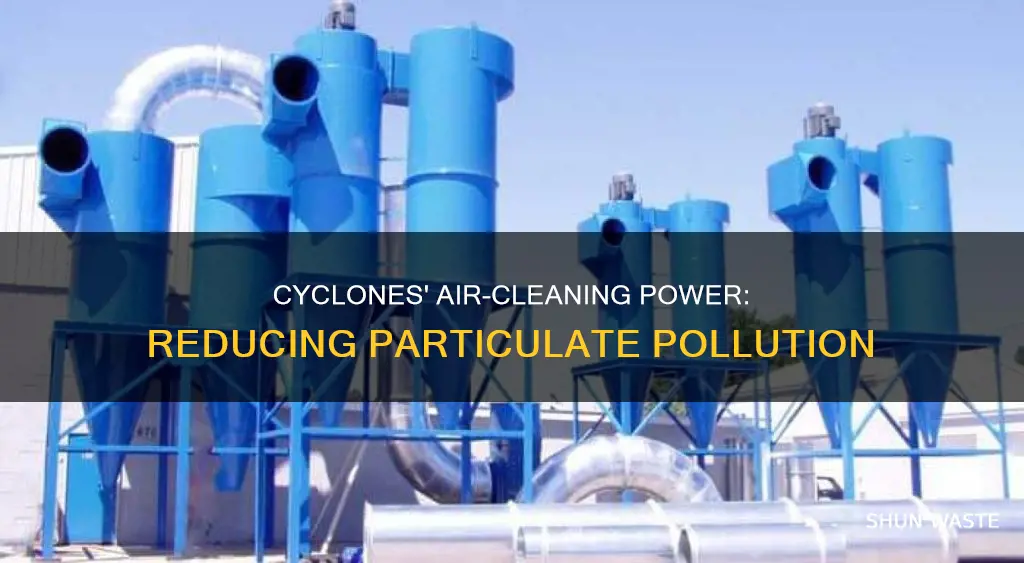
Cyclones are devices that use centrifugal and inertial forces to separate and remove particulate matter from air, gas, or liquid streams. They are commonly used to address air pollution, particularly in industrial settings, and are known as pre-cleaners due to their ability to remove larger particles, preventing subsequent finer filtration methods from dealing with these abrasive particles. Cyclones create a spiral vortex within a cylindrical or conical chamber, causing larger particles with higher inertia to strike the outside wall and fall to the bottom of the chamber, where they can be collected and removed. This process effectively reduces particulate pollution by separating and collecting coarse particles, allowing the cleaned air to exit through the top of the chamber.
Characteristics | Values |
---|---|
Mechanism | Centrifugal and inertial forces are used to separate particulate from the contaminated gas stream |
Particle Size | Generally used to collect particles greater than 10 micrometers in diameter; high-efficiency cyclones can collect particles as small as 2.5 micrometers |
Efficiency | Can remove 50-99% of all particulate matter in flue gas |
Energy Costs | High-efficiency cyclones require a higher pressure drop and higher energy costs |
Construction | Relatively simple construction with generally no moving parts |
Components | Inlet cylindrical section, conical section, outlet gas duct, outlet dust tube, and collection hopper |
Performance Indicators | Outlet opacity, inlet velocity, pressure differential, and inlet gas temperature |
Applications | Used in power and industrial applications, including pulp and paper plants, cement plants, oil refineries, and household vacuum cleaners |
What You'll Learn
Centrifugal and inertial forces
Cyclones use centrifugal and inertial forces to separate particulate matter from contaminated gas streams. Centrifugal force is a pseudo force that appears to act on objects when viewed in a rotating frame of reference. In the context of cyclones, it is the force that pushes large particles towards the cyclone walls, causing them to fall down into a hopper due to gravity. The cyclone's geometry, along with the volumetric flow rate, determines the cut point, or the size of particle that will be removed with a 50% efficiency.
