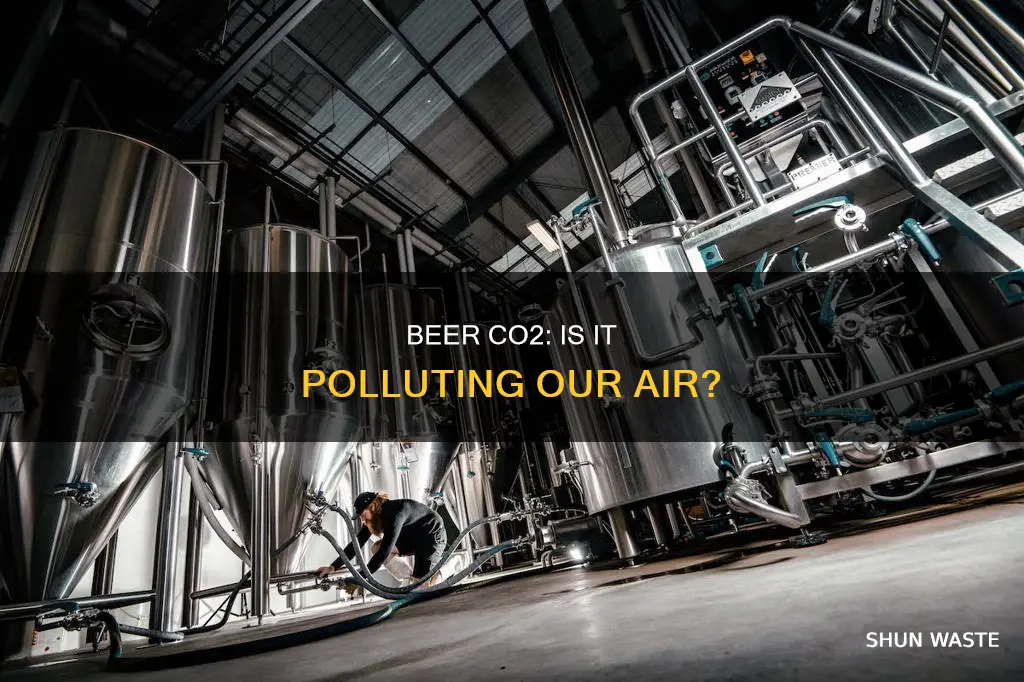
The production and consumption of beer contribute to air pollution. The global alcoholic beverage industry produces around 1.5 gigatons of greenhouse gas emissions annually, comparable to the emissions of 276 million cars. Beer contributes significantly to this, with a single bottle of beer (355ml) equivalent to 0.25 kg of CO2. The fermentation process releases CO2, and it is also used throughout the brewing, packaging, and serving processes. While major breweries have systems to capture CO2 for reuse, smaller craft breweries often purchase it from polluting sources.
Characteristics | Values |
---|---|
CO2 in beer | CO2 is a natural byproduct of the beer-brewing process and is also used as an ingredient in beer |
Beer and climate change | The global alcoholic beverage industry produces around 1.5 gigatons of greenhouse gas emissions annually, contributing to climate change. Beer is a significant contributor to an individual's carbon footprint. |
CO2 recapture systems | Large breweries have systems to capture CO2 produced during fermentation for reuse in carbonation and other functions, but this technology is not available on a smaller scale. |
CO2 usage in craft breweries | CO2 is used to move beer between tanks, purge tanks and lines, and carbonate the final product. |
CO2 and nitrogen | Nitrogen is sometimes used as an alternative to CO2 in the brewing process and can be combined with CO2 for dispensing beer. |
Beer packaging | Cans are better for the environment than bottles, provided they are recycled. |
What You'll Learn
The carbonation process
Carbonation is an essential part of the beer-making process, creating the bubbles and foam, or "head", on top of a poured beer. Carbonation occurs naturally in beer as yeast produces carbon dioxide along with alcohol when they eat sugar. The amount of carbonation in a beer varies, with American-style lagers tending to have high carbonation levels, while certain barley wines or stouts have lower levels of carbon dioxide.
