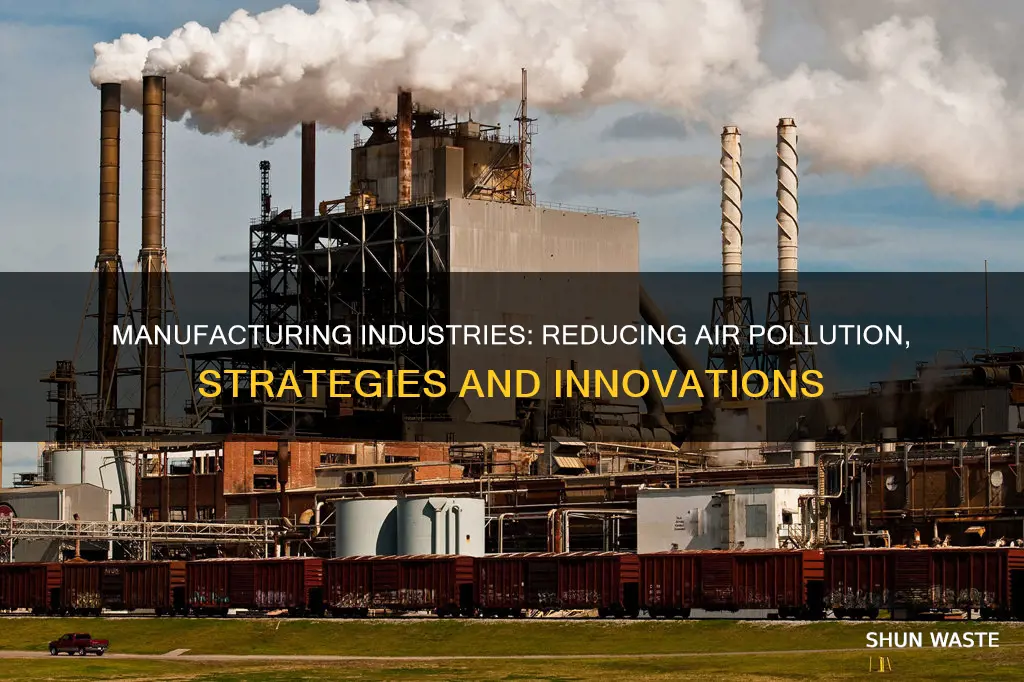
Air pollution is a pressing issue, with 92% of the global population living in areas that exceed safe levels of pollutants. Industrial activities are a major contributor to this problem, and with increasing consumer demand, the stress on the environment and human health is only growing. As such, it is crucial to explore ways in which manufacturing industries can reduce air pollution. This involves adopting strategies to tackle pollutants at their source, improve energy efficiency, and implement effective air filtration systems.
Characteristics | Values |
---|---|
Energy Sources | Transition to renewable energy sources such as solar, wind, hydro, and geothermal power. |
Energy Efficiency | Improve energy efficiency by implementing energy-saving technologies, such as LED lighting and high-efficiency heating and cooling systems. |
Sustainable Materials | Use recyclable or biodegradable materials with low environmental impact during the manufacturing process. |
Air Filtration Systems | Install industrial air filtration systems to improve indoor air quality and reduce environmental impact. |
Dust & Fume Collection Systems | Use dust and fume collection systems to control dust and ambient gases generated during manufacturing operations. |
Regulatory Compliance | Monitor and ensure compliance with air quality regulations to reduce emissions. |
Employee Health & Safety | Improve employee health and safety by providing breathing masks and PPE when necessary. |
Pollution Control Devices | Install pollution control devices, such as oxidizers and rotary concentrators, to destroy pollutants before they enter the atmosphere. |
Transport | Use public transport, electric vehicles, or bicycles for daily commutes to reduce transportation emissions. |
Paper Usage | Limit paper usage and promote digital solutions to reduce deforestation and associated air pollution. |
What You'll Learn
Use renewable energy sources
Manufacturing industries can play a crucial role in reducing air pollution and mitigating climate change by transitioning to renewable energy sources. This shift is essential to decrease our dependence on fossil fuels, which are major drivers of air and water pollution. By embracing clean and sustainable energy options, industries can significantly reduce their environmental impact and contribute to a healthier planet. Here are several paragraphs detailing the importance and benefits of adopting renewable energy sources:
Paragraph 1: The Importance of Transitioning to Renewable Energy
The manufacturing industry's reliance on fossil fuels has severe environmental consequences, particularly in terms of air pollution and climate change. To address this issue, it is crucial to transition to renewable energy sources such as solar, wind, hydro, and geothermal power. These clean energy sources emit little to no pollutants, helping to reduce air pollution and our carbon footprint. By investing in renewable technologies and promoting policies that encourage renewable energy markets, we can create a healthier and more sustainable future for all.