Inertial forces, on the other hand, are responsible for separating particles of different sizes within the cyclone. The cyclone creates a spiral vortex, similar to a tornado, which causes the gas stream to move in a helical pattern. Lighter components with less inertia are more easily influenced by this vortex and travel up, while larger components with more inertia are not as easily influenced and tend to follow a straight path. This causes the larger particles to hit the inside walls of the container and fall into the hopper, while the cleaned gas escapes through the top.
The combination of centrifugal and inertial forces within the cyclone allows for the separation of particulate matter from contaminated gas streams, making cyclones an effective method for reducing particulate pollution. Cyclones are often used as pre-cleaners to remove larger, abrasive particles, and their simple construction and lack of moving parts make them a cost-effective solution for particulate pollution control.
Local Air, Local Action: Reducing Pollution Together
You may want to see also
Cyclone separator design
Cyclone separators are air pollution control devices that use the principle of inertia to remove particulate matter from flue gases. They are also known as pre-cleaners as they generally remove larger pieces of particulate matter, preventing finer filtration methods from dealing with large, abrasive particles later on. Cyclones are effective because they are not expensive to install or maintain, they have no moving parts, they collect dry particulate matter, and they take up very little space.
The design of a cyclone separator depends on its application. Cyclones are used in a variety of industries, including wood, chemicals, and agriculture. The standard dimensions of cyclones are directly related to their geometry, with efficiency increasing with smaller dimensions. The design process involves multiple steps, including calculating K ratios, geometrical dimensions, inlet and outlet velocities, friction coefficients, characteristic velocities, the cut-off diameter, efficiencies, and the pressure drop.
The geometry of a cyclone separator is critical to its performance. Cyclones are generally cylindrical or conical containers that create a spiral vortex to separate particles from air, gas, or liquid streams. The rotational effects and gravity separate mixtures of solids and fluids. The size of the cyclone depends on the volume of flue gas that needs to be filtered.
The performance of a cyclone separator is determined by its ability to separate particles of different sizes. Cyclones are typically designed to capture particles larger than 10 micrometers in diameter with 50% efficiency. However, high-efficiency cyclones can be employed to collect smaller particles, requiring higher pressure drops and energy costs. The separation efficiency of a cyclone is influenced by the particle size distribution of the contaminated gas stream.
In summary, the design of a cyclone separator involves multiple factors, including the geometry, dimensions, and performance characteristics. The specific design process may vary depending on the application, but the overall goal is to create an effective and efficient particle separation system.
Students' Role in Reducing Plastic Pollution
You may want to see also
Cyclone performance
The primary indicators of cyclone performance are the outlet opacity and inlet velocity. Other indicators include the pressure differential across the cyclone and the inlet gas temperature. Cyclones are generally used to collect particles greater than 10 micrometres in diameter, but high-efficiency cyclones can be used to collect smaller particles, down to 2.5 micrometres. The ability of a cyclone to separate particles is dependent on the rotational radius of the stream, which is determined by the cyclone's geometry and volumetric flow rate. This is known as the cut point of the cyclone and defines the size of the particle that will be removed from the stream with a 50% efficiency.
The performance of a cyclone can be improved by increasing the collection effectiveness or decreasing energy consumption. For example, reducing the inlet velocity can lower the pressure drop and, consequently, the energy required, resulting in a reduction in both financial and environmental costs. Additionally, the use of multiple-cyclone separators, which consist of several small-diameter cyclones operating in parallel, can enhance performance by increasing the length and reducing the diameter of the cyclones, leading to better separation of dust particulates.
The choice of cyclone for a specific application involves a trade-off between collection efficiency and pressure drop. Accurate data gathering from the design stage is crucial for the smooth operation of a cyclone. Cyclones are commonly used in industrial applications, such as in pulp and paper plants, steel mills, and petroleum coke plants, as well as in household devices like vacuum cleaners and kitchen ventilation systems.
