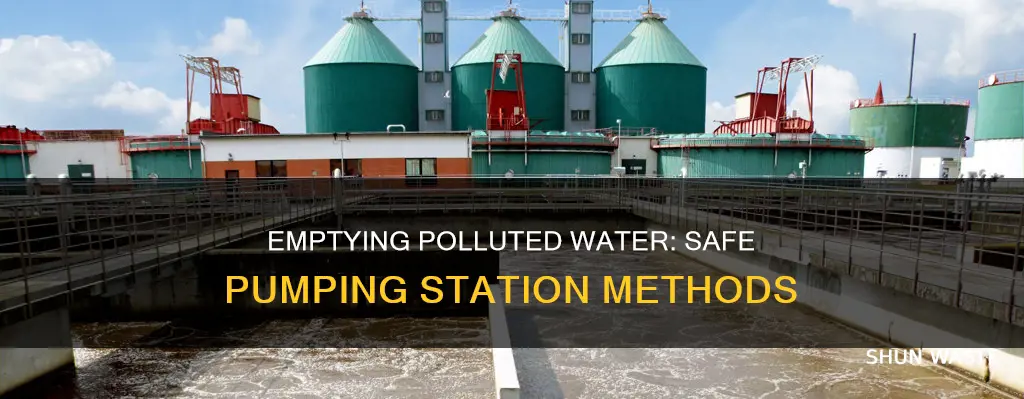
Pumping stations are an essential part of flood defences, removing water from flooded land and preventing the sewer system from overflowing during heavy rain. They are also used to maintain water levels in canals. When dealing with polluted water, it is crucial to use equipment that can handle challenging conditions without getting blocked. Self-cleaning filters can effectively prevent blockages in pumps and connected equipment. For example, the Rotorflush filter is specifically designed to handle dirty and contaminated water, with a self-cleaning mechanism that continuously cleans the filter mesh. In addition, polluted water can be purified using a water sieve and filtration medium, although this process may not remove all germs.
How to empty polluted water into a pumping station
Characteristics | Values |
---|---|
Type of pump | Self-cleaning filters and filter pumps |
Location of pump | Upstream from any sewage or water treatment plants |
Distance from water source | A new pump should be placed at a fresh water source |
Pipes | Should not run through or be too close to a landfill |
Water source | Should not be on polluted ground |
Pump maintenance | Regular maintenance can reduce environmental risks associated with overflowing and breakdowns |
Pump placement | In a closed system, there is a risk of out-pumping the water source |
Pump type | Submersible pumps are increasingly used as they require less space and are not impacted by weather |
What You'll Learn
Using self-cleaning filters to prevent blockages in pumps
When dealing with polluted water, it is crucial to employ equipment that can withstand such conditions without succumbing to blockages. Self-cleaning filters are an effective solution to prevent blockages in pumps, intake strainers, and other connected equipment. Here are some key points about using self-cleaning filters to prevent blockages in pumps:
Selecting the Right Self-Cleaning Filter
Choose a self-cleaning filter specifically designed for handling polluted water, such as the Rotorflush self-cleaning filters. These filters are equipped with a self-cleaning mechanism that continuously cleans the filter mesh, preventing debris from causing blockages.
Proper Installation
Ensure that the self-cleaning filter is properly installed on the intake of your pump or connected equipment. Securely attach it and position it correctly to maximize its effectiveness in filtering out pollutants and contaminants from the water.
Continuous Automatic Backwash
Self-cleaning filters utilize a continuous automatic backwash system. This means that while the pump is running, the filter continuously clears itself of any debris, weed, or other particulate matter. This prevents blockages and ensures an uninterrupted supply of filtered water.
Increased Efficiency and Reduced Maintenance
By preventing blockages, self-cleaning filters offer increased efficiency and reduced maintenance requirements. They protect pumps and other equipment from blockages, extending their lifespan and minimizing the need for frequent maintenance.
Applications
Self-cleaning filters are versatile and can be used in various industries, including wastewater treatment, irrigation, heat pump installations, and agriculture. They are suitable for pumping and filtering polluted water in difficult conditions, making them a reliable choice for maintaining water quality and system functionality.
Building Homes: Water Pollution's Unseen Culprit
You may want to see also
Locating and opening the waste cap
To locate and open the waste cap, start by identifying the waste cap on your boat. It is essential to differentiate it from the fuel or water caps, as these fluids should not be mixed. Once you are certain you have the correct cap, proceed to remove it. In most modern facilities, you won't need to apply significant downward pressure on the exit tube, and the risk of the tube popping out is minimal. These caps typically screw into the boat and are designed to be the correct size.
After locating and opening the waste cap, you can proceed with emptying your holding tank. If you are at a fuel dock with a waste pump-out, you can empty the Marine Sanitation Device (MSD) there. Alternatively, you can travel at least three miles offshore and empty your tank there.
If you are dealing with a gravity tank, the process is relatively straightforward. Simply open the valve and listen for any sounds that indicate the tank is emptying. For a macerator setup, you will need to open the macerator line's thru-hull fitting in the bilge or lazarette to allow fluids to exit the boat.
When the tank is almost empty, you will notice that the motor will freewheel and spin, similar to a nearly blended frozen drink. At this point, you can pump water through the toilet to flush out any remaining contents. Make sure to close the thru-hull valve when you are finished, as sailing along can cause backflow that can enter the toilet and overflow onto the head sole or shower.
