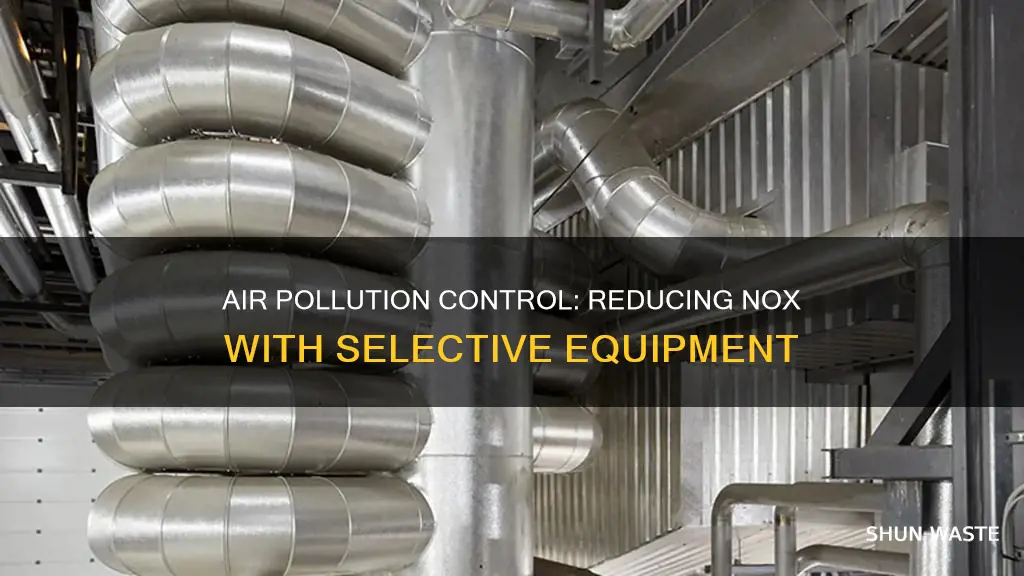
Nitrogen oxides (NOx) are formed from the combustion of fossil fuels and have significantly negative environmental impacts. NOx gases are produced primarily from fuel combustion in mobile and stationary sources, such as automobiles and coal-fired power plants. The combustion of gasoline in automobiles emits nitrogen oxides into the atmosphere, while stationary emissions come from coal-fired power plants and electric power plant boilers. To reduce NOx emissions, various strategies and technologies can be employed, such as fuel switching, flue-gas recirculation, low NOx burners, derating, steam or water injection, staged combustion, fuel reburning, reduced-oxygen concentration, selective catalytic reduction, and selective non-catalytic reduction. These techniques aim to minimize NOx formation by reducing flame temperature, lowering excess air, and burning low-nitrogen-containing fuels.
What You'll Learn
Natural gas reburning
Field evaluations of NGR on full-scale utility boilers have shown promising results, with NOx reductions ranging from 40% to 75%. This makes NGR a viable option for facilities looking to reduce NOx emissions from their combustion equipment. However, it is important to note that the selection of an appropriate NOx reduction technique will depend on various factors, including the type of facility, site-specific conditions, and economic considerations.
NGR is particularly effective in reducing NOx emissions and has several advantages over other techniques. It is a relatively simple and economical method that does not require significant modifications to the existing combustion system. NGR can be applied to a wide range of combustion sources and can achieve high NOx reduction efficiencies.
When selecting an NOx reduction strategy, it is crucial to consider the specific requirements and constraints of the facility. Factors such as fuel type, combustion temperature, and regulatory compliance should be carefully evaluated to determine the most suitable technique. Additionally, the potential increase in emissions of other pollutants and the economic viability of the chosen strategy should also be considered.
Overall, NGR is a proven and effective method for reducing NOx emissions from combustion sources. By injecting natural gas above the primary combustion zone, NGR creates conditions that promote the conversion of NOx into molecular nitrogen, resulting in significant NOx reductions. This technique is a valuable tool in the effort to improve air quality and meet regulatory standards.
Sediment Pollution: Reducing Its Impact on Our Environment
You may want to see also
Flue gas recirculation
FGR is particularly effective for natural gas boilers with outputs between 500 kW and 32 MW. The London Plan, for example, has placed planning requirements on major developments within the Greater London Authority (GLA) to use gas boilers with a NOx rating of less than 40mg·kWh–¹. FGR is a practical and cost-effective solution for boilers in this output range.
The basic principle behind FGR is to reduce the flame temperature by adding non-reactive gases such as carbon dioxide, nitrogen, or steam to the burner. By adding about 10% of flue gas into the flame, the temperature is reduced by approximately 7%. This reduction in temperature lessens the production of NOx.
