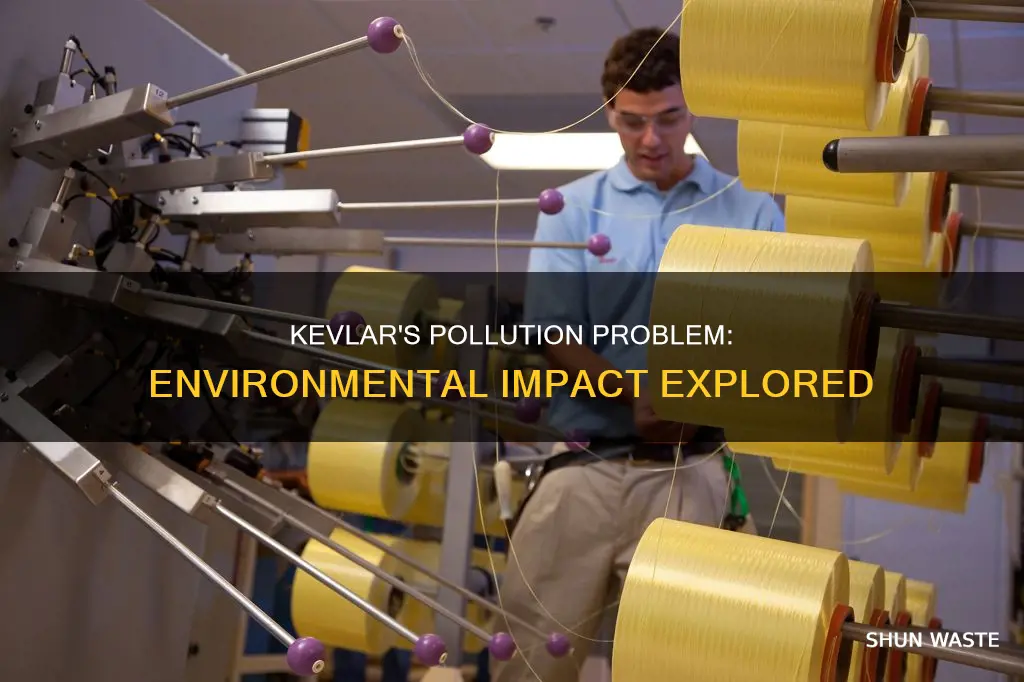
Kevlar is a synthetic fibre known for its strength and heat resistance. It was invented in 1965 and has since been used across various industries. However, the production and disposal of Kevlar can harm the environment. The manufacturing process involves using toxic chemicals such as sulphuric acid, which can cause pollution if not properly handled or disposed of. Kevlar is also non-biodegradable, meaning it can remain in the environment for hundreds of years, impacting ecosystems and wildlife. Despite its negative environmental impact, Kevlar is 100% recyclable, but this must be done by specialist companies.
Characteristics | Values |
---|---|
Recyclability | 100% recyclable |
Environmental impact | Similar to plastic |
Biodegradability | Not biodegradable |
Production process | Involves harmful chemicals like sulphuric acid and chlorine |
Disposal | Must be disposed of correctly by a specialized company to avoid causing pollution |
Eco-friendly alternatives | Hemp, recycled polyester, bamboo, Tencel, cork |
Health risk | Unreasonable risk to human health, potentially causing miscarriages, reduced fertility, and damage to liver, kidneys, immune system, and nervous system |
What You'll Learn
- Kevlar's non-biodegradability means it persists in the environment for hundreds of years
- The production of Kevlar involves harmful chemicals, including sulphuric acid
- Kevlar's disposal can cause pollution if not properly managed
- The use of sulphuric acid in the production of Kevlar is unsustainable
- There are eco-friendly alternatives to Kevlar, such as hemp and bamboo
Kevlar's non-biodegradability means it persists in the environment for hundreds of years
Kevlar is a synthetic fibre with a variety of useful applications, including heat resistance and exceptional strength. However, its production and disposal can be harmful to the environment. One of the main substances used in the production of Kevlar is sulphuric acid, which is very toxic to animals and plants. If sulphuric acid is disposed of or used incorrectly, it can cause significant harm to the environment.
