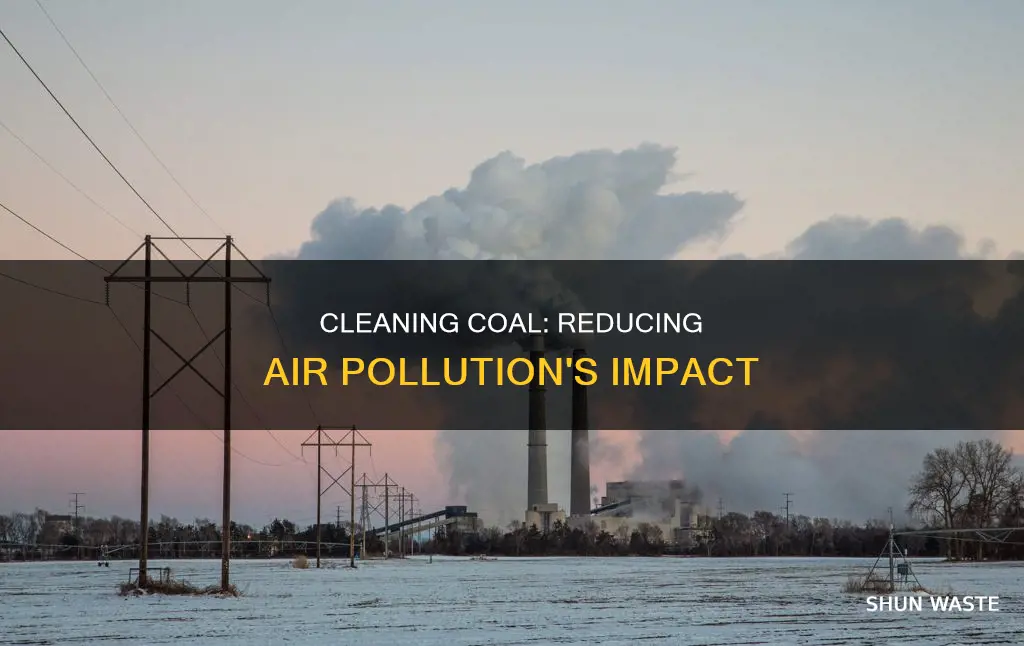
Burning coal for energy generation has long been a reliable source of energy for the US and other countries. However, it is also an incredibly dirty process, with harmful environmental and public health impacts. The pollutants produced by burning coal include small airborne particles, carbon monoxide, volatile organic compounds, arsenic, lead, nitrogen oxides, and particulate matter, which have been linked to asthma, cancer, heart and lung ailments, and neurological problems. To mitigate coal-based pollution, various approaches have been proposed, including physical and chemical cleaning of coal before combustion, carbon capture and storage technologies, and the use of modern technologies to reduce pollution in coal-fired power plants. While these methods have shown some success in reducing emissions, there are still challenges and criticisms associated with their effectiveness, cost, and environmental impact.
How to Clean Coal Air Pollution
Characteristics | Values |
---|---|
Clean Coal | Capturing carbon emissions from burning coal and storing them in underground pockets of porous rock |
Carbon Capture and Storage (CCS) | Captures around 90% of CO2 produced at power plants |
Gasification | Makes it easier to separate CO2 from exhaust fumes |
Oxy-combustion | Babcock-ThermoEnergy's Zero Emission Boiler System (ZEBS) features near 100% carbon capture and no air emissions |
Scrubbers | Remove sulfur dioxide from coal-generated gas |
Coal Washing | Removes soil and rock from coal before it is sent to a factory |
Nitrogen Oxide Controls | Reduce nitrogen oxide emissions, a contributor to smog and acid rain |
Mountaintop Removal | This technique changes the landscape and can harm aquatic wildlife downstream |
Coal Ash Storage | Can contaminate groundwater if not properly stored |
Coalbed Methane | Must be vented out of mines to make them safer, but can be captured and used or sold |
What You'll Learn
Cleaning coal before combustion
Coal is the dirtiest of all fossil fuels and has long been a reliable source of energy in the US. When burned, it produces emissions that contribute to global warming, create acid rain, and pollute water. The same chemistry that enables coal to produce energy also produces harmful environmental impacts and pollutants that harm public health.
