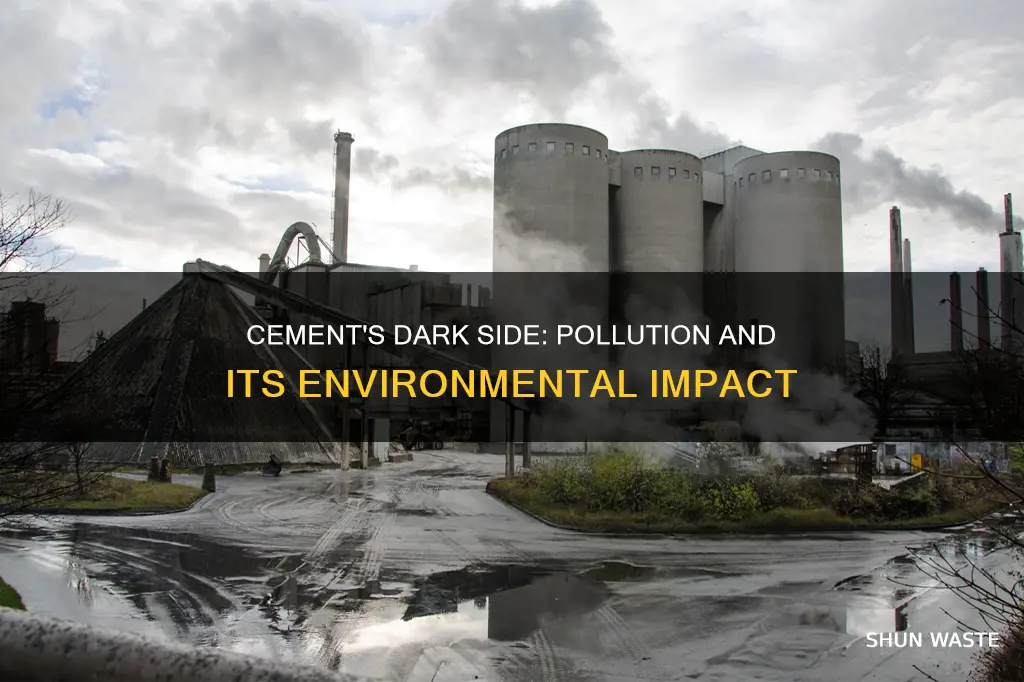
Cement is a key ingredient in concrete, the most widely used substance on Earth after water. It is used to create hard surfaces and to build the majority of the world's bridges, roads, and dams. However, the cement industry is responsible for a massive carbon footprint, contributing about 8% of the world's carbon dioxide emissions. The chemical process required to make cement involves burning limestone in kilns heated to over 1400 degrees Celsius, releasing carbon dioxide and other harmful pollutants. This, along with the energy-intensive process of manufacturing cement, makes the cement industry a significant source of air pollution and a contributor to climate change.
Characteristics | Values |
---|---|
Global carbon dioxide emissions | 7%-8% |
Comparison with other sources | More than all trucks in the world |
Comparison with other industries | Third largest emitter in the world |
Comparison within the construction industry | More than the average car |
Comparison with aviation fuel | More than 2.5% emissions from aviation fuel |
Limestone quarries and cement factories | Sources of air pollution |
Water consumption | Almost a tenth of the world's industrial water use |
Heat-island effect | Concrete absorbs warmth of the sun and traps gases |
Respiratory diseases | Worsens silicosis and other respiratory diseases |
Air pollution | Concrete dust is a major source |
Radioactivity | Natural radioactive elements can be present |
Health concerns | Toxicity and radioactivity |
Energy | Requires large amounts of energy |
Sulfur dioxide emissions | More than 500,000 tons per year |
Nitrogen oxide emissions | More than 500,000 tons per year |
Carbon monoxide emissions | More than 500,000 tons per year |
What You'll Learn
- Limestone quarries and cement factories are sources of air pollution
- The cement manufacturing industry is a large source of nitrogen oxide and carbon monoxide
- The cement industry is one of the main producers of carbon dioxide
- Concrete dust is a major source of dangerous air pollution
- Green cement technology can reduce carbon emissions in cement production
Limestone quarries and cement factories are sources of air pollution
Limestone quarries and cement factories are significant sources of air pollution. Every stage of a quarry's lifecycle comes at a significant environmental cost: the loss of natural carbon sinks, the eradication of biodiversity, noise and
The cement industry is one of the main producers of carbon dioxide, a greenhouse gas. The production of one ton of cement releases about one ton of CO2 into the atmosphere, primarily due to the calcination of limestone and the burning of fossil fuels. The chemical process required to make cement involves heating kilns to over 1,400 degrees Celsius, causing the carbon trapped in the limestone to combine with oxygen and be released as CO2.