Water Changes: Refreshing Your Aquarium, Removing Pollutants Effectively
You may want to see also
Using a macerator button to empty the tank
A macerator pump is a straightforward and affordable solution for creating a bathroom setup almost anywhere, without the need for conventional plumbing fixtures. It is particularly useful when installing a bathroom seems impractical or impossible. The macerator pump uses a macerator device, often positioned behind the toilet fixture, to break down solids and fluids into a fine slurry that can be discharged under pressure through small-diameter piping.
To empty a tank using a macerator button, you can follow these steps:
- Flush the toilet, allowing the effluent to be discharged by gravity through the rear spigot into the macerator device.
- As the water level rises, the water pressure will activate a microswitch, turning on the macerator device. The stainless steel blades will then rotate at high speed, grinding the effluent into tiny particles.
- Once the effluent is completely reduced, the microswitch will deactivate, ending the maceration process.
- The reduced effluent will then be pumped away from the macerating unit through a small pipe into a sanitary gravity drain or septic tank.
- Finally, remove the hose from the tank and secure the bung to prevent any spillage during transportation to the dump station.
It is important to note that while macerator systems can handle drainage from multiple fixtures, the toilet flush takes priority in the event of simultaneous discharging. Additionally, ensure that you have access to the pump and water valves for servicing, as recommended by manufacturers.
Water Pollution: Understanding the Many Types and Their Impact
You may want to see also
The importance of regular pumping station maintenance
Pumping stations are crucial in various contexts, from industrial plants to municipal sewer systems. They play a pivotal role in commercial, manufacturing, and wastewater management applications. Therefore, regular pumping station maintenance is essential to ensure efficient operation, minimise downtime, and maximise the lifespan of the infrastructure. Here are some key reasons why regular pumping station maintenance is vital:
Identify Potential Issues
Scheduled and routine inspections are a cornerstone of pumping station maintenance. They help identify potential issues before they escalate into major problems. Regular checks allow for the early detection of wear and tear, leaks, and other visible issues. This proactive approach can reduce the frequency of breakdowns and system failures, improving overall reliability and efficiency.
Extend Equipment Lifespan
Proper maintenance activities, including lubrication, cleaning, and calibration, ensure the long-term performance and reliability of pumping stations. Lubrication reduces friction and wear on moving parts, while cleaning prevents debris from interfering with the station's operation. Calibration of sensors and control systems ensures accurate readings and optimal performance. By addressing issues promptly and upgrading components, the lifespan of the equipment can be extended.
Cost Savings and Energy Efficiency
Regular maintenance can lead to significant cost savings by reducing the need for expensive repairs or replacements. It also helps to optimise energy consumption and operational costs. Predictive maintenance techniques, such as oil analysis, vibration monitoring, and thermographic inspections, can further enhance energy efficiency and reduce operational costs.
Ensure Water Quality and Safety
In the context of wastewater management, regular pumping station maintenance is crucial to ensure water quality and safety. Proper maintenance of sewer pumps, including grinder pumps and sewage pumps, prevents blockages and ensures efficient operation. This helps to maintain water quality and reduces the risk of water pollution, protecting public health and the environment.
Optimise Performance and Efficiency
Regular maintenance keeps pumping stations operating at peak efficiency. This involves periodic checks on performance, inspection of wearing parts, alignment checks, and lubrication of bearings and joints. By identifying issues early, troubleshooting becomes more effective, and pump system failures can be prevented. Optimised performance also contributes to cost savings and a more sustainable operation.
In conclusion, regular pumping station maintenance is essential to ensure the reliable and efficient operation of these critical systems. By identifying issues early, extending equipment lifespan, reducing costs, optimising performance, and ensuring water quality, pumping stations can effectively serve their intended purposes in various industrial, commercial, and municipal contexts.
Factories: Air and Water Polluters
You may want to see also
Using a water pump to treat and re-treat water
Pump and treat is a safe way to clean up contaminated groundwater and prevent it from spreading to other areas, such as drinking water supplies, wildlife habitats, and recreational water bodies. This method is typically used after the source of groundwater contamination, such as leaking drums or contaminated soil, has been addressed or removed.
The pump and treat process involves pumping contaminated groundwater to a surface collection system through wells in the saturated zone. The treatment system may consist of a single cleanup method, such as activated carbon or air stripping, or a combination of methods, to clean the water. The cleaned groundwater is then either discharged into sewer systems or re-injected into the subsurface.
To effectively pump and treat contaminated water, it is essential to select the right type of pump and ensure proper installation and maintenance. For example, self-cleaning filters and filter pumps, such as those offered by Rotorflush, can help prevent blockages in pumps and connected equipment when dealing with dirty and contaminated water. These filters are equipped with a self-cleaning mechanism that continuously cleans the filter mesh, preventing debris from accumulating and causing blockages.
Additionally, different types of pumps used in water treatment plants include centrifugal pumps, submersible pumps, positive displacement pumps, and metering pumps. Centrifugal pumps spin at high speeds to force wastewater out of the pump and into discharge pipes or areas within the facility. Submersible pumps are placed directly in the water or slurry to provide additional pumping power for fluid removal. Positive displacement pumps enclose and force out a specific amount of fluid into a discharge pipe, and metering pumps, such as peristaltic pumps, feed chemicals into the water stream for treatment.
By selecting the appropriate pump, ensuring proper installation, and maintaining the equipment, water treatment facilities can effectively treat and re-treat water to ensure its quality and protect the environment and public health.
Ions in Water: Understanding High Concentration Pollution
You may want to see also