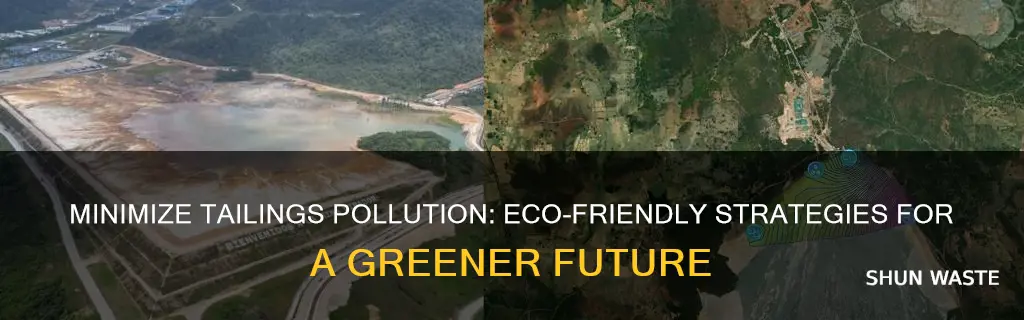
Tailings are a major cause of pollution and can be challenging to manage and dispose of, as seen in the game Eco. While complete pollution prevention is impossible, there are strategies to mitigate tailings pollution. Burial is key, and the depth of burial makes a significant difference, with deeper burials resulting in less leakage. Additionally, different disposal methods, such as dumping tailings into water or storing them in vehicles, can affect pollution levels. Players must balance the need to address pollution with the tedious and time-consuming nature of tailings disposal.
Characteristics | Values |
---|---|
Burial | The deeper you bury tailings, the less leakage occurs. At 25-30 blocks below the surface, pollution leakage is small. |
They pollute ~50% less for every 5 blocks down you bury them. | |
They must be buried under solid blocks (not rubble, e.g. stone). Dirt is the most economical choice. | |
Storing in vehicles | Storing tailings in vehicles is possible, but they will emit pollution as if they were not mitigated at all, even if the vehicles are buried. |
Dry stacking | A replacement for the current method of burying tailings. Tailings are dewatered to reduce their size, compacting them so they require less area. |
Refining | Reducing tailings further by extracting valuable remaining minerals at the cost of energy, another specialised material and time. |
What You'll Learn
Bury tailings underground
One effective method to reduce tailings pollution and its environmental impact is to bury the tailings underground. This approach offers several advantages and can be a sustainable solution when properly implemented. Here are the key steps and considerations for burying tailings underground:
Site Selection and Preparation
The first step is to identify a suitable site for burying the tailings. This location should be carefully chosen to minimize environmental risks and ensure long-term stability. Ideal sites are typically old mines or quarries that are no longer in use, as these areas have already been disturbed and can accommodate the volume of tailings without causing additional ecological damage.
Once the site is selected, it must be prepared by clearing the area and removing any vegetation or debris. The ground may need to be leveled and compacted to create a stable base for the tailings deposit.
Containment and Engineering Controls
To prevent pollution and minimize the risk of contamination, engineered containment systems are constructed. These systems are designed to isolate the tailings from the surrounding environment, preventing leaching and the escape of contaminants. Common containment methods include:
- Lined Ponds or Impoundments: Creating a pond or impoundment lined with impermeable materials, such as clay or synthetic liners, to contain the tailings.
- Tailings Cells: Constructing engineered cells or pits, often lined and capped, to store tailings in a controlled manner.
- Underground Injection: Injecting tailings into deep, stable rock formations, ensuring long-term containment.
These containment systems are designed with multiple layers of protection, including liners, leachate collection systems, and monitoring wells, to detect and prevent any potential leaks.
Tailings Deposition and Cover
After the containment system is in place, the tailings can be transported and deposited into the designated area. This process should be carefully managed to avoid spills or releases during transportation. The tailings are then spread and compacted in layers to ensure stability and minimize air emissions.
Once the tailings are in place, a final cover is installed to provide additional protection and help with the rehabilitation of the site. This cover typically consists of several layers, including a protective layer of soil, a vegetative layer to promote plant growth, and sometimes a geosynthetic layer for added protection against erosion and infiltration.
