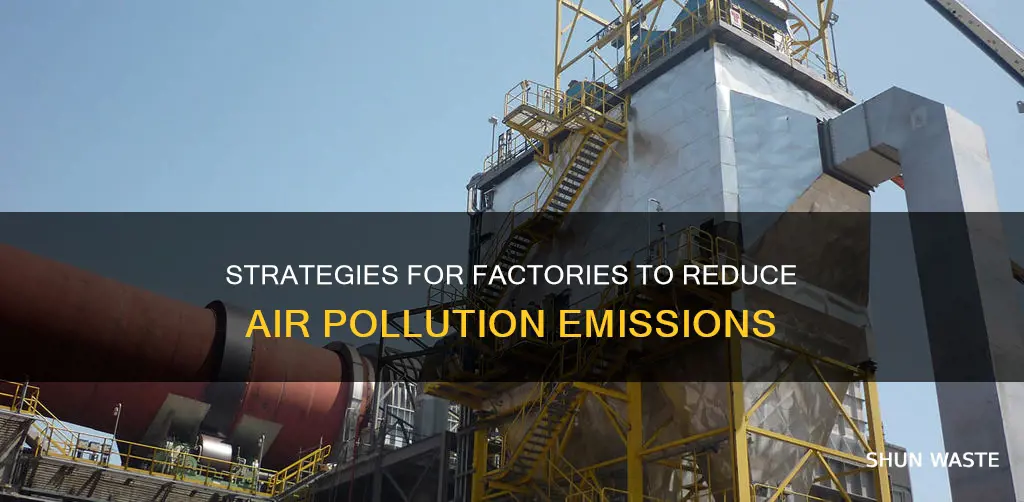
Factories contribute significantly to global emissions of pollutants such as sulphur dioxide and particulate matter. There are two basic options for controlling air pollution: pollution prevention and pollution control. Pollution prevention involves changing the factory's operations so that it creates little or none of a particular pollutant. For example, a factory can switch from coal to natural gas fuel, which can dramatically reduce emissions of mercury, particulates, greenhouse gases, and other contaminants. Pollution control involves implementing and maintaining effective methods and equipment to improve air quality and working conditions. This includes improving energy efficiency, installing pollution control devices, and ensuring regulatory compliance.
Characteristics | Values |
---|---|
Pollution prevention | Changing factory operations to reduce or eliminate a particular pollutant |
Pollution control | Using cleaner technologies, installing pollution control devices, improving energy efficiency, and investing in R&D |
Air quality monitoring | Using devices to monitor indoor and outdoor air quality in real-time |
Regulatory compliance | Ensuring factories meet air quality standards and regulations |
Energy efficiency | Optimising energy use in buildings, manufacturing processes, and transportation to reduce emissions |
Cleaner technologies | Switching from coal to natural gas fuel to reduce emissions of mercury, particulates, and greenhouse gases |
What You'll Learn
- Pollution prevention: changing operations to create little or none of a particular pollutant
- Pollution control: reducing emissions of mercury, particulates, greenhouse gases, etc
- Cleaner technologies: using less toxic materials
- Air filtration systems: reducing pollutants at the source
- Regulatory compliance: ensuring factories follow air quality standards
Pollution prevention: changing operations to create little or none of a particular pollutant
Factories can prevent pollution by changing their operations to create little or none of a particular pollutant. For example, a cadmium plating factory can switch to a different plating process that doesn't use cadmium. Factories that switch from coal to natural gas fuel can also dramatically reduce emissions of mercury, particulates, greenhouse gases, and other contaminants such as sulphur.
Another way to prevent pollution is to reduce pollutants at the source. This can be done by improving energy efficiency, which optimises energy use in buildings, manufacturing processes, and transportation to reduce energy consumption and emissions. Factories can also install pollution control devices and ensure regulatory compliance.
It is also important to control the dust generated by manufacturing operations to maintain appropriate indoor air quality (IAQ). Implementing and maintaining effective methods and equipment appropriate for your industry can improve air quality and working conditions for all parties concerned. Regular monitoring of air quality with devices that provide real-time and accurate data can help determine whether specific safety precautions, such as breathing masks and PPE, are necessary.
Protecting Animals from Pollution: Strategies for Conservation
You may want to see also
Pollution control: reducing emissions of mercury, particulates, greenhouse gases, etc
Factories can implement a number of measures to control air pollution and reduce emissions of mercury, particulates, and greenhouse gases.
The first option is pollution prevention, which involves changing the factory's operations so that it creates little or none of a particular pollutant. For example, a factory can prevent cadmium pollution by switching to a plating process that doesn't use cadmium. Similarly, factories can switch from coal to natural gas fuel, which can dramatically reduce emissions of mercury, particulates, and greenhouse gases.
