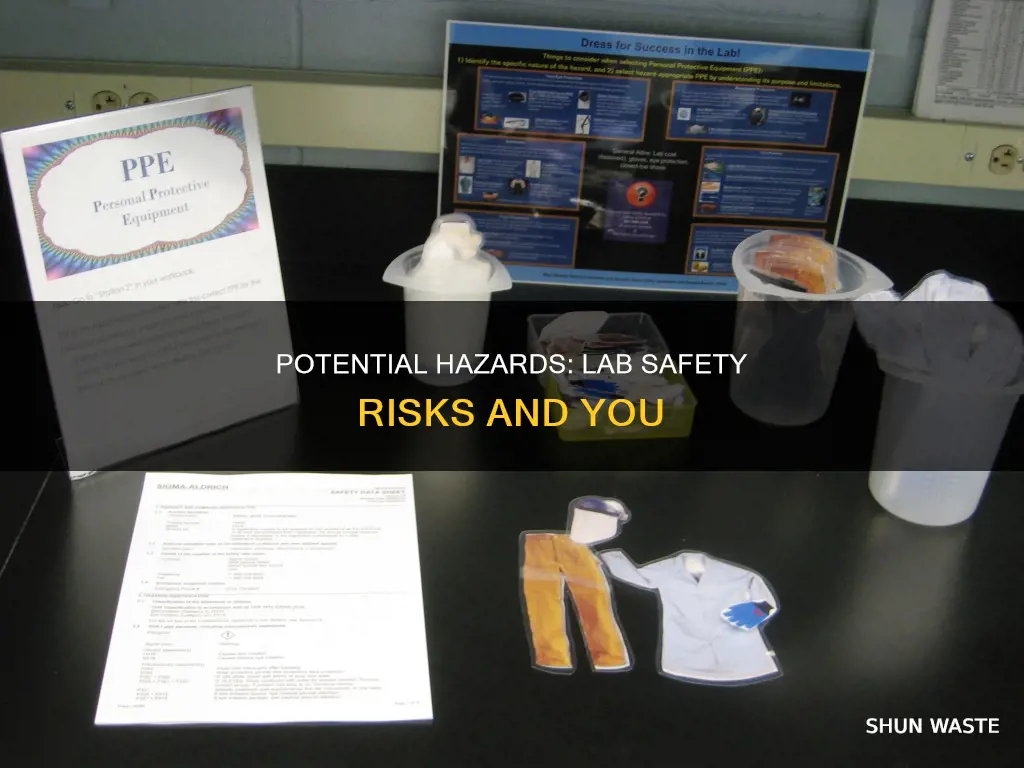
Laboratory work often involves hazardous chemicals, open flames, delicate instruments, and other potential safety risks. To ensure a safe working environment, it is crucial to identify and understand the various hazards and implement effective control measures. Some common hazards in laboratories include chemical, fire, physical, biological, and radiation risks. Chemical hazards, such as exposure to toxic substances, can lead to acute and chronic health issues, including irritation, long-term damage, and even fatalities. Fire hazards, caused by flammable materials, ignition sources, and oxygen, can result in laboratory fires, explosions, and severe burns. Physical hazards, such as slips, trips, and falls, as well as ergonomic risks from repetitive tasks, can also cause injuries. Biological hazards from blood, body fluids, and laboratory animals can pose a risk of infection, and radiation sources can have serious health consequences if not properly controlled. Proper safety measures, including training, personal protective equipment, and adherence to standards and regulations, are essential to mitigate these risks and ensure the well-being of laboratory workers.
Characteristics | Values |
---|---|
Risk Factors | Airborne pathogens, animal allergens, shedding of biohazards, aerosols and droplets, needles, scalpels, broken glass |
Protective Measures | Gloves, lab coats, safety glasses, biological safety cabinets, filtered cages, negative pressure-filtered devices, primary containment devices |
Pathogens | Hepatitis B, Mycobacterium tuberculosis, Shigella spp., Brucella spp., Salmonella spp., Leptospires, Coxiella burnetii, Rickettsia spp., Coccidioides immitis |
What You'll Learn
Toxic gases and vapours
In Assisted Conception Unit (ACU) laboratories, for example, poor air quality can negatively impact the development of human embryos and the success rate of IVF treatments. It is crucial to monitor and control air quality and VOC levels in these environments.
