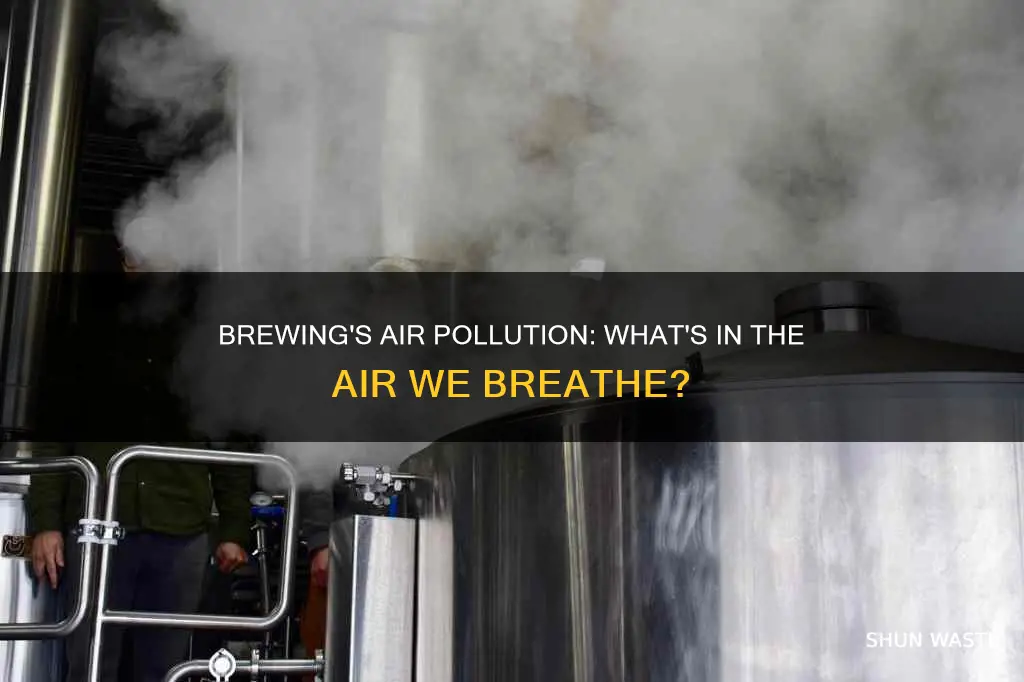
Beer brewing is a complex process that involves several steps and can generate various air pollutants. The most common air pollutants produced during the beer brewing process are volatile organic compounds (VOCs), particulate matter (PM), and carbon dioxide (CO2). VOCs are released when hot wort, the liquid extracted from the mashing process, is boiled. This step also releases PM, which can include dust, soot, and metals. While CO2 is a natural byproduct of fermentation, it is not considered an air pollutant. However, it contributes to the overall carbon footprint of the brewing process, along with energy consumption and wastewater. The presence of physical, chemical, and microbiological contaminants in beer can also impact the environment and human health, with sources ranging from raw materials to production processes and the factory environment.
Characteristics | Values |
---|---|
Common air pollutants | Volatile organic compounds (VOCs), particulate matter (PM), aerosol and bioaerosol pollutants, and carbon dioxide (CO2) |
Sources of air pollutants | Boiling hot wort, the liquid extracted from the mashing process |
Effects of air pollutants | Harmful to human health and the environment |
Raw materials | Water, malt, hops, barley, cereals, unmalted grains, sugar/corn syrups, yeast |
Metal pollution | Cr, Cu, and Zn |
Fungal contamination | Loss of malt yield, loss of quality, presence of toxic fungal secondary metabolites (MTs) |
Toxin reduction | Adsorption of spent grains during brewing converts toxins into less toxic compounds or reduces their concentration |
Water consumption | High water usage due to constant cleaning during the brewing process; water-to-beer ratio of 4.5:1 |
Energy consumption | Drying and roasting barley are the most energy-intensive parts of the process |
Wastewater | Large volumes of wastewater produced, impacting natural ecosystems |
Solid waste | Spent grains, hot trub, and yeast |
Emissions | CO2 emissions can be reduced by converting to LED or CFL lighting and using low NOx emissions burners |
What You'll Learn
- Volatile organic compounds (VOCs) are emitted during the boiling of hot wort
- Particulate matter (PM) is produced during the mashing and boiling processes
- Carbon dioxide (CO2) is a natural by-product of fermentation
- Metals in beer come from raw materials and brewing equipment
- Fungi contaminating grain and malt lead to a high economic burden
Volatile organic compounds (VOCs) are emitted during the boiling of hot wort
The production of beer involves a complex, multi-step process that begins with the preparation of raw materials, including malted barley, wheat, corn, wheat malt, rice, millet, and hops. The grains are milled and then combined with water in a saccharification kettle to create mash. During the boiling of this wort, VOCs are released, contributing to air pollution.
