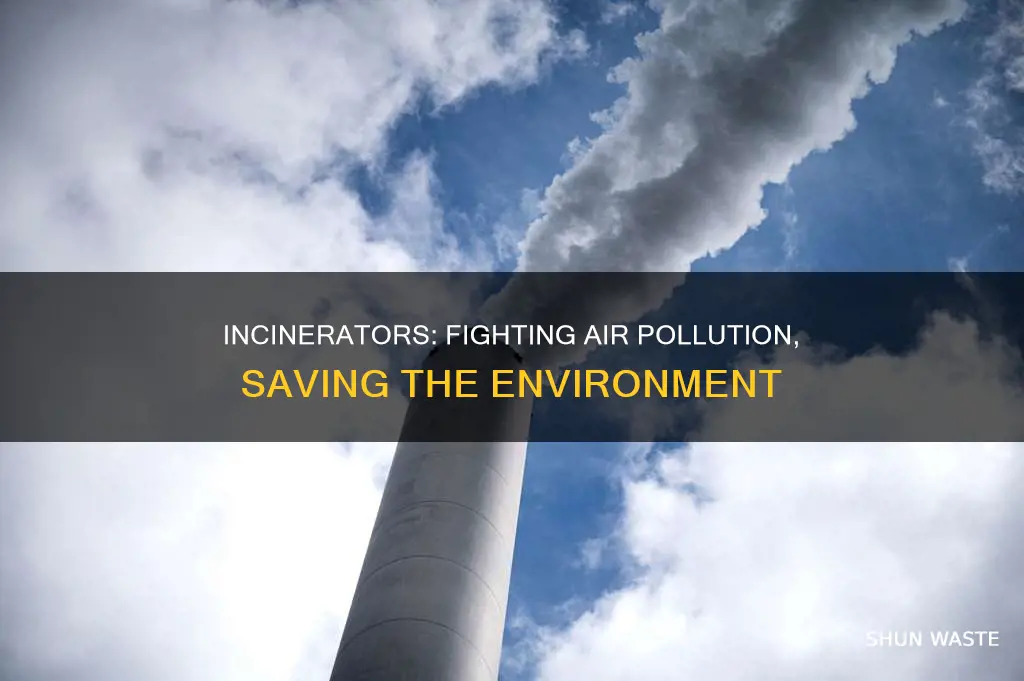
Incinerators have long been used to reduce the amount of garbage and protect people and the environment from hazardous waste. However, they have also been criticised for causing air pollution and posing health risks to nearby communities. While incinerators remain a popular waste treatment method, particularly in industrialised countries, advancements in air pollution control technology have made the process safer and reduced emissions.
Incinerators with air pollution control (APC) now include multiple redundancies for operational continuity and safety systems, as well as flue gas abatement systems to achieve strict emissions regulations. These systems aim to ensure complete combustion, flue gas cooling, and the removal of toxic elements such as sulfur oxides, carbon oxides, nitrogen oxides, polyaromatic hydrocarbons, and heavy metals.
Modern incinerators are also more energy-efficient, with the combustion process delivering significant amounts of steam that can be used to generate electricity. Additionally, the carbon dioxide produced by incinerators is a less problematic greenhouse gas than the methane produced by biodegradation in landfills.
While incinerators have their benefits, it is important to acknowledge the risks and implement proper safety measures to minimise air pollution and protect public health.
What You'll Learn
- Incinerators with Air Pollution Control (APC) systems can achieve minimal emissions while maintaining reliability and simplicity
- Incinerators with Scrubbing and Filtration systems are compliant with important regulatory standards, such as the EU Incinerator Directive
- Incinerators can be designed to ensure complete combustion, flue gas cooling, and world-leading flue gas abatement systems
- Incinerators can be equipped with auto feeders, which prevent overfeeding by operators and increase safety
- Incinerators can be designed with an optional liquid feeder, which is customised according to waste specifications
Incinerators with Air Pollution Control (APC) systems can achieve minimal emissions while maintaining reliability and simplicity
Incinerators with Air Pollution Control (APC) systems are designed to achieve minimal emissions while maintaining reliability and simplicity. They are the most advanced incinerators on the market and are designed to comply with strict regulations, such as the EU Incinerator Directive and the South African Emission Regulations. Here's how they achieve minimal emissions:
Design and Operation of the Combustion Chamber
The design and operation of the combustion chamber play a crucial role in reducing emissions. Modern incinerators are designed to ensure complete combustion, with features such as under-fire and over-fire combustion air, which improve airflow, oxygen supply, and turbulence over the waste. This results in near-complete oxidation of combustible gases. Additionally, advanced incinerators incorporate design features like arches and bull noses, which help retard the upward flow of gases, prolonging their stay in the high-temperature zone to ensure complete combustion.