Kevlar is not biodegradable, which means that once it is disposed of, it will persist in the environment for hundreds of years. This has a detrimental impact on ecosystems and wildlife, as animals may ingest or become entangled in the material, leading to physical harm. Kevlar's non-biodegradability also contributes to plastic waste, as it takes centuries to decompose.
Despite Kevlar's recyclability, it can still be very polluting if not disposed of correctly. Recycling Kevlar requires specialised knowledge, and if it is simply left in a landfill, it will not decompose for a very long time, if ever. Therefore, it is critical to dispose of Kevlar properly to mitigate its negative environmental impact.
To address the environmental concerns associated with Kevlar production and disposal, efforts are being made to develop more sustainable and eco-friendly alternatives. Some potential alternatives include natural fibres such as hemp, bamboo, and cork, which are renewable and biodegradable. Additionally, recycled synthetic materials, such as recycled polyester made from plastic bottles, can also reduce waste and pollution. These alternatives offer industries currently reliant on Kevlar more environmentally friendly options without compromising performance or durability.
Robots and Pollution: What's the Connection?
You may want to see also
The production of Kevlar involves harmful chemicals, including sulphuric acid
Kevlar is a synthetic fibre with a variety of useful applications, including bulletproof vests and tires, thanks to its exceptional strength and heat resistance. However, its production and disposal can harm the environment. The manufacturing process involves using various chemicals, including sulphuric acid, which can result in pollution if not properly handled or disposed of. Sulphuric acid is used to keep the Kevlar in solution during the spinning process, and it is very toxic to animals and plants. If it is incorrectly disposed of or used, it can cause great harm to the environment due to its toxicity.
Kevlar is also not biodegradable, so it will remain in the environment for an extended period, impacting ecosystems and wildlife. Poor disposal methods, such as leaving it in nature after it has worn out, contribute to plastic waste that takes centuries to decompose. Therefore, understanding how we manufacture and dispose of Kevlar is critical for mitigating its negative environmental impacts.
Despite these challenges, Kevlar is 100% recyclable, which reduces its environmental impact if disposed of correctly. Recycling companies specializing in synthetic fibres, such as Kevlar, have procedures to minimize potential damage while producing a high-quality product. Additionally, steps are being taken towards eco-friendly production methods, resulting in less environmental impact.
To conclude, while the production of Kevlar involves harmful chemicals, including sulphuric acid, which can cause pollution, proper handling, disposal, and recycling procedures can minimize its negative impact on the environment.
Oil Refineries: Air Pollution's Worst Enemy?
You may want to see also
Kevlar's disposal can cause pollution if not properly managed
Kevlar is a synthetic fibre with a variety of useful applications, including bulletproof vests and tires, thanks to its exceptional strength and heat resistance. However, its production and disposal can significantly impact the environment.
The manufacturing process involves using various chemicals, including sulfuric acid, which can be harmful to both humans and the environment. If these chemicals are not properly handled or disposed of, they can cause pollution, especially in nearby water sources. For example, sulfuric acid is very toxic to animals and plants, and if it comes into contact with water, it can cause significant harm.
Additionally, Kevlar is not biodegradable, meaning it will persist in the environment for hundreds of years, similar to plastic waste. This can threaten wildlife, which may ingest or become entangled in the material, causing physical harm. Therefore, Kevlar's disposal can cause pollution if not properly managed. It must be recycled by a company specializing in such materials to minimize its environmental impact.
However, Kevlar is 100% recyclable and can be reused multiple times, reducing its environmental impact. Recycling companies that specialize in synthetic fibres, such as Kevlar, have procedures in place to minimize potential environmental damage while producing high-quality recycled products. Nevertheless, finding sustainable and eco-friendly alternatives to Kevlar is important. Some possible alternatives include hemp, recycled polyester, bamboo, Tencel, and cork, all of which have lower environmental impacts and are biodegradable.
Overall, while Kevlar has numerous benefits due to its strength and heat resistance, its production and disposal must be carefully managed to mitigate its negative environmental consequences.
Small Airports, Big Impact: Understanding Their Pollution Footprint
You may want to see also
The use of sulphuric acid in the production of Kevlar is unsustainable
Kevlar is a synthetic fibre with a variety of applications, including bulletproof and stab-proof vests, and is known for its exceptional strength and heat resistance. However, its production and disposal can harm the environment.