Chemical vapours, in particular, can be extremely dangerous. Some chemical vapours are invisible and odourless, making them difficult to detect without professional training and equipment. They can be lighter than air and rise, or heavier and sink, depending on their density. The volatility of a chemical vapour is determined by its vapour pressure, which increases with temperature. Chemicals with higher vapour pressure values are more volatile and pose greater health risks.
To mitigate the risks associated with toxic gases and vapours, laboratories should implement proper ventilation systems, such as HEPA filters, and gas detection and monitoring systems. Additionally, controlling chemical vapours involves keeping containers well-sealed during transport and storage, promptly cleaning spills, and regularly cleaning the outsides of containers. A properly operating chemical fume hood or glove box is essential for limiting exposure to chemical vapours.
Repairing Gross Polluters: Getting Your Vehicle Back on Track
You may want to see also
Chemical exposure
Additionally, it is important to implement engineering controls and safety measures to minimise the risk of exposure. This includes the use of laboratory chemical hoods and ventilation systems to prevent exposure to airborne substances. Other engineering controls may include shields, barricades, and interlocks. It is also crucial to follow basic safety rules and policies, such as wearing personal protective equipment (PPE), including gloves, lab coats, and safety glasses, to prevent skin and eye contact.
Furthermore, laboratories should establish protocols for handling and storing hazardous chemicals properly. This involves ensuring that labels on containers are not removed or defaced and that safety data sheets are readily accessible to employees. Employees should also be informed of any potential health risks associated with the chemicals they are working with and be provided with the necessary training to handle and dispose of chemicals safely.
In the event of an accident or emergency, it is crucial to be prepared. This includes knowing the specific actions to take in the event of a hazardous substance release, having easy access to emergency contact information and safety equipment, and knowing who to notify in an emergency. By following these measures, laboratories can help minimise the risk of chemical exposure and protect the health and safety of their employees.
Reducing Noise Pollution: Strategies for a Quieter Environment
You may want to see also
Fire hazards
Laboratories often contain flammable chemicals, high-powered equipment, and a complex web of electrical devices, all of which present significant fire risks. Fire hazards are prevalent in laboratories due to the wide variety of chemicals, materials, and equipment used in day-to-day operations.
Flammable chemicals are a major cause of laboratory fires. Many solvents, such as ethanol, acetone, and methanol, are highly flammable. Proper chemical storage is essential to minimise fire risk. Flammable chemicals should be stored in designated, approved flammable storage cabinets, and incompatible chemicals should be stored separately to prevent reactions that could lead to a fire. It is important to ensure that chemicals are properly labelled to avoid confusion during experiments.
Another common cause of laboratory fires is the use of hot plates and burners. Minimising the use of open flames, such as Bunsen burners, is crucial. When working with flammable or volatile chemicals, it is important to use a fume hood to contain vapours and minimise the risk of ignition. Fume hoods should be properly maintained and inspected regularly to ensure they are functioning correctly and have proper ventilation.
Electrical safety is also a key factor in preventing laboratory fires. Regular inspections of electrical equipment for signs of wear or damage are necessary. Overloading power outlets should be avoided, and all electrical devices should be properly grounded. Gas cylinders should be secure, and only one cylinder and one spare should be kept in the lab at any time.
To ensure the safety of personnel and minimise property damage, laboratories should be equipped with appropriate fire safety equipment, such as fire extinguishers, fire blankets, emergency showers, and eyewash stations. All personnel should receive fire safety training, including hands-on training in the use of fire extinguishers, to enable them to respond effectively in the event of a fire.
The Measure's Intriguing Exploration: ABD 27 54
You may want to see also
Biological hazards
Biohazards can be contained through the use of safety equipment such as biological safety cabinets or hoods. These cabinets come in three classes, with Class 1 protecting the operator, Class 2 protecting both the operator and the biological agent, and Class 3 being totally enclosed to prevent the release of airborne particles. Additionally, personal protective equipment (PPE) such as gloves, lab coats, safety glasses, and eye protection is crucial for preventing exposure to biohazards.
