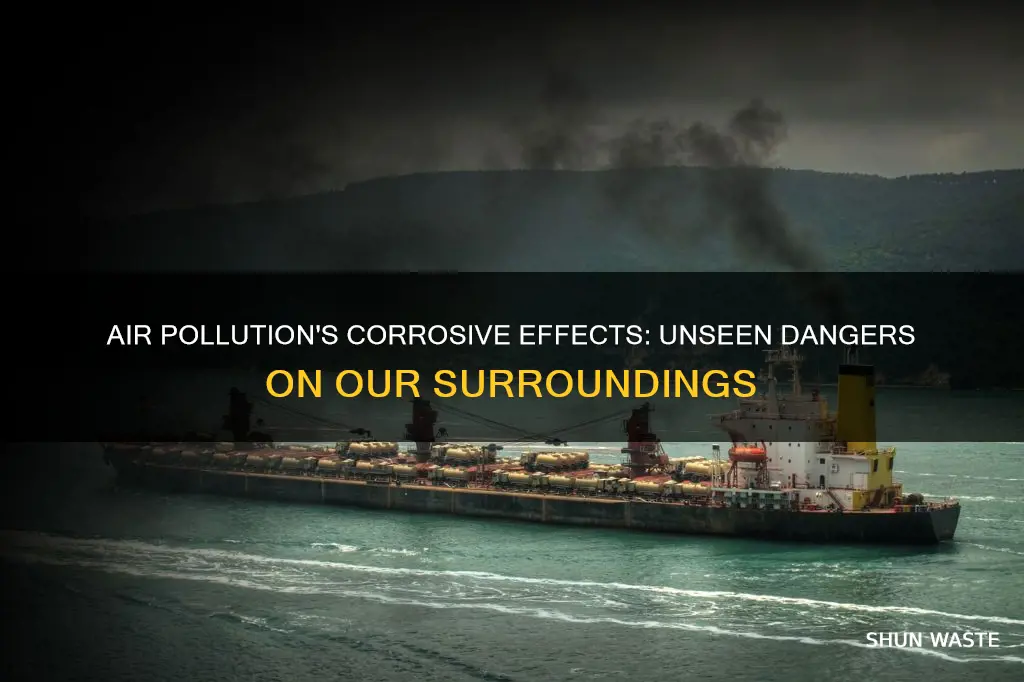
Air pollution is a significant issue that has various detrimental effects on the environment, including corrosion. Corrosion is the process of decay on a material caused by a chemical reaction with its environment. Atmospheric corrosion, the degradation of materials exposed to air and its pollutants, is the most common form of corrosion. This is caused by gaseous pollutants, which are the most destructive type of pollutant. Gaseous pollutants are primarily caused by the burning of fuels in power plants, factories, and vehicles. These pollutants include sulphur dioxide, carbon dioxide, dust, and chlorides, which have been identified as some of the biggest contributors to corrosion.
Characteristics | Values |
---|---|
Corrosive Pollutants | SO2, CO2, chlorides, dust, and humidity |
Metals Most Susceptible to Corrosion | Copper, mild steel |
Metals Least Susceptible to Corrosion | Stainless steel, aluminum, epoxy |
Pollutant Sources | Power plants, factories, heating plants, vehicle emissions, heating furnaces |
What You'll Learn
Industrial environments and gaseous pollutants
Industrial environments are rife with gaseous pollutants that can cause corrosion, particularly of electronic equipment and metal alloys. The burning of fuels in power plants, factories, and automobiles, as well as emissions from heating furnaces, contributes to the high levels of gaseous pollutants in industrial areas. These pollutants include sulphur dioxide (SO2), ozone (O3), nitrogen dioxide (NO2), and chlorides (chlorine and hydrogen chloride). Sulphur and nitrogen dioxides are byproducts of fuel burning and are of particular concern due to their corrosive nature and negative impact on health.
The presence of these gaseous pollutants in industrial settings accelerates the corrosion of metals and electronic devices. This is due to the chemical reactions that occur between the gases and the materials they come into contact with. For example, sulphur dioxide doesn't just contribute to air pollution and respiratory issues; it also actively degrades metals and other materials. The corrosive nature of these gases can be quantified and classified through reactivity monitoring, which measures the growth of corrosion films on copper and silver sensors.
Reactivity monitoring is a valuable tool for characterising the destructive potential of an industrial environment. By analysing the type and amount of corrosion films on copper and silver sensors, it is possible to identify the specific corrosive gases present. This technique is especially useful in differentiating between various classes of contaminants. For instance, silver reactivity monitoring, when used in conjunction with copper reactivity monitoring, can detect changes in gaseous pollutant levels down to 1 ppb and identify contaminants that copper alone cannot, such as chlorine.