Monitoring and Maintenance
Even after the tailings are buried, ongoing monitoring and maintenance are crucial to ensure the long-term integrity of the containment system. Regular inspections, maintenance of erosion control measures, and monitoring of groundwater and surface water quality are essential to detect any potential issues and mitigate risks.
Proper record-keeping and long-term planning are also vital to ensure that the site is properly managed and maintained, even over extended periods. This includes documentation of the tailings composition, site engineering, and any potential future uses or impacts of the site.
By following these steps and employing best practices, burying tailings underground can be a safe and effective method to reduce tailings pollution and minimize their environmental footprint. It offers a sustainable solution by isolating the tailings from the environment, rehabilitating disturbed land, and providing long-term stability with proper management and monitoring.
Nitrogen Dioxide Pollution: Strategies for Reduction and a Greener Future
You may want to see also
Store tailings in clay
Storing tailings in clay is one method to reduce tailings pollution. Tailings are pollution-causing blocks that are created when using machinery such as the Screening Machine, Froth Floatation Cell, or Sensor-Based Belt Sorter to create Concentrated Ores. These tailings will leak pollution into their surroundings if not stored correctly.
One way to mitigate this pollution is by burying the tailings under a significant amount of material. This can be done by burying them in clay. The depth of the burial is crucial, as the pollution leakage decreases as the depth increases. By burying the tailings 25-30 blocks below the surface, the pollution leakage is significantly reduced. For every 5 blocks down you bury the tailings, they will pollute 50% less. Therefore, at a depth of 10 blocks, they will produce only 25% of their pollution, and at 15 blocks, this decreases to 12.5%.
It is important to note that the tailings must be buried under solid blocks, such as dirt or clay, and not rubble like stone. The burial hole does not need to be lined with any specific block and can be open as long as there are blocks above the tailings. Additionally, the area above the tailings does not need to be solid, as only the highest block above them counts for depth.
By storing tailings in clay and burying them at a sufficient depth, the pollution leakage can be effectively reduced.
Strategies to Reduce Smog and Air Pollution
You may want to see also
Put tailings in a waste pit
Putting tailings in a waste pit is a common method for dealing with mining waste. This process is known as in-pit tailings storage and involves backfilling abandoned open-pit surface mines with tailings. This method is attractive to mine operators as it is a cost-effective way to fill worked-out voids, and the tailings do not require retaining walls. Additionally, it is preferred by aboriginal stakeholders in Australia, where remote mining operations have used in-pit storage for decades.
However, one significant disadvantage of in-pit storage is the potential for groundwater contamination. To mitigate this risk, some operations have installed underdrainage systems to control and recover seepage from the deposited tailings. Other disadvantages include rapid rates of rise, especially during the early stages of deposition, which can result in low strength and poor consolidation properties of the tailings.
Another important consideration is the stability of underground mines near an in-pit tailings facility. The weight of the overlaying tailings may cause convergence in underground roadways, and liquefied tailings can rush into underground voids, leading to catastrophic consequences. An example of this is the Mufulira disaster of 1970, where a tailings inrush caused the deaths of 89 miners.
To address the issue of groundwater contamination, environmental laws in some jurisdictions may forbid or control the backfilling of pits to prevent excess groundwater contamination. Additionally, groundwater bores may need to be installed around the pit to monitor seepage plumes, and in some cases, it may be necessary to pump out the seepage to prevent contamination.
Overall, while in-pit tailings storage can be a cost-effective solution for mine operators, it is essential to carefully consider the potential risks and implement appropriate measures to mitigate negative environmental impacts, especially groundwater contamination.
Phoenix Air Pollution: Strategies for Cleaner Air
You may want to see also
Recycle tailings
Recycling tailings is a sustainable solution to the environmental challenges posed by mining activities. Here are some ways to recycle tailings:
Resource Recovery
Tailings may contain valuable minerals such as gold, silver, and copper that were not fully extracted during the initial mining process. Through reprocessing, these minerals can be further extracted, maximising resource utilisation and enhancing the economic benefits of mining activities. This not only reduces the environmental impact of mining but also optimises resource utilisation and potentially extends the economic life of mining operations.