To mitigate the environmental impact of these emissions, breweries can implement a range of measures. For example, the installation of low NOx emissions burners in boilers can effectively reduce air pollution levels. Additionally, by reusing spent grains as animal feed, breweries can reduce waste while also generating additional income for local farms.
Another significant source of pollution in the beer brewing process is the contamination of raw materials, such as barley and malt, by fungi. This contamination results in a substantial economic burden due to the loss of yield, reduced quality, and the presence of toxic fungal secondary metabolites (MTs). To address this issue, it is crucial to comply with national and international regulations regarding the maximum allowable levels of toxins in raw materials.
Furthermore, the beer brewing process consumes significant amounts of water and energy, leading to environmental challenges. To reduce their environmental footprint, breweries can focus on water conservation through clean-in-place measures and adopt more efficient energy practices, such as heat exchange for cooling wort and the use of renewable energy sources.
Oil's Dark Secret: Air Pollution's Main Culprit?
You may want to see also
Particulate matter (PM) is produced during the mashing and boiling processes
The beer brewing process involves several steps and can generate various air pollutants. One of the key pollutants produced during this process is particulate matter (PM). PM is released during the mashing and boiling stages, specifically when the hot wort, the liquid extracted from mashing, is boiled. This release of PM contributes to air pollution and poses potential health risks.
Particulate matter (PM) is a complex mixture of solid and liquid particles suspended in the air. In the context of beer brewing, PM is generated when the wort is boiled. The boiling process is crucial for developing the flavour and aroma of the beer, but it also results in the release of PM into the air. The composition of PM can vary, but it typically includes a range of particles such as dust, soot, and metals. The presence of metals in beer primarily originates from the raw materials used, such as water, malt, and hops, which can be contaminated by metal-containing agrochemicals or ecosystem pollution.
During the mashing process, grains are milled and mixed with water in a saccharification kettle to create the wort. This wort is then boiled, and it is during this boiling stage that PM is released into the air. The boiling temperature and duration can vary depending on the specific beer recipe and the desired level of flavour development. However, it is important to note that the boiling process not only releases PM but also emits volatile organic compounds (VOCs), which contribute to both indoor and outdoor air pollution.
To mitigate the release of PM during the mashing and boiling processes, several measures can be implemented. Firstly, ensuring proper ventilation and air filtration systems in the brewing facility can help capture and remove PM before it escapes into the surrounding environment. Additionally, regular maintenance and cleaning of brewing equipment, including the kettle and boiling tanks, can reduce the buildup of particulate matter. Optimising the boiling process by minimising the duration and frequency of boiling can also help reduce PM emissions.
Furthermore, it is important to address the issue of metal contamination in the raw materials. Implementing measures to reduce metal pollution in agricultural practices, such as regulating the use of metal-containing agrochemicals, can decrease the presence of metals in the raw materials used for brewing. By minimising the metal content in the raw materials, the concentration of metals released into the air during the boiling process can be significantly reduced, contributing to improved air quality and reduced health risks for both workers and the surrounding community.
Air Pollution: Strategies for a Cleaner Tomorrow
You may want to see also
Carbon dioxide (CO2) is a natural by-product of fermentation
Carbon dioxide (CO2) is a natural by-product of the beer brewing process. It is produced during fermentation, when yeast consumes sugars and amino acids from the wort. This process occurs under anaerobic conditions, where sugars are primarily transformed into ethanol and carbon dioxide. The carbon dioxide gives beer its carbonation.
While CO2 is a natural and expected outcome of fermentation, it is important to consider its potential impact on the environment. CO2 is a greenhouse gas and contributes to the carbon footprint of the brewing industry. High levels of CO2 can also be a safety concern for brewery workers, as it can displace oxygen and create an asphyxiating environment. Therefore, proper ventilation and safety protocols are crucial during the brewing process.
The amount of CO2 produced can vary depending on the type of beer being brewed. For example, cask-conditioned beers tend to have lower CO2 levels than bottle-conditioned beers. Additionally, the fermentation time and temperature play a significant role in determining the final CO2 content of the beer.
Breweries have implemented strategies to reduce their carbon emissions and overall environmental impact. These include adopting renewable energy sources, improving energy efficiency, and investing in wastewater treatment. By addressing these environmental challenges, the brewing industry can work towards a more sustainable future.
Furthermore, it is worth noting that the presence of CO2 in beer is not considered a contaminant or pollutant. The fermentation process effectively converts potential toxins into less harmful compounds, ensuring that the final beer product meets health and safety standards. This natural transformation of CO2 during fermentation is a key aspect of the brewing process and contributes to the overall quality and characteristics of the beer.