There are different methods of carbonation, including force carbonation and natural carbonation. Force carbonation involves pumping carbon dioxide into a sealed container with the beer, which is then absorbed into the liquid. This method is often used for kegs, with the carbonation process taking anywhere from 12 hours to 3 days, depending on the temperature of the beer and how much it is agitated.
Natural carbonation occurs when yeast produces carbon dioxide during the fermentation process. To achieve the desired level of carbonation, brewers can add a specific amount of sugar just before bottling. The yeast will then process the sugar to produce carbon dioxide. This method takes longer, with bottles typically left at room temperature for two to three weeks to allow for carbonation to occur.
Carbonation levels are critical in achieving the perfect pint of beer. Dispensing systems use carbon dioxide to move the beer from the keg to the tap, and the right mix of gases is essential to maintaining the brewer's precise carbonation levels. Nitrogen separators are often used to produce the ideal mix of gases for dispensing beer, as they can help compensate for temperatures outside the normal range.
Carbon dioxide is also used throughout the brewing process for various applications, including purging tanks, scrubbing oxygen, and moving beer between tanks. It is a crucial processing aid and ingredient in craft beer production.
Air Pollution Masks: Effective Protection or Just a Fad?
You may want to see also
CO2 as a processing aid and ingredient
Carbon dioxide (CO2) is an essential ingredient in the production of beer. It is used for a variety of purposes, including carbonating the beer, pressurizing the kegs or bottles, and dispensing the beer. CO2 is also used in a number of other ways in the brewing process, such as cleaning and sanitizing equipment and protecting the beer from oxidation.
CO2 is a natural by-product of the beer-brewing process. During the fermentation stage, yeast breaks down the sugars from the beer wort into alcohol and CO2. The result is carbonation, which produces the bubbles and foam, or head, at the top of a poured beer. Different beers have different amounts of carbonation. For example, American-style lagers tend to have very high carbonation levels, while certain barley wines or stouts have lower CO2 levels.
CO2 is bought in liquid form and mostly heated back into a gas onsite for usage. It is used to move beer between tanks and to pressurize fermentation tanks. CO2 is also used to purge oxygen from tanks, cans, and lines to prevent oxidation and spoilage. This process is known as tank purging and is the biggest use of CO2 in the cellar.
CO2 is also used in the packaging of beer, in can filler and keg racker operations, and to pre-purge and pressurize equipment. It is used to maintain proper head pressure on tanks and to move beer or product from one tank to another. CO2 is added to the beer to give it its characteristic fizziness. The amount of CO2 added varies depending on the type of beer being brewed. For example, lagers are typically carbonated with less CO2 than ales.
Large-scale breweries often have the resources to invest in CO2 recovery and reuse systems, which can help reduce their CO2 emissions and save money on CO2 costs. These systems capture the CO2 that is released during the brewing process and recycle it back into the brewery for various applications.
Air Pollution Course Project: Breathe Easy with Data
You may want to see also
CO2 recovery systems
The production of beer contributes to climate change, with the global alcoholic beverage industry producing around 1.5 gigatons of greenhouse gas emissions annually. CO2 is a natural byproduct of the beer-brewing process, and it is also bought in liquid form and heated back into a gas for usage onsite.
The benefits of CO2 recovery systems include:
- Greener process with lower emissions and a reduced carbon footprint
- Cost savings due to reduced CO2 purchases and lower energy costs
- Independence from the CO2 market
- Reduced waste
- Increased sustainability
However, there are also potential drawbacks to consider. CO2 recovery systems can be very expensive to install, and there may be concerns about their potential negative impact on the quality of the beer. Additionally, the robotic control needed for a fully automated system can be a significant investment.
Vapor's Impact: Air Pollution's Unseen Threat
You may want to see also
The environmental impact of beer production
Firstly, the production of CO2, a key ingredient in beer, can be a source of pollution. While CO2 is a natural by-product of the fermentation process, additional CO2 is often purchased and heated on-site, which can contribute to a brewery's carbon emissions.