The corrosion of circuit boards in electronic systems in industrial settings is a significant concern. Gaseous pollutants, along with factors like temperature and humidity, contribute to the deterioration of these electronic devices. To mitigate the effects of corrosion, industries employ gas filtration systems to maintain low concentrations of corrosive gases. Additionally, "free cooling" or "air-side economizers" are used to reduce the costs of cooling by allowing outdoor air to pass through filters and provide direct cooling when conditions are suitable.
Iron Mining: Pollution and Environmental Impact
You may want to see also
Corrosion monitoring and reactive monitoring
Corrosion is the gradual destruction of materials, especially metals, caused by interactions with chemicals, electrochemical reactions, friction, or other environmental factors. Gaseous pollutants, primarily from the burning of fuels in power plants, factories, and commercial and residential buildings, are a significant contributor to corrosion.
Corrosion Monitoring
Corrosion monitoring is a critical process in industries that use volatile materials, such as Oil & Gas and Petrochemicals, to prevent the degradation of assets and ensure their longevity. It involves regular data collection to track changes in specific areas of an asset over time. Monitoring focuses on specific areas of an asset, such as a boiler or pressure vessel, and is conducted more frequently than general inspections. Drones can be effectively used for corrosion monitoring, providing data that helps recommend maintenance work and mitigate damage.
The choice of sensor type and location is crucial for effective monitoring. In existing plants, corrosion experience guides the placement of sensors. However, in new applications, determining sensor locations can be challenging, and clients may need to instruct contractors on the requirement for monitoring and sensor positioning.
The corrosion rate is typically expressed in mm year−1 or mils year−1, calculated by measuring weight loss after exposure and considering factors like coupon surface area, metal density, and time of exposure. Polarization techniques and curves are also used to measure corrosion rates by extrapolating the linear portions of the curves to intersect at the natural corrosion potential.
Reactive Monitoring
Reactive monitoring, or reactivity monitoring, is an air monitoring technique that targets corrosive pollutants. It involves using copper and silver sensors to characterize the destructive potential of an environment by analyzing the growth of corrosion films. Silver, for instance, is sensitive to chlorine and can detect changes in gaseous pollutant levels as low as 1 ppb.
The reactivity rate of G1, indicating low corrosion levels, is generally considered economically feasible. However, when corrosion levels exceed the ISA G1 severity level, and the presence of sulfur oxides, chlorides, and/or active sulfur is confirmed, air treatment is necessary to remove these contaminants and prevent corrosion.
Carbon Dioxide Pollution: Impacting Our World
You may want to see also
Effects of corrosion on man-made materials
Corrosion is the degradation of materials due to their interaction with the environment. While it is primarily associated with metals, all material types are susceptible to corrosion. The level of pollutants in the air can speed up this process. Airborne contaminants such as corrosive particulate matter (PM) are created due to the chemical reactions between liquids and solids. These same liquids and solids, including salt and black carbon, can interact with the molecules within metals and accelerate decay.
Man-made materials such as metals are particularly vulnerable to corrosion. For instance, unprotected metallic alloys used in neodymium magnets can crumble into powder when exposed to salt water or acidic environments. Similarly, natural rubber is susceptible to ozone cracking, a form of corrosion caused by exposure to high carbon activities. Plastic additives can slow down this process.
The corrosion of metals in industrial environments is a significant problem. The high concentration of corrosive pollutants in the air of industrial cities accelerates the corrosion of metals and their alloys. For example, sulfur dioxide, a product of power plant and vehicle emissions, is one of the biggest contributors to corrosion. It is particularly aggressive towards copper contacts used in electronic equipment. Gaseous pollutants, which are primarily caused by the burning of fuels in power plants and factories, are the most destructive form of air pollution contributing to corrosion.
Corrosion can also affect man-made structures and equipment. For instance, aluminium plates can undergo pitting, stainless steel fasteners can experience crevice corrosion, and pipes in nuclear reactors can suffer from stress corrosion cracking. The application of protective coatings to metal surfaces can act as a barrier to corrosion. Additionally, the alteration of the environment through the addition of chemical species to inhibit corrosion is another approach to controlling corrosion in man-made structures.
Air Pollution in America: Causes and Concerns
You may want to see also
Corrosion of metals and particulate matter
Air pollution is a significant cause of corrosion, and the problem is worsening worldwide. Metals are especially vulnerable to corrosion from air pollution. Corrosive pollutants in the air include sulphur dioxide, carbon dioxide, chlorides, dust, and humidity. These pollutants are released into the atmosphere through the burning of fuels in power plants, factories, and vehicles.
