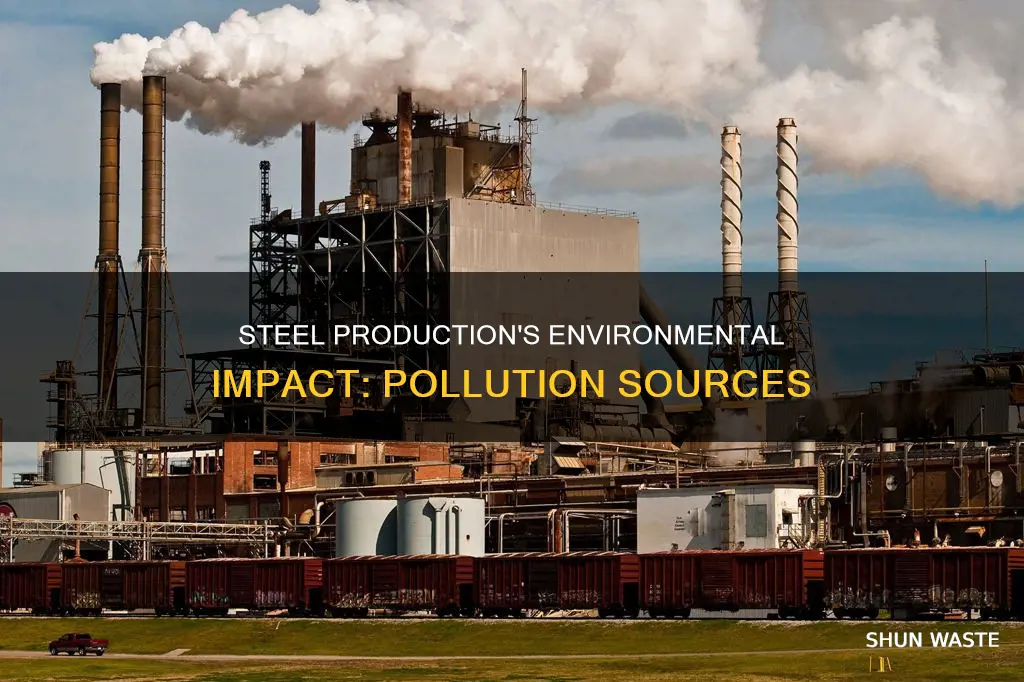
Steel is one of the most widely used metals in the world, contributing to economies and societies with its versatility, strength, and ease of conversion. However, the production of steel has a significant environmental impact, causing pollution through air emissions, water contamination, hazardous waste, and solid waste. The major sources of pollution in steel production are coking and iron-making, with the former releasing pollutants such as coke oven gas, naphthalene, ammonium compounds, and sulfur into the air and water. Iron and steel manufacturing also involve the processing of raw materials containing heavy metals, leading to dust emissions. The industry's heavy reliance on fossil fuels, particularly coal, further contributes to air pollution. As steel consumption and production continue to grow, addressing these environmental challenges becomes increasingly crucial to mitigate adverse health effects and improve the quality of life for communities located near steel plants.
Characteristics | Values |
---|---|
Air emissions | CO, SOx, NOx, PM2, coke oven gas, naphthalene, ammonium compounds, crude light oil, sulfur, coke dust |
Water emissions | Water used to cool coke after baking becomes contaminated with coke breezes and other compounds |
Greenhouse gas emissions | CO2 |
Solid waste | Slag, the limestone and iron ore impurities collected at the top of the molten iron |
Hazardous waste | Hazardous wastes are generated during steel production |
Energy consumption | Steel production is one of the most energy-intensive industries |
Fossil fuel dependence | Steel production heavily depends on fossil fuels, especially coal |
What You'll Learn
Coke production releases harmful gases and compounds
Coke is a crucial component in steelmaking, but the process of its production releases harmful gases and compounds, causing significant pollution. Coke is a carbon-rich, hard, porous substance derived from coal through a process called coking or carbonization. This process involves heating coal in ovens with limited oxygen, causing the coal to melt and release volatile matter such as oil, tar, hydrogen, nitrogen, and sulfur. The cooked coal then solidifies into coke.
The coking process generates harmful emissions, including coke oven gas, naphthalene, ammonium compounds, crude light oil, sulfur, and coke dust. These emissions contribute to air pollution and pose risks to human health. Inhalation, skin contact, or eye contact with these emissions can be hazardous, and organizations like the Occupational Safety and Health Administration (OSHA) in the United States have established exposure limits to protect workers.