Paragraph 2: Reducing Dependence on Fossil Fuels
Fossil fuels, including coal, oil, and gas, are the primary contributors to global climate change, accounting for over 75% of greenhouse gas emissions. By transitioning to renewable energy, we can reduce our dependence on these finite resources and mitigate their harmful effects on the environment. Renewable energy sources are naturally replenished and widely available, offering a more sustainable and environmentally friendly alternative. This shift not only reduces air pollution but also lessens the environmental impact of energy generation, improving the planet's overall health.
Paragraph 3: Economic Benefits of Renewable Energy
In addition to the environmental benefits, renewable energy sources offer significant economic advantages. Renewable energy technologies have become increasingly affordable, with prices rapidly dropping in recent years. Investing in renewable energy creates three times more jobs than investing in the fossil fuel industry. By 2030, it is estimated that the transition to net-zero emissions will result in a net gain of 9 million jobs in the clean energy sector. Additionally, renewable energy sources provide countries with energy independence, reducing their vulnerability to unpredictable fossil fuel price fluctuations and geopolitical crises.
Paragraph 4: Health Benefits of Renewable Energy
The adoption of renewable energy sources has a direct positive impact on public health. According to the World Health Organization, about 99% of people worldwide breathe air that exceeds safe limits, and air pollution from fossil fuels is responsible for millions of deaths each year. By transitioning to clean energy sources, such as wind and solar power, we can significantly improve air quality and reduce the health risks associated with air pollution. This includes lowering the levels of fine particulate matter (PM2.5) and nitrogen dioxide, which are harmful to human health.
Paragraph 5: Resilience and Extreme Weather Events
Renewable energy sources also enhance resilience in the face of extreme weather events. For example, during Hurricane Sandy in 2012, renewable energy projects remained largely undamaged and operational, while fossil fuel-based electric generation was severely impacted, leaving millions without power. By increasing the share of renewable energy in our energy mix, we can build a more resilient and reliable energy system, better equipped to withstand the challenges posed by climate change and extreme weather events.
Fish Drowning in Polluted Waters: An Unseen Crisis
You may want to see also
Improve energy efficiency
Improving energy efficiency is one of the most effective ways for manufacturing industries to cut down on air pollution. This can be achieved through various means, such as:
Optimising Scheduling
Altering the schedules for processes or machines can benefit energy efficiency. Most idling machines can require up to 80% of the energy loads drawn during full production, so significant savings can be made through scheduling optimisation. Manufacturers have traditionally optimised for output, energy, or production efficiency. However, cutting-edge research is now being carried out to find schedules that maintain production levels while reducing energy usage.
Equipment Maintenance
Proper maintenance of factory equipment can lead to gains in energy efficiency. There are three basic approaches: reactive, preventative, and predictive maintenance. Reactive maintenance is performed after a machine or process fails and is the least energy-efficient scheme. Preventative maintenance is time-based and carried out according to a pre-set schedule. Predictive maintenance, or "conditions-based maintenance", involves proactive monitoring of machines for any changes to their condition. This is the most energy-efficient approach, reducing overall energy usage by 18% compared to reactive maintenance.
