electrode and the ore in a conventional electrical arc furnace (EAF). This enables melting and reduction to occur simultaneously, allowing for the production of liquid iron in a single step. The highly energetic hydrogen species in the plasma enable exothermic redox chemical reactions with enhanced kinetics, permitting energy savings.
The Max-Planck-Institut für Eisenforschung GmbH has conducted research into the fundamental scientific questions related to HPR. Their studies focus on the reaction thermodynamics, kinetics, associated phase transformations, microstructural evolutions, and transport phenomena. Their initial findings show that gangue elements, such as Si, are preferentially partitioned to the unreduced oxide domains at the micro and nanoscale. However, these elements are evaporated over the course of the reduction process due to their higher vapour pressure compared to iron. As a result, iron nearly free of gangue elements, especially S and P, can be obtained after a short exposure to a lean hydrogen plasma in a conventional lab-scale arc melt furnace.
The implementation of HPR can play a crucial role in reducing pollution caused by the iron and steel industry. By transitioning to HPR, the industry can significantly reduce its CO2 emissions and move towards more sustainable practices. This technology offers a promising future for the industry, as it not only reduces pollution but also provides energy savings and enables the production of "green steel".
Reducing Ocean Plastic Pollution: Strategies for a Cleaner Future
You may want to see also
Reduce fossil fuel consumption
The iron and steel industry is the You may want to see also Recycling scrap metal is an effective way to reduce pollution caused by the iron and steel industry. It is a process that involves collecting, sorting, and processing scrap metal into new products. This process has several benefits that contribute to pollution reduction and environmental sustainability. Firstly, recycling scrap metal helps to reduce the use of chemicals and fossil fuels. When new metals are extracted from the earth, it requires significant energy and resources, often involving the use of chemicals and fossil fuels. By recycling scrap metal, we can reduce the demand for new metals and lower our reliance on these harmful substances. For example, recycling steel saves 60% of the energy required to produce steel from iron ore, while recycling aluminum uses 95% less energy compared to producing it from raw materials. This reduction in energy consumption leads to a decrease in carbon emissions, contributing to a lower carbon footprint. Secondly, recycling scrap metal helps to conserve natural resources by reducing the need for mining and extraction of raw materials. Mining activities can cause soil erosion, water pollution, habitat destruction, and the release of greenhouse gases. By recycling scrap metal, we can minimize the environmental impact of mining, protect natural resources, and reduce waste. Additionally, recycling scrap metal contributes to the circular economy, where materials are reused and repurposed, reducing the need for disposal and landfilling. Moreover, recycling scrap metal has economic benefits that indirectly support pollution reduction efforts. The scrap metal industry generates revenue and creates job opportunities worldwide. It provides an income stream for manufacturers and factories by buying excess scrap from them. Recycling scrap metal also helps lower production costs for manufacturers as recycled metals are less expensive than mining for virgin ore. This financial incentive encourages manufacturers to use recycled materials, reducing their overall expenses and contributing to sustainability. Furthermore, recycling scrap metal can lead to a decrease in global energy consumption. The iron and steel industry is the largest consumer of energy among industrial sectors, and it is responsible for a significant portion of global greenhouse gas emissions. By recycling scrap metal and using it as a raw material, we can reduce the energy-intensive process of extracting and processing new metals, thus lowering energy consumption and subsequent emissions. Lastly, recycling scrap metal can be further optimized through improved waste management systems and innovative recovery processes. By enhancing the collection and segregation of scrap metal, we can increase the amount of metal available for recycling, ensuring that less metal ends up in landfills. This optimization will be crucial in decarbonizing the steel industry and meeting the challenges posed by the growing demand for steel. You may want to see also Improving energy efficiency in the iron and steel industry is crucial to reducing pollution and achieving sustainability goals. Here are some measures that can be implemented to enhance energy efficiency: Decarbonization and Efficiency: To meet global climate goals, the iron and steel industry needs to cut emissions by approximately 50% by 2050. This involves both decarbonizing production processes and improving energy efficiency. The industry's heavy reliance on fossil fuels, particularly coal, which accounts for about 75% of its energy needs, is a significant contributor to CO2 emissions. By transitioning to cleaner energy sources and reducing fossil fuel usage, the industry can significantly reduce its carbon footprint. Motor System Modernization: Motor systems in iron and steel plants, including fans, compressors, pumps, and rolling mills, often suffer from inefficiencies. While these systems consume only about 7% of the total energy, it is estimated that up to 70% of the energy they use is wasted due to inefficiencies. By modernizing motor systems and adopting variable speed drives (VSD), significant energy cost reductions can be achieved. For instance, adding VSDs to fans in a basic oxygen furnace can lower power demand and costs by about 20%. Technology Upgrades: Upgrading to newer, more energy-efficient technologies can play a crucial role in reducing energy