Cement factories also release other pollutants, including dust or particulate matter, NOx, SOx, carbon oxides, and methane. These emissions endanger the lives of nearby flora and fauna and contribute to air pollution and respiratory issues in humans. A study in Sri Lanka found that over 14% of people living close to cement factories suffer from respiratory disorders.
The acquisition of sand for concrete can also be environmentally catastrophic, as it destroys the world's beaches and river courses, leading to increased activity from organised crime gangs and violence.
Breathing and Pollution: What's the Real Connection?
You may want to see also
The cement manufacturing industry is a large source of nitrogen oxide and carbon monoxide
Cement is a stone-like building material responsible for 7% of global carbon dioxide emissions. The cement manufacturing industry is a large source of nitrogen oxide and carbon monoxide, emitting over 500,000 tons per year of these gases, as well as sulfur dioxide. Nitrogen oxide (NOx) is associated with a variety of adverse health and environmental impacts, including ground-level ozone, acid rain, smog formation, and respiratory distress. It contributes to urban pollution and can trigger a wide range of health issues, including respiratory problems.
NOx formation occurs at high temperatures, and nitrogen oxides are produced as byproducts of hydrocarbon combustion. The cement-making process involves burning limestone in kilns heated to over 1400 degrees Celsius, which is approximately four times hotter than a home oven's self-clean cycle. This high temperature is necessary to create clinker, the key raw ingredient of cement. The extreme heat required to produce clinker makes cement manufacturing particularly energy-intensive and polluting.
Carbon monoxide (CO), another byproduct of the cement manufacturing process, is equally harmful to health. CO reduces oxygen delivery to the body's organs and tissues and has adverse effects on the cardiovascular and central nervous systems. Additionally, it contributes to the formation of smog and ground-level ozone, which further exacerbates respiratory issues.
The cement industry is under increasing pressure to reduce its environmental impact and find greener alternatives. While some companies are working on solutions, buyer reluctance to pay more for sustainable materials remains a challenge.
Air Pollutants: Understanding Their Diverse Sources
You may want to see also
The cement industry is one of the main producers of carbon dioxide
The cement industry is a significant contributor to global carbon dioxide emissions, accounting for about 7-8% of the world's total CO2 emissions. This is mainly due to the chemical process required to manufacture cement, which involves burning limestone in kilns heated to extremely high temperatures. The carbon trapped in the limestone combines with oxygen and is released as CO2, a potent greenhouse gas. The production of clinker, a key ingredient in cement, is particularly carbon-intensive, responsible for about half of the emissions from cement production.
The cement industry's high emissions have drawn the attention of policymakers aiming to reduce global warming. Strategies to mitigate the industry's carbon footprint include improving material efficiency, adopting low-carbon fuels, and investing in carbon capture and storage (CCS) technologies. Some companies are exploring alternative raw materials and processes to reduce their environmental impact. For instance, Brimstone, a US-based company, has developed a method to produce cement from carbon-free calcium silicate rocks, which can passively capture atmospheric carbon dioxide.
Despite these efforts, the industry faces challenges in reducing emissions while meeting the growing global demand for cement, driven by increasing infrastructure needs in developing economies. The high cost of greener cement mixes and the lack of demand for sustainable materials also hinder progress. However, with tightening pollution rules and the increasing cost of emitting CO2, cement manufacturers are under pressure to find solutions.
To achieve net-zero emissions by 2050, global cement production must remain stable or decrease. Several countries and regions are making notable progress in decarbonising cement production. For example, the United States' Inflation Reduction Act allocated $5.8 billion for industrial decarbonisation, while the European Union's Green Deal Industrial Plan aims to preserve the EU's attractiveness for net-zero industries. These initiatives, along with continued research and adoption of low-carbon alternatives, are crucial steps towards reducing the cement industry's carbon footprint.
Biogas and Air Pollution: Friend or Foe?
You may want to see also
Concrete dust is a major source of dangerous air pollution
Concrete is the most widely used substance on the planet after water. It is a thirsty behemoth, consuming almost a tenth of the world's industrial water use. It also has a significant carbon footprint, with the cement industry being one of the main producers of carbon dioxide, a greenhouse gas. The production of cement is responsible for about 7% of global carbon dioxide emissions.
