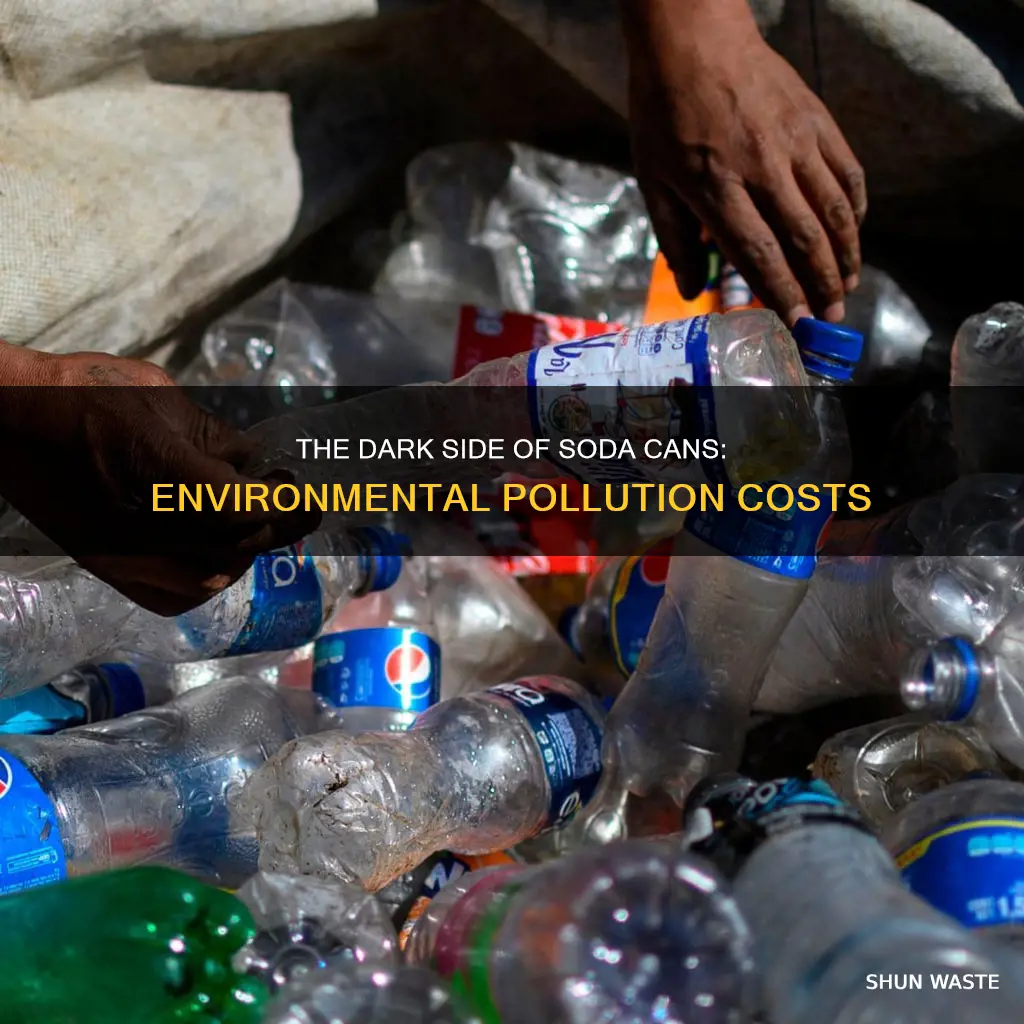
Aluminium cans are considered to be the most environmentally friendly packaging for pressurised drinks, but the production of soda cans still contributes to pollution. The water used in soda often comes from drought-prone areas, and soda factories have been closed over pollution issues, such as discharging toxic effluents into the environment. Beverage companies Coke, Nestle and PepsiCo are the three largest plastic polluters in the world. The ingredients in soda also contribute to its carbon footprint, with sugar being the primary ingredient.
Characteristics | Values |
---|---|
Carbon footprint | Ingredients contribute between 7% and 14% of soda’s carbon footprint, most of which comes from sugar |
Water usage | Water used in soda production can come from drought-prone areas, worsening water problems in poor regions |
Water pollution | Coca-Cola has been called out for water pollution and offloading contaminated waste onto local farmers for use as fertilizer |
Environmental impact | Aluminium cans contribute less to global warming than glass and plastic because they consume less energy and resources |
Microplastics | Microplastics are increasingly being found in beverages, including soda, raising health concerns |
What You'll Learn
- Aluminium cans are more environmentally friendly than glass and plastic because they consume less energy and resources to make
- Aluminium cans are lighter than glass and don't use fossil fuels like plastic does
- Glass and plastic require more electricity to make, which generates more sulphur dioxide pollution, a leading cause of acid rain
- Microplastics are increasingly being found in our food supply, especially in beverages
- Coca-Cola has been called out for water pollution and offloading contaminated waste onto local farmers for use as fertiliser
Aluminium cans are more environmentally friendly than glass and plastic because they consume less energy and resources to make
Aluminium cans are also more environmentally friendly than glass and plastic because they are more easily recycled. Aluminium can be recycled over and over again without losing quality, whereas glass and plastic can only be recycled a limited number of times before they need to be downcycled or thrown away. Recycling aluminium cans also uses less energy and water than recycling glass or plastic.