Water vs Air: Pollution's Deadliest Forms
You may want to see also
Metals in beer come from raw materials and brewing equipment
The beer brewing process produces several air pollutants, including volatile organic compounds (VOCs), particulate matter (PM), aerosol and bioaerosol pollutants, and carbon dioxide (CO2). While CO2 is a natural by-product of fermentation, it can contribute to air pollution when released in large quantities during the brewing process.
Now, let's focus on the topic of metals in beer and their sources during the brewing process:
Metals in Raw Materials
Metals in beer primarily originate from the raw materials used in brewing, including water, hops, malt, barley, and yeast. These raw materials can be contaminated with metals through the use of metal-containing agricultural agrochemicals, such as fertilisers and pesticides, or through ecosystem pollution. For example, the application of copper-containing pesticides on hops can result in copper residues in the raw material. While the concentration of heavy metals in these raw materials is typically low, even negligible amounts can end up in the final beer product.
Metals in Brewing Equipment
Brewing equipment, such as tanks, pipes, containers, and filters, can also introduce metals into the beer. The choice of metal for brewing equipment is crucial and has an impact on both the flavour and safety of the beer. Copper, for instance, was historically used for its excellent thermal conductivity, but it can react with the beer, potentially imparting an unpleasant metallic taste. Stainless steel is now the preferred material for brewing equipment due to its good corrosion resistance and ability to prevent abnormal smells from corrosive by-products. Additionally, the use of aluminium for brewing tanks is acceptable for short-term contact with beer, but long-term exposure to other metals, including copper, will result in corrosion.
To summarise, metals in beer can originate from both the raw materials and the brewing equipment used in the brewing process. While most toxic metals are transferred to residues during brewing, some can end up in the final beer product, emphasising the importance of using appropriate materials and maintaining equipment to ensure safe and high-quality beer.
Air Pollution: Detecting the Invisible Danger in Your Home
You may want to see also
Fungi contaminating grain and malt lead to a high economic burden
Fungi contaminating grain and malt can lead to a high economic burden in the beer brewing process. Fungi invasion causes a loss of germination, colour, flavour, and degradation of nutritive value. Fungi contamination can also lead to grain charring due to hot spot generation and the production of toxigenic secondary metabolites, which have several health repercussions. The occurrence of toxigenic fungi and relative mycotoxins in grain is one of the most important social and economic concerns in cereal-producing countries, including many EU countries.
Fungal contamination of barley and malt results in a high economic burden from malt yield loss, quality failure, and costs connected to the presence of toxic fungal secondary metabolites (MTs). The pollution of barley and malt by fungi leads to a high economic burden due to the loss of malt yield, the loss of quality, and the costs associated with the presence of toxic fungal secondary metabolites (i.e., MTs). The levels of AFs and OTAs in beer are under indirect control, as their levels in beer are a function of their presence in malt, for which a maximum level has been set.
Fungal contamination of grain and malt can occur during the storage of raw materials. The critical factors affecting microbial growth in stored grains include the temperature and water content of the grain, the initial contamination level, the type of storage structure, the physical state of the grains, and the presence of other pests. Fungi can also contaminate grain and malt during the malting and brewing processes, as mycotoxins and their metabolites can enter the malt-beer chain.
To prevent fungal growth and reduce the economic burden of fungi contamination, several chemical and molecular biology-based analytical tools and strategies have been developed. These include drying and aeration, hermetic storage, dielectric heating, cold plasma treatment, ozonation, irradiation, ultra-superheated steam treatment, and the application of vegetable oil and plant derivatives. Additionally, the reuse of spent grains as animal feed can reduce waste and increase profits for local farms.
Overall, fungi contaminating grain and malt can lead to a high economic burden in the beer brewing process due to yield loss, quality failure, and the costs associated with the presence of toxic fungal secondary metabolites. By implementing prevention and control measures, the economic impact of fungi contamination can be mitigated.
Air Pollution: Warning Signs in Our Environment
You may want to see also
Frequently asked questions
The most common air pollutants produced during the beer brewing process are volatile organic compounds (VOCs), particulate matter (PM), aerosol and bioaerosol pollutants, and carbon dioxide (CO2).
VOCs are emitted during the brewing process when hot wort, the liquid extracted from the mashing process, is boiled. VOCs can be harmful to both human health and the environment.
PM is produced during the mashing and brewing process when hot wort is boiled. It can be made up of a variety of particles, including dust, soot, and metals.
CO2 is a natural by-product of fermentation and is what gives beer its carbonation. While it is not considered an air pollutant, high levels of CO2 can cause foaming in beer.