Additionally, water used to cool the coke after baking becomes contaminated with coke breezes and other compounds, leading to water pollution. While the contaminated water can be reused, and most pollutants can be removed through filtration, it still contributes to environmental pollution.
The use of coal in coke production also has environmental implications. Coal is crushed, ground into a powder, and heated in ovens, releasing volatile compounds. The coal industry has faced scrutiny due to its environmental impact, and while there have been efforts to reduce coal consumption and emissions, it remains essential to steel production.
Moreover, the blast furnace, a crucial step in steelmaking, utilizes coke, iron ore, and limestone to produce pig iron. The blast furnace process further contributes to emissions, and while natural gas is increasingly used as a substitute for coke to reduce carbon emissions, the steel industry's reliance on coke production continues to have environmental consequences.
Overpopulation's Impact: Air Pollution Explained
You may want to see also
Energy consumption leads to carbon dioxide emissions
Steel production has a significant impact on the environment, with energy consumption being a major contributor to carbon dioxide emissions. The iron and steel industry is the largest coal consumer and is responsible for about 7% of global energy consumption. This high energy consumption leads to significant carbon dioxide emissions, with the industry emitting 2.6 Gt of CO2 annually, accounting for 6.5% of global emissions from energy use and 7-9% of global anthropogenic CO2 emissions.
The predominant production method in Europe, the BF/BOF process, relies heavily on coal, highlighting the need for alternative technologies to reduce emissions. Strategies being explored include BF/BOF efficiency programs that aim to decrease coal usage, increase fuel injection with alternatives like natural gas or biomass, or use coke oven gas as an energy source. While these measures can reduce emissions, they do not offer completely carbon-neutral steel production.
Another approach is using hydrogen-based DRI and EAF methods, which replace fossil fuels with hydrogen produced from renewable energy, enabling nearly emission-free steel production. Major European steel producers are actively exploring hydrogen-based processes, either as a PCI replacement or for direct reduction. Additionally, the use of "green hydrogen," produced through the electrolysis of water, can be employed as an alternative injection material to PCI, reducing carbon emissions by up to 20%.
Biomass, such as heated and dried sugar, energy cane, or pyrolyzed eucalyptus, can also be used as a reductant or fuel. However, its effectiveness is regionally dependent, as regions like Europe may not have sufficient biomass supply to significantly reduce carbon emissions. Carbon capture and storage technologies are also being explored, but they are not yet proven economically or technologically.
Transportation Pollution: Cars vs Planes
You may want to see also
Air pollution causes adverse health effects
Steel production releases a wide range of pollutants into the air, including fine particulate matter, volatile organic compounds, nitrogen oxides, and sulphur dioxide. These emissions have detrimental effects on both human health and the environment, causing air pollution and contributing to climate change. The areas closest to steel plants are the most affected by the pollution generated during steel manufacturing, and the adverse health effects of air pollution are well-documented.
According to the United States Environmental Protection Agency (EPA), exposure to air pollutants can lead to a variety of respiratory issues, including inflammation of the lining of the lungs, reduced lung function, respiratory symptoms, and increased susceptibility to respiratory infections. Prolonged exposure to air pollution can also result in premature mortality, aggravation of cardiovascular disease, and exacerbation of allergic symptoms. Additionally, air pollution has been linked to neurodevelopmental effects, such as lowered IQ and behavioural problems, further highlighting the importance of mitigating air pollutant emissions.
The health risks associated with fine particle pollution (PM2.5) from steel production have been studied in communities near steel manufacturing plants, such as Piquiá de Baixo in Brazil. Research has found a significant rate of lung function abnormalities and respiratory illnesses in these areas, underscoring the urgent need for action to protect residents from the harmful effects of air pollution. Lowering or eliminating criteria air pollutants can help reduce health risks and improve the quality of life for those living near steel plants.
Furthermore, the use of carbon-rich fuels, such as coke, in steel production results in the release of naphthalene, a potentially carcinogenic substance. Steel manufacturing also generates heavy metals like lead and cadmium, which are known to cause long-term health issues. The implementation of advanced emission control technologies and air quality monitoring systems is crucial to reducing the environmental and health impacts of the steel industry, ensuring a safer future for both workers and nearby communities.