FGR is also used for temperature regulation in boilers. Boilers operate across a range of fuel rates but must produce steam at a constant temperature. FGR increases the flow rate and heat transfer through the superheater coils, ensuring a constant temperature. This application of FGR has been common for over a hundred years, even on large boilers.
FGR is specifically effective in reducing thermal NOx formation. It does so by diluting the fuel-air mix with relatively inert gases, thereby reducing the flame temperature. This prevents diatomic nitrogen and oxygen in the fuel-air mix from reacting to form NOx. However, it is important to note that FGR is not effective in reducing fuel NOx, which is formed from the nitrogen in the fuel.
In summary, flue gas recirculation is a well-established technology that offers a practical and cost-effective solution for reducing NOx emissions, particularly in natural gas boilers. By recirculating flue gases and reducing flame temperatures, FGR effectively lowers NOx formation without significantly impacting energy efficiency.
Reducing Pollution: Increasing Carry Capacity for a Greener Future
You may want to see also
Low-NOx burners
- Recirculation Zones: Low-NOx burners induce recirculation zones within the combustion chamber, which helps mix the fuel and air more effectively, reducing the peak flame temperature and the formation of NOx.
- Staging Combustion Zones: By dividing the combustion process into multiple zones, low-NOx burners can control the amount of oxygen available in each zone, optimising combustion and minimising NOx formation.
- Reducing Local Oxygen Concentrations: Lowering the oxygen concentration at the burners is a critical strategy to reduce NOx. This can be achieved by diluting the combustion air with flue gas or another inert gas.
- Surface Stabilised Combustion: This technique, used by ALZETA, involves premixing fuel and air to achieve uniform heating and operating at minimum combustion temperatures. This method ensures complete and uniform combustion, even at the lean conditions necessary for ultra-low NOx emissions.
- Radiant Burners: Ceramic-fibre burners are used when ultra-low NOx, low heat flux, and uniform heating are required. These burners improve heat transfer and system efficiency while complying with low-emission requirements.
Applications
- Utility Boilers: Used to produce steam and electricity, low-NOx burners can be installed in utility boilers to reduce NOx emissions.
- Gas-Fired Unflued and Flued Gas Heaters: Low-NOx burners can be used in gas-fired heaters, improving energy efficiency and indoor air quality by reducing NOx emissions.
- Gas-Fired Storage Water Heaters: Low-NOx burners can be applied in storage water heating systems to reduce NOx emissions and improve energy efficiency.
- Industrial and Commercial Boilers: In many areas, ultra-low NOx burners are required for industrial and commercial boilers. These burners can deliver less than 7 ppm NOx in most applications.
- Gas Turbines: ALZETA's nanoSTAR injector can be used in gas turbines to achieve under 3 ppm NOx with only modest modifications to the turbine's combustion section.
Mitigating Pollution: Strategies for Air, Water, and Land
You may want to see also
Selective catalytic reduction
The SCR process is highly effective, with commercial systems reducing NOx by up to 95%. It is commonly used in large utility boilers, industrial boilers, and municipal solid waste boilers, as well as diesel engines in ships, locomotives, and automobiles. SCR systems are now the preferred method for meeting diesel emissions standards for heavy trucks, cars, and light commercial vehicles, resulting in significant reductions in NOx, particulates, and hydrocarbon emissions.
The key to the SCR process is the use of a catalyst, which can be made from various porous ceramic materials such as titanium oxide. The catalyst increases the rate of the NOx conversion reaction, which depends on the NO2:NO ratio. Different SCR catalysts, such as vanadium oxide or metal-substituted zeolites, have different operating temperature windows and other properties, so they must be carefully selected for each specific application.
The SCR reaction typically occurs as the gases pass through the catalyst chamber. The reductant, such as ammonia or urea, is injected and mixed with the gases before they enter the chamber. The chemical equation for this reaction is:
2 NO + 2 NH3 + 1/2 O2 -> 2 N2 + 3 H2O
The ideal temperature range for the SCR reaction is between 630 and 720 K (357 and 447 °C), but it can operate as low as 500 K (227 °C) with longer residence times. The minimum effective temperature depends on factors such as fuel type, gas constituents, and catalyst geometry.
One of the advantages of SCR technology is the variety of reductants that can be used. In addition to anhydrous and aqueous ammonia, urea (CO(NH2)2) is commonly used and is considered safer to store. However, it requires thermal decomposition to convert it into ammonia. Other possible reductants include cyanuric acid and ammonium sulfate.
The choice of catalyst is also critical to the SCR process. Base metal catalysts, such as vanadium and tungsten, are less expensive and perform well within the temperature ranges commonly used in industrial and utility boiler applications. However, they lack high thermal durability. Zeolite catalysts, on the other hand, can operate at substantially higher temperatures and have a lower potential for SO2 oxidation, reducing the risk of corrosion.