Another reason why aluminium cans are more environmentally friendly than glass and plastic is that they have a lower carbon footprint. The carbon footprint of a product is the amount of greenhouse gas emissions that are released into the atmosphere during its production, use, and disposal. Aluminium cans have a lower carbon footprint than glass and plastic because they are made from a material that is more easily recycled and has a longer lifespan.
Finally, aluminium cans are more environmentally friendly than glass and plastic because they are less likely to contribute to water pollution. Glass and plastic bottles can end up in landfills, where they can leach harmful chemicals into the groundwater. Aluminium cans, on the other hand, are more likely to be recycled and reused, reducing the amount of waste that ends up in landfills.
How Sewage Pollutes Groundwater: Understanding the Risks
You may want to see also
Aluminium cans are lighter than glass and don't use fossil fuels like plastic does
The processes involved in making aluminium cans also contribute less to environmental problems like acid rain and oxygen-free zones in the ocean. This is because creating glass and plastic requires more electricity, and so it generates more sulphur dioxide pollution on average – a leading cause of acid rain. Making glass and plastic, and extracting the materials to make them (particularly soda ash for glass production), also releases more phosphates into the environment, which can overload rivers and coastal seas and deplete oxygen from the water.
However, it is important to note that the water used in soda often comes from poverty-stricken, drought-prone areas, which can contribute to groundwater depletion and water pollution. In addition, certain soda factories have been closed over pollution issues when they discharged toxic effluents into the environment.
Minimizing Air Pollution: Simple Steps for a Cleaner Tomorrow
You may want to see also
Glass and plastic require more electricity to make, which generates more sulphur dioxide pollution, a leading cause of acid rain
Glass and plastic require more electricity to make than aluminium cans, which generates more sulphur dioxide pollution on average. Sulphur dioxide is a leading cause of acid rain. Making glass and plastic also releases more phosphates into the environment, which can overload rivers and coastal seas and deplete oxygen from the water. Aluminium cans are the most environmentally friendly packaging for pressurised drinks.
India's Air Pollution: Measurement Methods and Strategies
You may want to see also
Microplastics are increasingly being found in our food supply, especially in beverages
Aluminium cans are considered to be the most environmentally friendly packaging for pressurised drinks. They contribute less to global warming than glass and plastic because they are lighter and consume less energy and resources to make. However, the ingredients in soda, particularly sugar, contribute between 7% and 14% of soda's carbon footprint.
Strategies for Factories to Reduce Pollution and Improve Sustainability
You may want to see also
Coca-Cola has been called out for water pollution and offloading contaminated waste onto local farmers for use as fertiliser
Aluminium cans are considered to be the most environmentally friendly packaging for pressurised drinks. They contribute less to global warming than glass and plastic because they are lighter and not made from fossil fuels. However, the ingredients in soda contribute between 7% and 14% of its carbon footprint, with most of that coming from sugar.
Coca-Cola has been accused of dehydrating communities in its pursuit of water resources to feed its own plants, drying up farmers' wells and destroying local agriculture. In India, Coca-Cola has been called out for groundwater depletion, water pollution and offloading contaminated waste onto local farmers for use as fertiliser. The Central Pollution Control Board of India found in 2003 that sludge from Coca-Cola's Uttar Pradesh factory was contaminated with high levels of cadmium, lead and chromium. The company was offloading cadmium-laden waste sludge as "free fertiliser" to tribal farmers who live near the plant. The largest Coca-Cola plant in India has been accused of putting thousands of farmers out of work by draining the water that feeds their wells, and poisoning the land with waste sludge that the company claims is fertiliser. Coca-Cola has also violated workers' rights in countries such as Colombia, Turkey, Guatemala and Russia.
Car Gas Usage: Pollution Culprit or Green Energy?
You may want to see also
Frequently asked questions
Aluminium cans are the most environmentally friendly packaging for pressurised drinks, contributing less to global warming than glass and plastic. However, the ingredients in soda contribute between 7% and 14% of its carbon footprint, with sugar being the primary ingredient.
Aluminium cans are lighter than glass and aren't made from fossil fuels like plastic. They also contribute less to environmental problems like acid rain and oxygen-free zones in the ocean.
Beverage manufacturers have been criticised for depleting water supplies, particularly in drought-prone areas. Coca-Cola has been called out for water pollution and offloading contaminated waste onto local farmers in India.
Microplastics are increasingly being found in beverages, raising health concerns as they can release hazardous chemicals and act as carriers of pathogens.