Furnace Function: Unseen Environmental Pollutants and Their Causes
You may want to see also
Heavy metals and dust emissions are produced during processing
Steel production has a number of impacts on the environment, including air and water emissions, wastewater contaminants, hazardous wastes, and solid wastes. The major sources of pollution from steel production are iron-making and coking. Coke production is one of the major sources of pollution from steel production. Air emissions such as coke oven gas, naphthalene, ammonium compounds, crude light oil, sulfur, and coke dust are released from coke ovens. The water used to cool the coke after it has finished baking becomes contaminated with coke breezes and other compounds. While the volume of contaminated water can be large, it is reusable, and most pollutants can be removed by filtration.
Gaseous emissions and metal dust are the most prominent sources of waste from electric arc furnaces, which are used to produce steel from recycled scrap steel or direct reduced iron. These furnaces operate at temperatures of up to 1650 °C and can emit heavy metals and dust particles, which can be harmful to human health and the environment.
Studies have shown that areas around steel mills have higher levels of potentially toxic elements (PTEs) such as Cr, Mo, Ni, and W in street dust. These elements can be carried by spherical and melted irregular particles, which can travel up to 20 km from the source and affect both urban and rural areas. The presence of these PTEs in street dust can pose a risk to human health, as they can be a pathway for these toxic elements to enter the body.
To mitigate the impact of steel production on the environment and human health, it is important to reduce dust emissions and capture and store carbon emissions. While carbon capture and storage technology is not yet fully developed or economically viable, it has the potential to create new products and reduce emissions in the future.
Sunsets and Pollution: A Complex Relationship
You may want to see also
Fossil fuel dependence results in air pollution
Steel production has a significant impact on the environment, and this impact is closely tied to the industry's dependence on fossil fuels. This dependence on fossil fuels, such as coal, oil, and natural gas, results in air pollution, which is a major concern for both the environment and human health.
The burning of fossil fuels emits hazardous air pollutants, including sulfur dioxide, nitrogen oxides, particulate matter, carbon monoxide, and mercury. These pollutants have detrimental effects on the environment and human health. For example, air pollution from fossil fuels can cause acid rain, eutrophication, and damage to crops and forests. It is also linked to various health issues, including asthma, cancer, and heart disease.
The impact of fossil fuel combustion is especially harmful to children's health. The developing fetus and young children are more vulnerable to the adverse effects of toxic air pollutants due to their rapid growth and immature immune and detoxification systems. Fossil fuel combustion by-products are considered the most significant threat to children's health and future, contributing to global inequality and environmental injustice.
Furthermore, the extraction, transportation, and refining of fossil fuels can lead to oil spills, which have devastating consequences for communities, wildlife, and natural habitats. The BP Deepwater Horizon oil spill in the Gulf of Mexico in 2010 is a notable example, resulting in fatalities, widespread environmental damage, and significant economic costs.
The environmental and health impacts of fossil fuel dependence in steel production disproportionately affect communities of color and low-income communities. For instance, in "Cancer Alley," an area in Louisiana predominantly comprising Black and low-income residents, the cancer risk is nearly 50 times higher than the national average due to the proximity of numerous chemical plants and oil refineries.
Transitioning from fossil fuels to renewable energy sources offers immediate health benefits by preventing premature deaths attributed to fossil fuel pollution. Research from Harvard University and other institutions found that more than 8 million people died in 2018 from fossil fuel pollution, making it responsible for about 1 in 5 deaths worldwide. This highlights the urgent need to reduce dependence on fossil fuels and mitigate their harmful air pollution effects.
Taylor Swift's Environmental Impact: Pollution and the Pop Star
You may want to see also
Frequently asked questions
Steel production causes air emissions (CO, SOx, NOx, PM2), wastewater contaminants, hazardous wastes, and solid wastes.
Coke production is one of the major sources of pollution in steel production. Air emissions such as coke oven gas, naphthalene, ammonium compounds, and crude light oil are released from coke ovens. Water emissions come from the water used to cool coke after it has finished baking.
The steel industry impacts the environment through the extraction of iron ore, processing, conversion, treatment, manufacture, and transport. These stages consume energy, generate emissions, and create waste.
According to the U.S. Environmental Protection Agency (EPA), exposure to criteria air pollutants can cause respiratory health issues, including inflammation of the lungs, reduced lung function, increased susceptibility to respiratory infections, and aggravation of cardiovascular disease.
The main sources of emissions in the steel industry are onsite emissions related to the steel-making process and fuel combustion in steel plants (direct emissions), and offsite emissions associated with electricity use (indirect emissions).