Overall, SCR technology has been widely adopted due to its effectiveness in reducing NOx emissions and its flexibility in terms of reductant and catalyst options. However, it is important to carefully select the appropriate reductant and catalyst for each specific application to ensure optimal performance and minimize ammonia slip, which refers to unreacted ammonia passing through the SCR.
Electric Cars: Reducing Air Pollution, Improving Our Future
You may want to see also
Overfire air combustion modification
Overfire air (OFA) is a common practice in pulverized coal combustion for reducing NOx emissions without compromising combustion efficiency. In opposed wall-firing boilers, a single-level arrangement of OFA nozzles aligned with swirl burners is typically used. However, a two-level staggered arrangement with wide spacings between nozzles and a doubled flow ratio in the upper level has been found to be more effective in reducing NOx emissions. This arrangement allows stronger upper-level jets to penetrate deeper into the central region, while weaker lower-level jets cover the near-wall region. This setup results in improved mixing with hot gas from the burner zone, leading to a more uniform flow and temperature distribution in the upper furnace.
The effectiveness of NOx reduction in single-level OFA setups depends on the OFA position and the OFA ratio. Increasing the OFA ratio and distance from the burner zone reduces NOx emissions but increases the carbon content in fly ash. On the other hand, a lower OFA position reduces NOx emissions but increases the carbon content in fly ash.
The introduction of separated-over-fire air (SOFA) has been shown to be effective in reducing NOx emissions. In a study on a 500 MW retrofit boiler, the combination of corner SOFA (70%) and clockwise wall SOFA (30%) resulted in a 66% reduction in NOx emissions. Another study on a 600 MWe down-fired boiler found that the introduction of SOFA, along with moving fuel-lean nozzles and rearranging the staged air, achieved a 50% reduction in NOx emissions without a significant increase in carbon content in fly ash.
Overall, the optimal arrangement of OFA and SOFA nozzles, as well as the flow ratios, are crucial in achieving efficient combustion and reducing NOx emissions in industrial-scale boilers.
Strategies to Reduce Pollution in Micropolis
You may want to see also
Frequently asked questions
There are several equipment types and strategies that can be used to reduce NOx emissions. Here are some of the most common and effective ones:
- Fuel switching: Switching to a fuel with a lower nitrogen content, such as natural gas, is a simple and economical way to reduce NOx emissions.
- Flue-gas recirculation (FGR): This technique involves recirculating a portion of the flue gas back into the combustion chamber to reduce temperature and oxygen concentration, inhibiting NOx formation.
- Low NOx burners: Specially designed burners that limit NOx formation by reducing peak flame temperature and local oxygen concentration.
- Derating: Reducing the output of industrial boilers or furnaces to decrease flame temperature and NOx formation.
- Steam or water injection: Injecting water or steam into the flame lowers the temperature and reduces the formation of thermal and fuel-bound NOx.
- Staged combustion: Creating fuel-rich and air-rich zones, either before or after the primary combustion zone, to reduce NOx emissions.
- Natural gas reburning (NGR): A three-stage burning process that ensures complete combustion of the primary fuel, reducing the formation of nitrogen dioxide.
- Selective catalytic reduction (SCR): A post-formation control technology that uses a catalyst and ammonia to convert NOx into nitrogen and water.
- Selective non-catalytic reduction (SNCR): A similar process to SCR but without the use of a catalyst, SNCR injects ammonia or urea into the flue gas at high temperatures to break down NOx into nitrogen and water.
The choice of equipment and strategy depends on various factors, including the specific facility, site conditions, and economic considerations.
NOx emissions have detrimental effects on both the environment and human health. In the environment, NOx gases:
- Increase the greenhouse effect and contribute to global warming.
- Form ground-level ozone, which is a potent toxin and has serious health implications for humans.
- Cause smog and acid rain, harming plants, trees, and aquatic life.
In terms of human health, people exposed to NOx emissions for prolonged periods may experience:
- Respiratory problems, including lung tissue damage and worsened asthma.
- Increased risk of breast cancer.
- Irreversible damage to the respiratory system from high levels of nitrogen dioxide (NO2).
NOx emissions are generated from both domestic and industrial sources, with the most common sources being:
- Power generation plants
- Construction equipment
- Sea vessels and marine equipment
- Metal finishing procedures
- Residential oil and gas combustion
- Automobile combustion engines
- Coal-fired power plants
- Electric power plant boilers
Fuel switching involves replacing a fuel with high nitrogen content with one that has a lower nitrogen content or is nitrogen-free. This is effective because fuel-bound NOx formation is dependent on the nitrogen content of the fuel. By switching to a lower nitrogen fuel, such as natural gas, you can significantly reduce NOx emissions. This strategy is simple to implement and can be an economical way to meet emission reduction goals.