Particulate matter, or suspended particulate matter (SPM), refers to tiny particles of solid or liquid matter that are suspended in the air. These particles can be made up of various substances, including heavy metals, and their sizes can range from micrometres to nanometres. Particulate matter is formed through the burning of fossil fuels, wood, and agricultural produce, as well as from dust.
Particulate matter can contribute to the corrosion of metals in several ways. Firstly, they can physically deposit onto the surfaces of metals. Due to their small size, particulate matter can quickly adsorb onto metal surfaces and form a layer. This layer can then react with the metal, leading to corrosion. For example, particulate matter containing heavy metal salts can deposit on copper surfaces, influencing the corrosion rate through the solubility of the resulting complexes in rainwater.
Secondly, particulate matter can destabilize the protective oxide films that naturally form on some metals. For instance, copper develops a thin layer of Cu2O and CuO in neutral and non-polluted environments. However, pollutants such as SO2, NOx, salinity, and SPM can destabilize this protective layer, making the metal more susceptible to corrosion.
Additionally, certain elements in particulate matter can enhance corrosion by accelerating electrochemical reactions. Lead, for example, has been observed to change the corrosion characteristics of coatings depending on the environment. In saline electrolytes, lead alloying accelerates the corrosion rate by acting as a strong cathode with respect to zinc. On the other hand, in sulfurous environments, lead forms stable and moisture-insoluble sulfate compounds that have a stifling effect on the corrosion rate.
The presence of particulate matter and corrosive pollutants in the air can have significant effects. Metals in industrial environments, such as circuit boards, are particularly at risk of corrosion due to the high levels of gaseous pollutants. Corrosion also degrades important infrastructure, including steel-reinforced highways, electrical towers, parking structures, and bridges.
To mitigate the effects of corrosion caused by particulate matter and air pollution, several strategies can be employed. Surface treatments can be applied to metals to protect them from airborne pollutants. Metal products can also be galvanized, making them highly resistant to corrosion. Additionally, high-efficiency air filters can be used to improve indoor air quality and eliminate harmful pollutants that contribute to corrosion.
Electric Oil Radiators: Do They Pollute Indoor Air?
You may want to see also
Corrosion fingerprint of locations
Corrosion fingerprinting is a technique used to identify and quantify the types and levels of corrosive chemical species present in a given environment. This is especially important in industrial environments, where circuit boards and other electronic components can be damaged by a variety of factors, including gaseous pollutants, which are the most destructive.
Reactivity monitoring is one such method of corrosion fingerprinting, which uses copper and silver sensors to detect corrosive pollutants in the air. The growth of corrosion films on these sensors can indicate the presence and levels of various corrosive chemicals, such as sulfur oxides, chlorides, and active sulfur. This technique is useful for industries that need to control the levels of corrosive pollutants in their environments, as it can provide a quantitative measure of the destructive potential of that environment.
Another method of corrosion fingerprinting is through the use of drones, which can provide high-quality visual data and accurate measurements of corroded areas. Drones like the Elios 3 can create 3D maps of corroded locations, making it easier to revisit and inspect these areas in the future. This technology is especially useful for monitoring corrosion in hard-to-reach places, improving safety and reducing costs by extending the longevity of assets.
In addition to drones, guided wave testing and magnetic flux leakage techniques can also be employed for corrosion fingerprinting. Guided wave testing uses acoustic waves to detect corrosion over long distances, making it ideal for pipelines. Magnetic flux leakage, on the other hand, involves magnetizing steel or other metals and then identifying "leaks" in the magnetic field, which indicate corrosion or damage.
The choice of corrosion monitoring technique depends on the specific requirements of the job. For example, in crude oil and wet gas production systems, it is important to place sensors in locations where they will be immersed in produced water, which is typically at the 6 o'clock position on horizontal sections. By discussing with operators of similar plants and considering the working conditions, it is possible to verify appropriate locations for corrosion monitoring sensors.
The Culprits Behind Pollution: Uncovering the Main Causes
You may want to see also
Frequently asked questions
Atmospheric corrosion is the most common form of corrosion, and it is caused by the degradation of materials exposed to air and its pollutants. The most corrosive pollutants are SO2, CO2, chlorides, and dust.
Common materials such as aluminium, brass, copper, epoxy, galvanised iron, mild steel, and stainless steel are all susceptible to corrosion. Copper and mild steel are the most corrosive metals, while stainless steel, aluminium, and epoxy are the least corrosive.
Corrosion occurs when an exposed surface comes into contact with a gas or liquid. The process is accelerated by exposure to warm temperatures, acids, and salts.