The second option is pollution control, which includes implementing air filtration systems and using cleaner technologies. Factories can also improve energy efficiency by optimising energy use in buildings, manufacturing processes, and transportation to reduce energy consumption and emissions. Regular monitoring of air quality is essential to maintain appropriate indoor and outdoor air quality. Devices such as Oizom can provide real-time and accurate data on air quality, helping to determine if safety precautions like breathing masks and PPE are necessary.
Additionally, factories should ensure regulatory compliance and invest in research and development to further improve air quality and reduce emissions. By implementing these measures, factories can proactively improve and preserve air quality, creating a more sustainable environment.
Solar Power: Pollution Solution with Energy Revolution
You may want to see also
Cleaner technologies: using less toxic materials
Cleaner technologies are an important part of reducing air pollution from factories. By using less toxic materials, factories can significantly reduce their environmental impact. For example, a cadmium plating factory can switch to a different plating process that doesn't use cadmium, a highly toxic metal. This simple change can prevent cadmium pollution entirely. Similarly, factories that switch from coal to natural gas fuel can dramatically reduce emissions of mercury, particulates, greenhouse gases, and other contaminants such as sulphur.
Another way to reduce pollution is to improve energy efficiency. This can be done by optimising energy use in buildings, manufacturing processes, and transportation, which will reduce energy consumption and emissions. Factories can also invest in research and development to find new, cleaner technologies and processes that reduce pollution.
It is also important for factories to monitor their air quality regularly. This can be done with devices that provide real-time and accurate data on the air quality. With this information, factories can determine whether specific safety precautions, such as breathing masks and PPE, are necessary to protect workers and the environment.
Overall, by using less toxic materials and implementing cleaner technologies, factories can make a significant impact on reducing air pollution and creating a more sustainable future.
Trash Pollution: Reducing the Impact, Saving the Planet
You may want to see also
Air filtration systems: reducing pollutants at the source
Air filtration systems are an important part of reducing pollutants at the source in factories. Factories contribute significantly to global emissions of pollutants like sulphur dioxide and particulate matter.
One way to reduce these emissions is to improve energy efficiency. This can be done by optimising energy use in buildings, manufacturing processes and transportation to reduce energy consumption and emissions. Factories can also switch from coal to natural gas fuel, which can dramatically reduce emissions of mercury, particulates, greenhouse gases and other contaminants such as sulphur.
Another way to reduce emissions is to install pollution control devices. These can include air filtration systems, which can be used to reduce pollutants at the source. Regular monitoring of air quality is also important, and this can be done with devices that provide real-time and accurate data on the air quality. This information can then be used to determine whether specific safety precautions, such as breathing masks and PPE, are necessary.
Overall, by implementing and maintaining effective methods and equipment, factories can improve air quality and working conditions for all concerned.
River Pollution: Understanding the Sources and Impacts
You may want to see also
Regulatory compliance: ensuring factories follow air quality standards
Factories can implement a range of measures to control air pollution and ensure regulatory compliance with air quality standards.
One approach is pollution prevention, which involves changing factory operations to reduce or eliminate the emission of specific pollutants. For example, a factory may switch to a different plating process that does not use toxic materials like cadmium. Similarly, factories can transition from coal to natural gas fuel, significantly reducing emissions of mercury, particulates, greenhouse gases, and contaminants such as sulphur.
Another strategy is pollution control, which includes the use of cleaner technologies and the installation of pollution control devices. This can involve implementing air filtration systems to reduce pollutants at the source and improve indoor air quality. Regular monitoring of air quality is essential, and devices like Oizom can provide real-time, accurate data to determine if safety precautions are necessary.
Additionally, improving energy efficiency can play a crucial role in reducing pollution. This involves optimising energy use in buildings, manufacturing processes, and transportation to lower energy consumption and emissions. Factories can also invest in research and development (R&D) to identify and implement more sustainable practices and technologies.
By combining these strategies, factories can effectively control air pollution, comply with air quality standards, and contribute to a more sustainable future.
Airborne Threats: Pollutants and Anaphylaxis Risks
You may want to see also
Frequently asked questions
Factories can prevent air pollution by changing their operations so that they create little or none of a particular pollutant. For example, a cadmium plating factory can prevent cadmium pollution by switching to a different plating process that doesn’t use cadmium. Factories that switch from coal to natural gas fuel can also dramatically reduce emissions of mercury, particulates, greenhouse gasses, and other contaminants such as sulphur.
Factories can control air pollution by improving energy efficiency, using cleaner technologies, installing pollution control devices, ensuring regulatory compliance, and investing in R&D.
Factories can monitor air quality by using devices that provide real-time and accurate data on the air quality. With this information, factories can determine whether or not specific safety precautions, such as breathing masks and PPE, are necessary.