Coal can be cleaned before combustion by physical and chemical means. Physical cleaning of coal usually involves gravimetric processes, often in conjunction with froth flotation. Such processes remove minerals and other non-combustible components of coal, exploiting their greater density compared to that of coal. This technology is widely practiced.
Coal can also be cleaned in part by chemical treatments. The concept is to use chemicals to remove the harmful components of coal, leaving the combustible material behind. Typically, coal cleaning entails treating crushed coal with acids or bases. This technology is expensive and has rarely moved beyond the demonstration phase. During World War II, German industry removed ash from coal by treating it with hydrofluoric acid and related reagents.
Another method of cleaning coal before combustion is gasification. With integrated gasification combined cycle (IGCC) systems, steam and hot pressurized air or oxygen combine with coal in a reaction that forces carbon molecules apart. The resulting syngas, a mixture of carbon monoxide and hydrogen, is then cleaned and burned in a gas turbine to make electricity. The heat energy from the gas turbine also powers a steam turbine.
Carbon capture and storage (CCS) technologies are emerging technologies that could allow coal plants to capture some of the CO2 they would otherwise release. The CO2 could then be transported and stored in a geological repository without harming the earth's climate. A few projects worldwide are currently operating, but the technology remains expensive, especially compared with cleaner forms of generation, and it is still unproven at the scale needed to materially contribute to addressing climate change.
Upholstered Furniture: Emitting Indoor Air Pollutants?
You may want to see also
Gasification of coal before burning
Gasification of coal is a process that transforms coal into synthetic natural gas (SNG) before it is burned. This synthetic gas can be used for power generation, heating, and chemical production. Gasification offers several advantages over traditional coal combustion, including a reduction in local air pollution and the capture of carbon dioxide (CO2) and other greenhouse gas emissions.
The process of gasifying coal involves placing coal into a high-temperature, pressurised container with steam and a limited amount of oxygen to produce a gas. This gas is known as synthesis gas or syngas and primarily consists of carbon monoxide and hydrogen. The gas is then cooled, removing undesirable components such as carbon dioxide and sulfur. This process is known as the water-shift reaction, where CO + H2O gives CO2 + H2. The resulting concentrated CO2 can then be captured, and the hydrogen can be used as fuel in a gas turbine for electricity generation.
One example of a coal-based plant using carbon-capture technology is the Schwarze Pumpe power station in Germany, built by Siemens and operational since 2008. The facility captures CO2 and acid rain-producing pollutants, separates them, and compresses the CO2 into a liquid. Another example is the $2.3 billion coal gasification plant in Indonesia, initiated by President Joko Widodo in 2022. The plant is designed to use 6 million tonnes of low-rank coal to produce 1.4 tonnes of dimethyl ether annually, reducing Indonesia's liquefied petroleum gas imports.
Overall, the gasification of coal before burning has the potential to reduce air pollution, capture carbon dioxide and other greenhouse gases, and improve the efficiency of coal-fired power plants.
Air Quality and Pollution: Understanding the Impact
You may want to see also
Carbon capture and storage
CCS is a three-step process: capturing, transporting, and storing CO2. During the capture phase, CO2 is captured from industrial processes such as steel and cement production or from burning fossil fuels in power generation. This can be done through various methods, such as oxy-combustion or post-combustion capture. The captured CO2 is then transported via ship or pipeline to a suitable storage location.
The final step of CCS involves storing the captured CO2 deep underground in geological formations, such as saline aquifers or depleted gas fields. These storage sites can be onshore or offshore and are rigorously monitored to ensure the safe containment of CO2. One example of a storage site is the proposed Zero Carbon Humber project in the UK, which aims to utilize a saline aquifer located about 1 mile below the seabed in the southern North Sea.