Secondly, the energy-intensive nature of beer production is a major concern. The process requires reliable agricultural producers, a stable energy source for heating and cooling, and significant water supply and usage. The energy used to produce the electricity required for brewing, as well as the fuel used for transportation, contributes to greenhouse gas emissions. The brewing industry is one of the largest industrial users of water, and the constant cleaning necessary during the brewing process further exacerbates water consumption.
Thirdly, the upstream environmental impact of beer production includes glass manufacturing, barley production, and malting. Glass bottles require a significant amount of energy to produce, although using recycled content can reduce this impact. Traditional barley production methods involve intensive tilling practices and the use of pesticides and fertilizers, which have a heavy environmental footprint. The drying and roasting processes in malting are also energy-intensive.
Additionally, the beer-brewing process often generates large amounts of wastewater and solid waste, which must be treated and disposed of safely and in accordance with strict discharge regulations.
To address these environmental challenges, the brewing industry is exploring new technologies and innovations. Some breweries are adopting renewable energy programs, and others are implementing systems that increase manufacturing efficiency, such as the BrewMonitor System. Craft brewers are also exploring sustainable practices, such as using nitrogen separators for draught systems and carbon capture solutions.
Electricity's Air Pollution: Is It a Real Concern?
You may want to see also
The impact of beer packaging on the environment
The beer industry is a significant player in the global economy, with an annual world beer production of over 1.34 billion hL in 2002. It is also one of the largest industrial users of water. The production and packaging of beer have a large environmental footprint, and the industry is facing increasing pressure to address these concerns.
A 2020 study by Manchester University found that the global alcoholic beverage industry produces around 1.5 gigatons of greenhouse gas emissions annually, comparable to the emissions of 276 million cars. The beer-brewing process generates large amounts of wastewater effluent and solid waste, and energy consumption is also a major issue. The BBC Climate Change Food Calculator states that drinking one pint of beer three to five times a week amounts to 139kg of greenhouse gas emissions per year.
The packaging phase of beer production is a significant contributor to the environmental impact of the industry. A life cycle assessment by Science Direct compared the environmental impacts of beer packaging in PET kegs, glass bottles, and aluminum cans. The results showed that draught beer in PET kegs is the most sustainable option, with a 90% lower footprint than other packaging types. Stainless steel kegs can be reused many times, reducing waste and the need for new materials. Aluminum cans are also highly valued for their lightweight nature and ability to be infinitely recycled without losing their original properties. This reduces the environmental impact by requiring less energy than producing new materials and lowering transportation costs and the associated carbon footprint. Glass bottles are completely recyclable and reusable, preserving the quality and flavor of the beer.
To reduce their environmental impact, breweries are adopting eco-friendly packaging solutions. Sustainable packaging helps to reduce waste, save energy, and minimize the use of non-recyclable materials. Implementing sustainable practices also increases consumer trust and loyalty, as customers are more likely to support environmentally conscious brands.
Ethanol's Air Pollution Effects: What You Need to Know
You may want to see also
Frequently asked questions
Yes, the CO2 from beer contributes to air pollution. CO2 is a natural byproduct of the beer-brewing process, and it is also added to beer as an ingredient during the fermentation stage to create carbonation.
A 355ml bottle of beer is equivalent to 0.25kg of CO2 or 1.3km of driving.
CO2 is used to move beer through lines and pressurize tanks during the brewing and packaging process. It also helps to maintain the brewer's precise carbonation levels and move the beer from the keg out of the tap. Using air compressors introduces too much oxygen to the beer, impacting its taste and quality.
The beer industry has a significant carbon footprint. According to a Manchester University study conducted in 2020, the global alcoholic beverage industry produces around 1.5 gigatons of greenhouse gas emissions annually, comparable to the emissions of 276 million cars. The fermentation process releases CO2, and other factors such as ingredients, packaging, fuel, electricity, and transport contribute to the industry's carbon footprint.