The manufacturing of Kevlar involves a complex process of spinning fibres and the use of sulphuric acid. Sulphuric acid is necessary to keep the Kevlar in solution during the spinning process due to Kevlar's water-insolubility. While Kevlar is 100% recyclable, its production process is unsustainable and harmful to the environment. Sulphuric acid, a substance used in the production of Kevlar, is very toxic to animals and plants. If it is incorrectly handled or disposed of, it can cause pollution in nearby water sources and do great harm. The use of concentrated sulphuric acid is challenging and can affect the sustainability of its use.
The production of Kevlar involves various other chemicals that can be harmful to both humans and the environment. Chlorine, for example, is another chemical used in the production of Kevlar that can cause pollution if not properly managed. Additionally, Kevlar is not biodegradable, meaning it will persist in the environment for hundreds of years, threatening wildlife and ecosystems.
To minimise the environmental impact of Kevlar production, it is crucial to implement sustainable practices and dispose of Kevlar correctly. Recycling companies specialising in synthetic fibres, such as Kevlar, have procedures in place to minimise potential damage while producing high-quality recycled products. Despite Kevlar's recyclability, its production process, particularly the use of sulphuric acid, remains unsustainable and harmful to the environment if not properly managed.
Overall, while Kevlar has valuable applications, the use of sulphuric acid in its production is unsustainable and contributes to its negative environmental impact. To mitigate these effects, eco-friendly production methods and sustainable alternatives to Kevlar are being explored.
Volcanic Eruptions: Air Pollution Culprits or Nature's Wonder?
You may want to see also
There are eco-friendly alternatives to Kevlar, such as hemp and bamboo
Kevlar is a synthetic fibre with a variety of applications, including body armour, tires, and ropes. It is made from long chains of molecules called polymers that are tightly woven to form a highly durable fabric. Kevlar's production and disposal can have a detrimental impact on the environment. The manufacturing process involves using toxic chemicals, such as sulphuric acid, which can result in pollution if not properly handled or disposed of. Kevlar is also not biodegradable, meaning it can persist in the environment for hundreds of years, threatening wildlife and ecosystems.
Fortunately, there are eco-friendly alternatives to Kevlar that offer similar levels of protection and durability. These include natural fibres such as hemp and bamboo. Hemp is a renewable, biodegradable fibre with a low carbon footprint. Bamboo is also biodegradable and requires fewer resources to produce than traditional materials. These alternatives allow industries to transition to more environmentally friendly practices without sacrificing performance.
Other eco-friendly alternatives to Kevlar include recycled polyester, Tencel, cork, and Dyneema. Recycled polyester is made from recycled plastic bottles, reducing waste and pollution. Tencel is a sustainable fabric made from wood pulp that is biodegradable, strong, and durable. Cork is a renewable, biodegradable, and recyclable material made from the bark of cork oak trees. Dyneema is an incredibly strong and durable material made from ultra-high molecular weight polyethylene, making it ideal for protective gear.
In addition to these alternatives, steps can be taken to reduce the environmental impact of Kevlar production and disposal. Companies can use recycled materials, reduce waste during manufacturing, and encourage customers to recycle or repurpose their gear. By implementing sustainable practices and exploring eco-friendly alternatives, we can help protect the environment while still staying safe and protected.
Dams and Dead Fish: A Water Pollution Concern?
You may want to see also
Frequently asked questions
Kevlar is not biodegradable and can remain in the environment for hundreds of years, threatening wildlife. Its production and disposal can also cause pollution if not properly managed. However, it is 100% recyclable, so if disposed of correctly, it has a very small environmental impact.
The manufacturing of Kevlar involves the use of various chemicals, including sulphuric acid, chlorine, and N-methylpyrrolidone (NMP). These chemicals can be harmful to both humans and the environment if not properly handled or disposed of.
Kevlar must be disposed of by a company that specializes in recycling synthetic fibers. If it is not recycled correctly, it can pollute the environment and have similar effects to plastic waste.
Some more sustainable and biodegradable alternatives to Kevlar include hemp, recycled polyester, bamboo, Tencel, and cork. These materials have a lower environmental impact while still offering durability and performance.
Steps are being taken to adopt more eco-friendly production methods for Kevlar, and recycling companies have procedures in place to minimize potential environmental damage while producing high-quality recycled products. Additionally, workplace protections are being implemented to safeguard workers' health during Kevlar production.