Catalytic Converters: Reducing Pollution, Saving the Planet
You may want to see also
Cyclone sizing
Cyclones are sized to provide the maximum inlet velocity possible for high separation without excessive turbulence. Cyclones can vary drastically in size, depending on the volume of flue gas that needs to be filtered. The size of the cyclone directly impacts its ability to separate particles from the air stream.
The cyclone geometry, together with the volumetric flow rate, defines the cut point of the cyclone. This is the size of the particle that will be removed from the stream with a 50% efficiency. Particles larger than the cut point will be removed with a greater efficiency, and smaller particles with a lower efficiency. In a conical system, as the rotating flow moves towards the narrow end of the cyclone, the rotational radius of the stream is reduced, thus allowing for the separation of smaller particles.
The performance of a cyclone is indicated by the outlet opacity and inlet velocity. Other indicators include the pressure differential across the cyclone and the inlet gas temperature. Cyclones are generally used to collect particles greater than 10 micrometres in diameter. However, high-efficiency cyclones can be used to collect particles as small as 2.5 micrometres, but this requires a higher pressure drop and increased energy costs.
Hydroelectric Power: Pollution Solution or Problem?
You may want to see also
Cyclone applications
Cyclones are used in a variety of applications to reduce particulate pollution. They are commonly used as pre-cleaners to remove larger particles from contaminated gas streams, which can reduce the inlet loading of particulate matter for downstream collection devices. Cyclones use centrifugal and inertial forces to separate particulates from gases, with the particulate collection efficiency depending on the particle size distribution of the gas stream. They are particularly effective for particles greater than 10 micrometers in diameter.
One of the primary applications of cyclones is in the industrial sector. They are used in power and industrial facilities, including pulp and paper plants, cement plants, steel mills, petroleum coke plants, metallurgical plants, and sawmills. In these settings, cyclones help remove particulate matter from the air, improving air quality and reducing pollution.
In sawmills, for example, large-scale cyclones are employed to remove sawdust from extracted air, ensuring a cleaner environment for workers and reducing the risk of respiratory issues. Similarly, in the cement industry, cyclones are used as components of kiln preheaters, helping to separate and collect dust particles.
Cyclones are also used in oil refineries to separate oils and gases. This application is crucial for ensuring the purity of the end products and preventing contamination. Additionally, cyclones find utility in industrial and professional kitchen ventilation systems, where they effectively separate grease from the exhaust air in extraction hoods, reducing the risk of fire and improving indoor air quality.
Another important application of cyclones is in household settings, where they are increasingly used as the core technology in bagless vacuum cleaners. These cyclones help separate and collect dust, dirt, and debris, improving the cleaning efficiency of the vacuum cleaners. Some portable and central vacuum cleaners now utilize this technology.
Furthermore, cyclones have applications in scientific research. Smaller cyclones are used to separate airborne particles for analysis, with some small enough to be worn clipped to clothing. These devices help collect respirable particles, providing valuable data for research and monitoring air quality.
Beacons: Friend or Foe in the War on Pollution?
You may want to see also
Frequently asked questions
Cyclones use centrifugal and inertial forces to separate particulate from the contaminated gas stream as it spirals through the cyclone.
The particulate collection efficiency of a cyclone is directly related to the particle size distribution of the contaminated gas stream. Cyclones are typically used to collect particles greater than 10 micrometers in diameter.
Cyclones are relatively inexpensive, have no moving parts, are easy to maintain, and can be used as a pre-treatment before the gas stream reaches more effective pollution control devices.
Cyclones are not able to effectively collect particulate matter smaller than 10 micrometers in diameter and cannot handle sticky or tacky materials.
Cyclones are used in a variety of industrial applications, including in cement plants, oil refineries, and kitchen ventilation systems to separate grease from exhaust air. Small cyclone devices are also often installed to control pollution from mobile sources.