The cement-making process is especially carbon-intensive because of the chemical reaction required to make it. Kilns are heated to more than 1,400 degrees Celsius, about four times hotter than a home oven set to self-clean. Inside the kiln, carbon trapped in limestone combines with oxygen and is released as CO2. A ton of cement yields at least half a ton of CO2.
Concrete dust released by building demolition and natural disasters can be a major source of dangerous air pollution. Following the Great Hanshin earthquake, concrete dust was found to be the major source of dangerous air pollution. The presence of some substances in concrete, including useful and unwanted additives, can cause health concerns due to toxicity and radioactivity. Natural radioactive elements such as K, U, Th, and Rn can be present in concrete dwellings, depending on the source of the raw materials used. For example, some stones naturally emit radon, and uranium was once common in mine refuse.
In addition to the health concerns posed by concrete dust, the process of manufacturing cement also has a significant environmental impact. The dust from wind-blown stocks and mixers contributes as much as 10% of the coarse particulate matter that chokes Delhi. Researchers found in 2015 that the air pollution index at all of the 19 biggest construction sites in Delhi exceeded safe levels by at least three times. The acquisition of sand for concrete has also been linked to the destruction of the world's beaches and river courses, with this form of mining increasingly associated with organised crime and violence.
There are methods to reduce the environmental and health impact of concrete and cement. For example, titanium dioxide (TiO2) has been used to remove nitrogen oxides from the atmosphere. Nitrogen oxides are atmospheric gases that contribute to acid rain and smog formation, which are the result of urban pollution. A Canadian company has also patented a technology that uses early age carbonation to sequester CO2 by injecting recycled liquid carbon dioxide into the concrete wet-mix stage during the manufacturing process. This technology sequesters the greenhouse gas pollutant in concrete infrastructure, buildings, and roads.
Human Flatulence: Air Pollutant or Natural Process?
You may want to see also
Green cement technology can reduce carbon emissions in cement production
Cement is a binding element made of calcium, silicon, iron, and aluminum that is mixed with sand, gravel, and water to make concrete, the second-most widely used substance on the planet after water. The cement industry is one of the main producers of carbon dioxide, a greenhouse gas. Cement manufacturing is responsible for about 8% of the world's carbon dioxide emissions, with cement contributing to 70% of carbon emissions from concrete manufacturing.
Cement production is one of the most energy-intensive processes in the world, requiring kilns to be heated to more than 1,400 degrees Celsius (2,600 Fahrenheit). This high temperature releases carbon trapped in the limestone, which combines with oxygen and is released as carbon dioxide. As such, reducing the amount of carbon emitted by cement production is critical to achieving global climate targets.
Green cement technology offers a solution to reduce carbon emissions in cement production. Green cement is an alternative product that can lower cement production's carbon emissions by up to 70%. Several companies have developed innovative technologies to reduce emissions, such as CarbonCure, which injects captured carbon into wet cement, strengthening the material and locking in carbon dioxide. Another example is Solidia and LaFarge, who have developed a concrete mix design and curing process that mixes cement powder with sand and cures the mixture with carbon dioxide to create concrete with a significantly lower carbon footprint.
To promote the adoption of green cement technology, financial incentives can be introduced for companies to transition to greener alternatives. For instance, tax credits, reimbursements, or grants can help businesses overcome the initial costs of transitioning to green cement. Additionally, organizations like the Trade and Technology Council (TTC) are working to strengthen sustainable trade between the European Union and the United States, creating opportunities for the development and trade of low-carbon cement and concrete.
Ground Pollution: Understanding the Root Causes
You may want to see also
Frequently asked questions
Yes, cement is a major cause of pollution. The cement industry is responsible for about 7-8% of global carbon dioxide emissions, more than all the trucks in the world.
The chemical process required to make cement emits staggeringly high levels of CO2. Limestone quarries and cement factories are often sources of air pollution. Kilns are heated to more than 1,400 degrees Celsius, and inside, carbon trapped in the limestone combines with oxygen and is released as CO2.
The cement manufacturing industry is the third-largest industrial source of pollution, emitting more than 500,000 tons per year of sulfur dioxide, nitrogen oxide, and carbon monoxide. These gases can cause a variety of health problems, including respiratory issues, and contribute to environmental issues such as acid rain and smog formation.
Several efforts are being made to reduce the pollution caused by cement. Some companies are working on cutting the amount of clinker in their cement or using substitutes like fly-ash or slag. Others are focusing on improving energy efficiency and using fossil-fuel alternatives. Additionally, carbon capture and storage devices can siphon off pollutants and trap them underground.