Environmental Protection
Untreated tailings can contain harmful chemicals that can lead to water pollution and ecosystem damage. By reprocessing tailings, the release of hazardous substances can be reduced, minimising the negative impact on the surrounding environment. This aligns with sustainable mining practices and helps mining companies comply with strict environmental regulations and social responsibility standards.
Improved Tailings Dam Stability
Reprocessing tailings can reduce the volume and weight of tailings by extracting valuable minerals. This, in turn, alleviates pressure on tailings dams, contributing to their stability and helping to prevent disasters such as tailings dam failures.
Extended Mine Life
Reprocessing tailings enables more efficient resource utilisation, thereby extending the lifespan of a mine. This is strategically significant for supporting long-term sustainable mining operations.
Construction Materials
Research has shown that iron tailings can be used to develop stronger and cheaper building bricks that have broad application prospects. Tailings can also be used as raw materials for preparing ceramics, composite materials, crystallised glass, lightweight materials, and optical products. Additionally, after secondary recycling, tailings can be used as raw materials for ceramics, cement, and other construction materials based on their physical and chemical properties.
Mineral Fertilizer or Soil Conditioner
Some mine tailings contain elements such as iron, phosphorus, zinc, and copper, which are essential for plant growth and development. Through proper processing, mineral tailings can be used to produce mineral fertilisers that improve soil quality. This not only enhances soil magnetism but also modifies the structure of magnetic particles in the soil, ultimately reducing air permeability and porosity.
Backfilling Mine Goaf Areas
Tailings can be mixed with cement and other consolidating materials to create a slurry that can be transported underground to fill mined-out areas. This helps to stabilise the ground and prevent surface subsidence and water leakage, which can pose significant risks to human survival.
Reducing Noise Pollution for Happier, Healthier Festivals
You may want to see also
Store tailings in a vehicle
Storing tailings in a vehicle is not an effective way to reduce tailings pollution. While it is possible to store tailings in vehicles, they will emit pollution as if they were not mitigated at all, even if the vehicles are buried. Therefore, storing tailings in vehicles is not a recommended method for reducing tailings pollution.
Tailings are the materials left over after separating the valuable fraction from the uneconomic fraction of an ore during the mining process. They often contain toxic chemicals such as heavy metals, sulfides, and radioactive content, making them a dangerous source of pollution. The pollution caused by tailings can have detrimental effects on the environment and surrounding communities.
To reduce tailings pollution, it is crucial to properly manage and store them. One effective method is to bury them under a significant amount of solid material, such as dirt or stone. The deeper the tailings are buried, the less leakage will occur. For example, at a depth of 25-30 blocks below the surface, pollution leakage is significantly reduced.
Additionally, there are other methods to mitigate tailings pollution, such as dry stacking, where tailings are dewatered to reduce their size and compacted to require less storage area. Another method is wet tailings storage, where tailings are dissolved in water ponds made by players and completely surrounded by solid materials to contain the pollution.
It is important to note that there is no way to completely prevent tailings pollution. However, by utilizing proper storage and disposal methods, the environmental impact of tailings can be minimized.
Energy Conservation: Reducing Pollution, Saving Our Planet
You may want to see also
Frequently asked questions
There is no way to completely prevent pollution from tailings in Eco. However, you can mitigate the amount of pollution by burying tailings under a significant amount of solid material. The deeper you bury them, the less leakage occurs.
Burying tailings in clay can help to stop the spread of pollution. You can also store tailings in a clay pond made by players that is completely surrounded by solid materials. This will contain the pollution and prevent it from affecting the surrounding area.
While you can store tailings in vehicles, they will emit pollution as if they were not mitigated at all, even if the vehicles are buried. To properly store tailings, they must be taken out of the vehicle inventory and buried in stockpiles or placed individually on the ground.
One method of disposing of tailings is to dump them into water, where they will dissolve and cause pollution to propagate downstream. Another method is to put tailings into mines or other contained areas, such as open-top storage. You can also try "dry stacking" tailings by dewatering them to reduce their size and compacting them so they require less area for storage.