CCS technology plays a crucial role in reducing CO2 emissions from large industrial sources. According to the Global CCS Institute, the 22 operational or under-construction CCS projects worldwide are expected to capture 40 million tonnes of carbon dioxide annually when fully functional. However, it is important to note that capturing and compressing CO2 requires a significant amount of energy, increasing the fuel needs of coal-fired power plants.
Air Quality Alert: Is Indoor Air More Polluted?
You may want to see also
Scrubbers to clean smoke
Smokestack scrubbers are a new component of industrial exhaust systems that are used as air pollution control devices. They are designed to remove harmful particles, gases, and chemical byproducts from industrial exhaust streams. Scrubber systems use liquid or chemicals to remove these pollutants from industrial exhaust and flue gases.
There are two main types of scrubber systems: wet and dry. Wet scrubber systems use water or another liquid to collect harmful substances from the exhaust air. They work with both gaseous and solid material and can even handle corrosive materials. Wet scrubbers have been in use for over 160 years, with water being used as a natural binder for dust for over 2000 years. Dry scrubber systems, on the other hand, use specific chemicals to target, absorb, and dissolve hazardous materials in the exhaust.
Scrubbers are particularly effective at removing sulfur from smoke before it leaves the smokestack. They can also be used to remove ammonia and smoke. Some scrubber systems also contain a heat recovery coil that collects heat energy from the exhaust and transfers it back into the building's heating unit, saving energy and money.
It is important to note that scrubber systems must be properly maintained and cleaned to ensure they are working efficiently. Filters and material collection devices should be emptied or replaced regularly.
Benzyl Chloride: A Hazardous Air Pollutant?
You may want to see also
Reducing moisture content
Moisture content is an important parameter in coal analysis, as it determines the calorific (heating) value and handling properties of coal. Coal with high moisture content has a lower calorific value than low-moisture coal, as moisture absorbs heat, reducing the relative efficiency of heating when the coal is combusted.
There are several methods to reduce the moisture content of coal. One way is to use physical cleaning processes, such as gravimetric processes and froth flotation, which remove minerals and other non-combustible components of coal by exploiting their greater density compared to coal. Another method is to use chemical treatments, such as treating crushed coal with acids or bases, to remove deleterious components and leave behind combustible material. However, this method is expensive and rarely moves beyond the demonstration phase.
One example of a chemical treatment is the use of hydrofluoric acid, which was employed by the German industry during World War II to remove ash from coal. More recently, the U.S. Department of Energy conducted projects in the late 1980s and early 1990s, known as the Clean Coal Technology and Clean Coal Power Initiative, which aimed to reduce moisture content and emissions from coal combustion.
Another approach to reducing moisture content in coal is through drying processes. The vapor-solid double split moving bed dryer, for instance, achieves uniform drying of particles and higher drying efficiency compared to other dryers. Interface renewal drying is another method that can reduce moisture content by an additional 1.6%. This technique involves simulating the interface update of coal in a moving heating surface and analyzing the dynamic changes in temperature and moisture during the drying period.
By reducing the moisture content of coal, emissions can be significantly decreased. According to the U.S. Department of Energy, removing moisture from low-rank coals prior to combustion can reduce emissions by up to 50%.
Air Pollution: Unborn Health and Teratogen Risks
You may want to see also
Frequently asked questions
Clean coal refers to capturing carbon emissions from burning coal and storing them in underground pockets of porous rock.
Clean coal works by capturing and storing carbon emissions from burning coal. This is done through carbon capture and storage (CCS) technologies, which involve capturing and transporting the CO2 to be stored in a geological repository without harming the earth's climate.
Clean coal has been criticised for being expensive and failing to deliver on its environmental promises. For example, refined coal has led to increased NOx emissions and water pollution in some cases.
Alternatives to burning coal include wind and solar energy.