Lighting
Lighting can represent up to 40% of a building's electricity use, so switching from incandescent bulbs to LED lights can result in substantial energy savings. Ensuring efficient distribution of light by using the right amount of light in the right places is also important.
Heating, Ventilation, and Air Conditioning (HVAC)
HVAC systems account for around 15% of all energy use in manufacturing. Simple measures such as setting the correct time and date, maintaining lower temperatures in hallways, and restricting access to heating and cooling controls can help optimise energy usage.
Boilers
Boilers are often used in manufacturing for space-heating and process-heating. Optimising energy efficiency in boilers involves checking flue-gas exit temperatures, excess air in the system, and burnout. Replacing an inefficient boiler with a condensing boiler can lead to efficiency gains of up to 25%.
Renewable Energy
Although using renewable energy may not directly reduce a manufacturer's energy usage, it can help to reduce a factory's carbon footprint and increase energy resilience by diversifying energy sources.
Energy Management Systems
Energy Management Systems (EMS) are a set of tools that allow manufacturers to monitor, measure, analyse, and control energy consumption. While there is an upfront cost, EMS can help manufacturers discover and prioritise energy efficiency opportunities.
Energy Audits
Energy audits are a formal process undertaken with the help of a professional third-party auditor to assess an operation's energy efficiency and identify powerful steps to significantly reduce energy usage.
Biofiltration: Nature's Solution to Purifying Polluted Water
You may want to see also
Install air filtration systems
Manufacturing industries can significantly reduce air pollution by installing air filtration systems. These systems are designed to block and trap air pollutants, which can range from invisible gases to dust particles.
There are various types of air filtration systems, including electrostatic precipitators, scrubbers, and emission control systems. For instance, an air scrubber is an air purification system that removes particulate matter from the air by using moisture or by cooling or filtering the airstream. Electrostatic precipitators use electrostatic forces to remove particles and pollutants from the air, while emission control systems focus on capturing and controlling pollutants before they are released into the atmosphere.
Air filtration systems can be customised to meet the specific needs of different industries. For example, the food and chemical processing industries may require high-efficiency particulate air (HEPA) filters, which can remove particles as small as 0.3 nanometres. On the other hand, manufacturing, automotive, and aerospace industries may only need to focus on large particle removal to maintain a safe and healthy work environment.
By installing air filtration systems, industries can effectively remove impurities such as dust, pollen, mould, bacteria, metallic powder, gases, and chemicals from the air. These systems not only improve the air quality for workers but also ensure the proper functioning of equipment by preventing clogging and damage caused by pollutants.
Additionally, air filtration systems can be designed for specific applications within a facility. Dust and fume collection systems, for instance, are crucial for removing exhaust fumes generated during welding, sanding, grinding, and spraying processes. These systems utilise sealed filters to trap particle contaminants, ensuring that clean air is released back into the environment or recirculated within the facility.
Hydroelectric Power: Pollution Paradox?
You may want to see also
Implement dust and fume collection systems
Dust and fumes are an inevitable byproduct of many manufacturing processes, and they can pose a serious risk to employee health and safety. Implementing dust and fume collection systems is critical to maintaining good indoor air quality and ensuring compliance with regulatory bodies. Here are some detailed steps and considerations for implementing such systems:
Types of Dust and Fume Collection Systems:
- Cartridge Dust Collectors: These are popular for general factory air cleaning due to their versatility. They use filter cartridges filled with pleated nonwoven fabric to capture dust and fumes from the airstream. The filters provide a large surface area to capture dust, and the media can be made from a blend of polyester and cellulose or spunbond fabric for durability.
- Baghouses or Bag Filter Dust Collectors: These operate similarly to cartridge collectors but can handle higher volumes of dust-laden air. They use long cylinder-shaped bags made from woven fabric and a pulse-cleaning system to remove dust.