To further minimize the risk of biohazards, proper housekeeping practices are essential. This includes disinfecting work surfaces, proper waste disposal, and addressing spills or contamination. Emergency procedures should also be in place to contain the biological hazard and minimize the risk to people and the environment.
Furthermore, risk assessments are crucial for projects involving genetically modified organisms (GMOs) or research animals. These assessments consider the potential risk of infection to humans, animals, and the environment, and projects must receive approval before proceeding. Understanding the vocabulary associated with biological safety and the institute's safety policy is also important for laboratory staff.
Radiation exposure
To mitigate the risks of radiation exposure, laboratory personnel should be vigilant about potential radiation hazards and implement simple measures to reduce exposure. This includes the use of personal protective equipment, such as gloves, lab coats, and safety glasses, as well as ensuring proper handling and disposal of radioactive materials.
The health impacts of acute radiation exposure can be severe and include temporary or permanent sterility, hair loss, skin ulceration, radiation dermatitis, and an increased risk of cancer. The severity of health effects depends on the absorbed dose and the duration of exposure. Absorbed doses above 1-2 Gy received over a short period can lead to acute radiation syndromes, with the LD50-60 dose of around 4.5 Gy likely to result in the death of 50% of exposed individuals within 60 days without proper medical care.
It is crucial for laboratory personnel to undergo comprehensive training to recognize and manage radiation hazards effectively. This includes understanding the potential sources of radiation exposure, such as radioactive specimens, and following established protocols for handling and disposing of radioactive materials. Additionally, regular maintenance and calibration of laboratory equipment are essential to ensure accurate measurements and minimize the risk of accidental exposure.
In summary, radiation exposure poses a significant risk to laboratory personnel, and it is imperative to prioritize safety measures and awareness to mitigate potential hazards effectively. By implementing standard precautions, providing comprehensive training, and maintaining a culture of safety, laboratories can minimize the risks associated with radiation exposure and protect the health and well-being of their personnel.
Frequently asked questions
Both fire hazards and corrosive chemicals pose significant risks in a laboratory setting. Fire hazards can result in devastating incidents such as laboratory fires, explosions, severe burns, and fatalities. On the other hand, corrosive chemicals can cause severe damage to body tissue and leave the skin irritated or with chemical burns. However, the potential for harm from corrosive chemicals may be higher due to their ability to cause immediate and severe damage, especially if they are not handled safely.
Both toxic gases and open flames present serious hazards in a laboratory. Exposure to toxic gases can lead to immediate health issues such as dizziness, headaches, respiratory distress, and even death in severe cases. Open flames, such as those from Bunsen burners, can cause heat burns and increase the risk of fires or explosions if flammable materials are nearby. However, toxic gases may pose a greater risk due to their potential for silent and rapid harm, especially if ventilation is inadequate.
Ergonomic hazards and biological hazards can both significantly impact the health and safety of laboratory workers. Ergonomic hazards, such as repetitive motions and awkward postures, can lead to muscle strain, joint pain, and nerve issues. Biological hazards, on the other hand, refer to risks associated with exposure to blood, body fluids, culture specimens, and laboratory animals, which may contain infectious pathogens. While both are serious, biological hazards may pose a greater risk due to the potential for contracting severe diseases or infections.
Radiation and chemical exposure are both extremely hazardous in a laboratory setting. Radiation exposure can have serious health consequences, and laboratories using radioactive materials must be licensed and follow strict safety protocols. Chemical exposure, particularly to hazardous substances, can result in acute and chronic health issues, including toxicity, corrosivity, flammability, and reactivity. While both hazards require stringent control measures, chemical exposure may pose a greater risk due to the prevalence and variety of chemicals used in laboratories.
Carcinogenic chemicals and reproductive toxins are both hazardous to laboratory workers, particularly women of childbearing age or those who are pregnant. Carcinogenic chemicals have been linked to cancer, a leading cause of human mortality, and can have severe long-term health effects. Reproductive toxins can cause adverse effects during pregnancy, impacting both the mother and the developing fetus. The risk posed by each type of hazard depends on the specific chemicals involved and individual factors, but both require strict handling procedures to minimise potential harm.