Flue Gas Abatement Systems
Incinerators with APC utilize flue gas abatement systems to achieve minimal emissions. These systems may include technologies such as fabric filters, electrostatic precipitators, and scrubbers. Fabric filters, also known as baghouses, are highly effective in capturing fine particles and have been widely adopted in municipal solid-waste incineration facilities. Electrostatic precipitators (ESPs), on the other hand, use electric fields to collect particulate matter and have been commonly used in municipal solid-waste incineration facilities as well. Wet scrubbers are another technology used to remove acid gases and particulate matter from flue gases.
Continuous Feed Systems
Incinerators with continuous feed systems load waste continuously into the feeder, resulting in a more consistent flue gas flow rate. This consistency improves combustion, flue gas scrubbing, and particulate removal. While continuous feed systems have higher capital costs, they contribute to achieving minimal emissions by optimizing the combustion process.
Automated Features and Safety Measures
APC incinerators often incorporate automated features and safety measures to ensure reliable and safe operation. For example, the auto feeder system automatically feeds waste into the incinerator, reducing the risk of overfeeding by operators. Additionally, these incinerators have multiple redundancies for operational continuity and safety, including robust instrumentation to monitor the entire process.
Heat Exchangers and Gas Cooling
Heat exchangers are used to cool down the flue gas before it enters the scrubbing system. This improves the efficiency of the scrubbing process and protects downstream equipment. In some cases, a second heat exchanger may be installed to preheat the combustion air, increasing fuel efficiency and combustion efficiency.
Dry Gas Scrubbing and Heavy Metal Adsorption
Dry gas scrubbing systems are designed to neutralize acid gases and adsorb heavy metals and dioxins. Macrotec's dry gas scrubbing system, for instance, introduces a scrubber agent that neutralizes acid gases and adsorbs heavy metals without the need for water, eliminating the requirement for further water treatment.
Continuous Emission Monitoring
Continuous Emission Monitoring Systems (CEMS) are employed to continuously monitor pertinent pollutants, such as carbon monoxide, nitrogen oxides, hydrogen chloride, and particulate matter. These systems provide real-time data and facilitate the maintenance of optimal operating conditions.
Plastic Pollution: Harming Air Quality and Our Health
You may want to see also
Incinerators with Scrubbing and Filtration systems are compliant with important regulatory standards, such as the EU Incinerator Directive
Incinerators are widely used for waste management, particularly in industrialised countries such as those in the EU, US, and Japan. These countries have strict regulations regarding waste disposal through landfilling, which has made incineration a popular waste treatment option. Incinerators can reduce waste mass and volume by up to 90%, and they are also used for energy recovery.
Incineration, however, can lead to environmental and human health issues due to the release of harmful emissions. To address this, modern incinerators are designed with advanced air pollution control technologies. These technologies aim to minimise negative environmental and health impacts by achieving high standards of emission control.
One such technology is Macrotec's incinerators with Scrubbing and Filtration systems, which are compliant with important regulatory standards. These incinerators are designed to meet the EU Incinerator Directive and the South African Emission Regulations. The EU Incinerator Directive, or Directive 2000/76/EC, was issued by the European Union to set standards and methodologies for the practice and technology of incineration. The directive aimed to minimise the negative environmental and health impacts of emissions from waste incineration and co-incineration.
Macrotec's incinerators incorporate advanced combustion chamber designs, combustion air control, flue gas cooling, and world-leading flue gas abatement systems. The combustion chambers have under- and over-fire combustion air, with a 2-second retention time. This design improves airflow, oxygen provision, and turbulence, leading to enhanced combustion speed and efficiency.
The Macrotec incinerators also feature a continuous feed system, where waste is loaded continuously into the feeder, resulting in a more consistent flue gas flow rate. This improves combustion, flue gas scrubbing, and particulate removal. Additionally, the system includes an auto feeder and optional bin tipper for added convenience and safety.
To ensure the safety and reliability of the process, Macrotec's incinerators are equipped with multiple redundancies for operational continuity and safety. Robust instrumentation monitors the entire process, and flue gas abatement systems are designed for minimal emissions while maintaining simplicity and reliability. These incinerators can operate in harsh conditions with minimal maintenance, making them a reliable choice for waste management.
Air Pollution: A Dangerous Path to Respiratory Issues
You may want to see also
Incinerators can be designed to ensure complete combustion, flue gas cooling, and world-leading flue gas abatement systems
Complete combustion is ensured through the injection of air in at least two locations within the furnace: under the grate carrying burning waste (primary or underfire air) and above the grate to mix additional oxygen with the combustion gases (secondary or over-fire air). The amount of under-fire and over-fire air can be controlled manually or automatically through dampers, allowing for adjustments to be made based on combustion conditions. Additionally, the design of the furnace itself plays a crucial role in achieving complete combustion. A properly sized furnace ensures that the heat input from the waste is sufficient to maintain the required temperature for complete combustion. Newer grate systems also help improve combustion by agitating the waste, breaking it into smaller pieces, and exposing a larger surface area to air and high temperatures.