- Wet Scrubbers: Wet scrubbers use water or another liquid to remove dust particles. They are suitable for operations involving flammable materials or where the liquid and dust mixture can be reused. They create a vortex of liquid droplets that mix with the particle-laden airstream, and the particles are then removed by centrifugal force.
- Portable Dust Collectors: These are smaller units designed for isolated jobs that produce dust. They can be positioned near the dust source and used in conjunction with larger dust collection systems.
- Shaker Dust Collectors: These are shake-cleaning baghouse systems that either clean offline or are compartmentalized for continuous cleaning. They are common in foundries, steel mills, mining, and bulk storage applications.
- Pulse Jet Dust Collectors: These are highly customizable baghouse systems with rapid, high-pressure air jet cleaning. They are widely used due to their ability to handle a wide range of temperatures and pressures and their high collection efficiency.
- Cyclone Dust Collectors: These are inertial separators that use centrifugal force to separate dust from the gas stream, creating a cyclonic action within the collection chamber. They are often used in woodworking, pulp and paper, and recycling plants.
- Electrostatic Precipitators: These use static electricity to separate soot, ash, and dust particles from exhaust gases. They are found in industrial power plants burning fossil fuels.
Factors to Consider:
- Application and Industry: Different industries and applications will have unique dust and fume characteristics. It is essential to understand the specific pollutants generated in your facility to select the most effective collection system.
- Facility Size and Dust Volume: The size of your facility and the volume of dust produced will influence the type and capacity of the collection system required.
- Regulatory Compliance: Ensure that your dust collection system complies with regulations set by major regulatory bodies such as OSHA, NFPA, and EPA.
- Maintenance and Cleaning: Regular maintenance and cleaning of the dust collection system are crucial. Implement regular cleaning procedures, such as pulse-cleaning for cartridge filters, to maintain system efficiency and prolong its lifespan.
- Employee Training: Ensure that employees are trained in the proper use and maintenance of the dust collection system. This includes understanding the system's limitations and any potential risks associated with its operation.
- Personal Protective Equipment (PPE): Even with a dust collection system in place, providing employees with PPE, such as N-95 masks, safety glasses, and earplugs, adds an extra layer of protection.
By carefully selecting and implementing a dust and fume collection system, manufacturing industries can significantly improve air quality, protect employee health, and comply with environmental and safety regulations.
Burning Scraps: A Hidden Source of Pollution?
You may want to see also
Use industrial air filters
Industrial air filtration systems are an effective way to improve air quality and are an important part of manufacturing processes. They can be used to filter airstreams in or out of a facility, removing contaminants such as particulate matter, odours, volatile organic compounds (VOCs), nitrogen oxides, sulfur dioxide, oil mists, and metal fumes.
There are several types of industrial air filters available, including dust and fume collection systems, which are critical for maintaining good indoor air quality. These systems remove particle contaminants from the air in manufacturing facilities, workshops, and industrial complexes. The air is cleaned by passing it through an array of sealed filters, and it is then either released outdoors or recirculated, meeting the required emission limits. Dust collection systems are particularly important for companies that generate large amounts of dust particles and ambient gases, and they must comply with strict government criteria to ensure efficiency and meet EPA, NFPA, and MSHA standards.
Another type of industrial air filter is the particulate filter, which is commonly used in industries such as pharmaceuticals, research and development, defence, and food processing. This type of filter works by trapping debris, oil, dirt, and other contaminants, ensuring product integrity, reducing pollution, and maximising product safety.
By investing in high-quality industrial air filters, industries can reduce particle and chemical pollutants emitted into the air, improving workplace safety and reducing negative environmental impacts. Regular maintenance and timely replacement of filters are crucial to ensure the effectiveness of air filtration systems.
Air Pollution and Fever: Is There a Link?
You may want to see also