consumption and CO2 emissions. Electric arc furnaces, for example, can replace basic oxygen furnaces, and hydrogen can be used as a reducing agent instead of carbon and coke. These technological advancements not only reduce the industry's environmental impact but also improve overall energy efficiency. Energy Management Programs: Adopting effective energy management programs, such as the ENERGY STAR Guidelines for Energy Management, can assist iron and steel producers in identifying areas for energy savings within their operations. By following industry best practices and utilizing energy performance indicator (EPI) tools, mills can assess their energy efficiency relative to similar mills and work towards improving their energy performance. Energy-Efficient Practices and Technologies: There are numerous energy-efficient practices and technologies that can be implemented at the component, process, facility, and organizational levels within the iron and steel industry. This includes improving energy efficiency in specific processes, such as coke quenching, blast furnace cooling, and descaling in hot rolling mills. Additionally, waste heat recovery and the use of steam can also contribute to overall energy efficiency improvements. You may want to see also The iron and steel industry is the largest energy-consuming manufacturing sector in the world, and it is also one of the largest industrial emitters of CO2, accounting for about 7% of global anthropogenic CO2 emissions. As such, the use of alternative fuels is a crucial strategy to reduce pollution in this industry. Here are some detailed suggestions for adopting alternative fuels: Hydrogen-based Direct Reduced Iron (DRI) Hydrogen-based DRI is a promising technology for reducing emissions in the iron and steel industry. In this process, hydrogen is used as a reducing agent to produce molten iron directly from iron ore. This method eliminates the need for coke, which is typically produced by heating coal in the absence of oxygen. By avoiding the use of coke, hydrogen-based DRI can significantly reduce the carbon emissions associated with traditional iron and steelmaking processes. According to the IEA's Sustainable Development Scenario, hydrogen-based DRI could account for nearly 15% of primary steel production globally by 2050. Carbon Capture, Use, and Storage (CCUS) Carbon Capture, Use, and Storage (CCUS) is another crucial technology for reducing emissions in the iron and steel industry. CCUS involves capturing carbon dioxide produced during steelmaking and either using it for other industrial processes or storing it underground. This technology can be applied to various steelmaking processes, including innovative blast furnace concepts and gas-based DRI. In the Sustainable Development Scenario, hydrogen and CCUS together account for around one-quarter of the cumulative emission reductions. Bioenergy Bioenergy is an alternative fuel source that can be utilised in the iron and steel industry to reduce emissions. Bioenergy refers to energy derived from biomass, such as agricultural and forest residues, energy crops, and organic waste. By using bioenergy instead of fossil fuels, the industry can reduce its reliance on coal and natural gas, which have a significant carbon footprint. Additionally, bioenergy can be used in conjunction with CCUS technologies to further reduce emissions. Direct Electrification Direct electrification of steelmaking processes is another strategy to reduce pollution. By using electricity instead of fossil fuels, the industry can take advantage of the increasing share of renewable energy in the global energy mix. This shift can help to decarbonise the steelmaking process, especially in regions with access to low-cost renewable electricity. However, it is important to note that direct electrification may not be feasible for all steelmaking processes due to the high temperatures required. Fuel Switching to Natural Gas While natural gas is still a fossil fuel, switching from coal to natural gas can lead to a significant reduction in emissions. Natural gas is a cleaner-burning fuel that produces fewer air pollutants and greenhouse gas emissions compared to coal. This transition can be a short-term solution while the industry works towards adopting more sustainable alternatives, such as hydrogen and bioenergy. You may want to see also The iron and steel industry is one of the most carbon-intensive manufacturing processes, contributing about 7% of carbon dioxide emissions globally. The industry is also one of the largest industrial emitters of CO2, accounting for about 7% of global anthropogenic CO2 emissions. The main sources of pollution in this industry include iron making, coking, smelting of ores, and the use of fossil fuels, particularly coal. According to the U.S. Environmental Protection Agency (EPA), exposure to criteria air pollutants can lead to various respiratory issues, including inflammation of the lungs, reduced lung function, increased susceptibility to respiratory infections, and aggravation of cardiovascular disease. It can also cause neurodevelopmental issues such as lowered IQ and behavioural problems. To reduce pollution, the industry can adopt a combination of strategies, including: - Energy optimization: Upgrading to newer, more energy-efficient technologies. - Fuel change: Switching from coal to alternative, cleaner, and less expensive fuels. - Recycling: Encouraging the recycling of scrap metal instead of forging new steel. - Training and awareness: Educating workers on optimizing machine use to reduce CO2 emissions. - Carbon capture: Applying carbon capture and storage techniques to mitigate emissions.Reforestation: Fighting Pollution, Restoring Nature's Balance
Recycle scrap metal
Protecting Nature: Humans' Role in Conservation
Improve energy efficiency
Mitigating Agricultural Water Pollution: Strategies for Sustainable Farming
Use alternative fuels
Reducing Sewage Pollution: Strategies for a Cleaner Environment
Frequently asked questions