Flue gas cooling is an important step to reduce emissions of certain pollutants, such as mercury and dioxins. This is typically achieved through waste-heat boilers or direct-contact water-spray quenches. By lowering the temperature of the flue gas, the efficiency of downstream air pollution control devices is increased.
World-leading flue gas abatement systems employ a combination of technologies to remove various pollutants. Fabric filters, electrostatic precipitators, and wet inertial-impaction scrubbers are commonly used for particulate matter control. Acid gases, such as sulfur dioxide and hydrogen chloride, are removed through wet scrubbers, spray dryer absorbers, or dry-lime injection systems. For the removal of dioxins and mercury, powdered activated carbon injection systems are highly effective. By injecting finely divided activated carbon particles into the flue gas stream, pollutants are adsorbed onto their surface, and then captured in the downstream particulate control devices.
Carbon Monoxide: Secondary Pollutant Threat?
You may want to see also
Incinerators can be equipped with auto feeders, which prevent overfeeding by operators and increase safety
Incinerators are a type of furnace used for burning waste. They are an effective way to reduce the volume of waste and safeguard people and the environment from hazardous materials. Incinerators can be equipped with auto feeders, which are completely automated and prevent overfeeding by operators, thereby increasing safety.
Auto feeders only require operators to load waste into the feeder or bin tipper and engage the safety button. The system then determines when to feed, preventing overfeeding and increasing safety around the incinerator feeder. This automation also optimises incinerator loading, reduces emissions, and removes operator error.
Incinerators with auto feeders are continuous feeding systems, meaning waste is continually loaded into the feeder and incinerator. This is in contrast with batch loaders, where waste is loaded once every hour to once every eight hours. Continuous feed systems offer more effective combustion control and better emissions as the spikes in heat and flue gas associated with batch feeding can be avoided. With a continuous feed system, pre-heating between batches is not required, reducing operating costs.
Incinerators with auto feeders can also be de-ashed continuously without needing to switch off operations, saving time and fuel. Access doors are easy to open and well-insulated, allowing for easy inspection and maintenance.
Overall, auto feeders in incinerators improve safety, optimise operations, and reduce emissions and operating costs.
Water Pollution and Cancer: A Toxic Link?
You may want to see also
Incinerators can be designed with an optional liquid feeder, which is customised according to waste specifications
Incinerators are a type of furnace used for burning waste, and they can be designed with an optional liquid feeder. This feature is particularly useful for liquid waste, which can be difficult to incinerate effectively without it. The liquid feeder option is customised according to the specifications of the waste being processed, including its calorific value, viscosity, and required flow rate. This ensures optimal design and efficient incineration.
Liquid feeders are often used in conjunction with primary and secondary combustion chambers. The primary chamber burns waste with sufficient heating value to combust without auxiliary fuel, while the secondary chamber requires auxiliary fuel to control temperature and destroy toxic emissions. This two-step process is necessary for treating liquid waste, as it ensures complete combustion and the destruction of harmful substances.
The liquid feeder option is particularly relevant for hazardous liquid waste incineration. In this type of incinerator, the waste is burned directly in a burner or injected into the flame zone or combustion zone of the incinerator chamber through atomising nozzles. The atomising nozzle is critical as it converts the liquid waste into fine droplets, providing a larger surface area for combustion and rapid vaporisation.
Liquid feeders can also be used with rotary kiln incinerators, which are suitable for both liquid and solid wastes. The rotary kiln is a versatile option that facilitates the movement and mixing of waste. It is often used for hazardous waste and can handle waste with high moisture content.
Overall, the liquid feeder option for incinerators is a customisable feature that enhances the ability to process liquid waste effectively. By incorporating this option, incinerators can be designed to meet specific waste specifications, ensuring optimal performance and contributing to the prevention of air pollution by improving combustion and reducing toxic emissions.
Breathing Polluted Air: A Risk Factor for Lung Cancer?
You may want to see also
Frequently asked questions
Incinerators burn waste at extremely high temperatures, turning it into ash and heat energy. The heat energy can be used to generate electricity.
Modern incinerators are designed to prevent air pollution by ensuring complete combustion and using flue gas cooling and abatement systems. They also use air pollution control technologies to remove harmful gases and particles.
Incinerators can reduce waste volume by up to 90% and mass by up to 70%. They are also used to generate electricity, especially in industrialised countries with strict waste disposal regulations.
Incinerators can emit harmful pollutants such as nitrogen oxide, carbon monoxide, and toxic particles if not properly controlled. They also require proper disposal of the resulting ash, which can be hazardous.
Incineration is often compared to landfilling and recycling as waste disposal methods. While incineration reduces waste volume and can generate energy, it may release pollutants if not properly controlled. Landfilling has the risk of leaking harmful substances into the environment, while recycling can be selective and may not be profitable for certain materials.