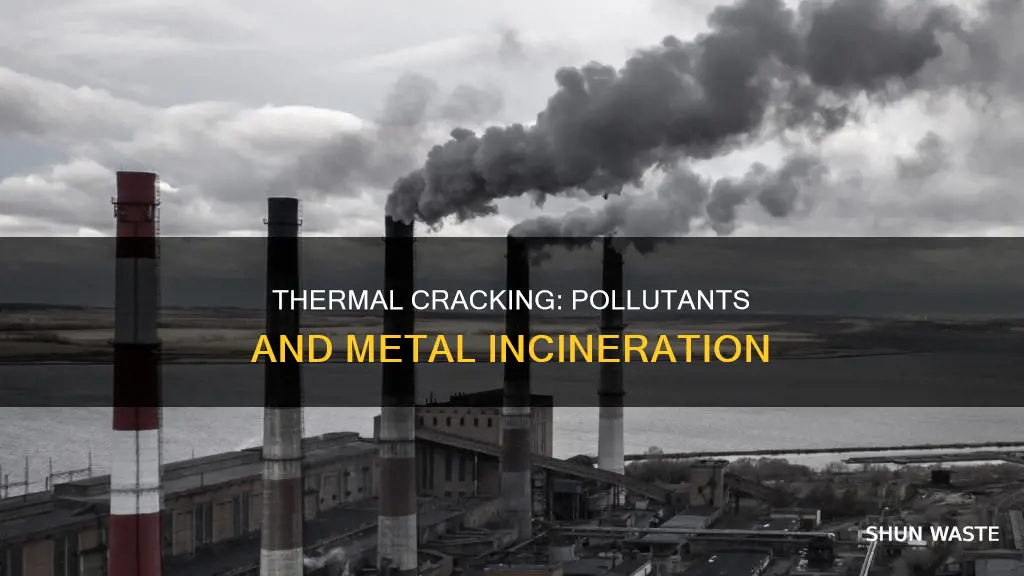
Incineration is a waste treatment process that involves the combustion of waste materials. It is considered a form of thermal treatment due to its high-temperature waste treatment system. Incineration has been criticized for its environmental impact, particularly the emission of toxic gases and the necessity to purify flue gases. The process also faces challenges with the absence of raw material recovery and low thermodynamic efficiency. As a result, feedstock recycling of waste polymers through thermal cracking in molten metal has emerged as a potential alternative. This method has demonstrated high exergy efficiency, offering an environmentally preferable option to incineration. However, it is important to note that incineration technologies have undergone rapid development, especially in China, and continue to be widely applied for the treatment of municipal solid waste.
Characteristics | Values |
---|---|
Pollutants produced by incineration | Nitrogen oxides, sulfur dioxide, hydrochloric acid, heavy metals (including mercury), dioxins, furans, fine particles |
Pollutants produced by thermal cracking of molten metal | None mentioned in sources |
Advantages of thermal cracking of molten metal over incineration | Higher exergy efficiency, raw material recovery, lower environmental pollution, no emission of toxic gaseous compounds |
What You'll Learn
Feedstock recycling of waste polymers
The process of feedstock recycling has been studied extensively, with the first International Symposium on Feedstock Recycling of Polymeric Materials (ISFR) held in 1999. Since then, the symposium has been conducted five more times, with the latest one held in Spain in 2013. These conferences have covered various topics, including thermal processes with and without catalysts, wet processes in various solvents, and the dehydrochlorination of PVC.
Feedstock recycling offers a way to recover raw materials and primary energy from waste. It has been found to be more efficient than other processes, particularly incineration, with an exergy efficiency of about 79.5%. This is because incineration has no raw material recovery, low thermodynamic efficiency, and may emit toxic gases. In contrast, feedstock recycling can be used to produce fuel mixtures of hydrocarbons. For example, over 90% of waste polyolefins may be converted into a mixture of hydrocarbons (C4–C24) through thermal decomposition in a molten metal bed.
However, feedstock recycling of waste polymers has not been widely adopted due to high investment costs, the necessity of frequent reactor cleaning, and the cost of catalysts. Additionally, the efficiency of the recycling process depends on the composition of the waste material, and a good feedstock consisting of one component is rare.
US Plastic Pollution: Global Impact and Responsibility
You may want to see also
Thermal decomposition of PE or PP
The thermal decomposition of polyolefins, such as polyethylene (PE) and polypropylene (PP), is a well-known process for feedstock recycling of waste polymers. This process involves the conversion of polyolefins into a fuel-like mixture of hydrocarbons using thermal cracking in a molten metal bed. This method is environmentally accepted and offers higher exergy efficiency compared to other processes, especially incineration.
The thermal decomposition behaviour of mixtures of PE and PP with different weight ratios has been studied. The weight loss behaviours of these polymers during decomposition are influenced by the presence of impurities and the heating rates. The pyrolysis experiments on mixtures of PP with PE and PP with polystyrene (PS) polymers exhibited marked differences in weight loss behaviours due to the impurities in the waste polymeric form.
The kinetic parameters of the thermal decomposition process are crucial. The apparent activation energy (Ea) for the pyrolysis of PE and PP varies depending on the research methodology and the degree of polymer conversion. The decomposition process of polyolefins is optimally described using a model of two simultaneous chemical reactions, homolytic and heterolytic dissociations, with distinct activation energies. This model achieved a high fitting accuracy, indicating its effectiveness in describing the decomposition process.
The dynamic thermal decomposition of PE and PP mixtures was investigated at different heating rates, ranging from 5 to 25 K min-1. The β-scission and alkylation reactions in the catalytic process were promoted by HY, improving the yields of certain aromatic hydrocarbons. The synergistic effect of pretreatment and catalysis resulted in a significantly enhanced yield of benzene, toluene, ethylbenzene, and xylene (BTEX).
Overall, the thermal decomposition of PE or PP in a molten metal bed is a promising method for feedstock recycling of waste polymers. It offers high exergy efficiency, minimises environmental pollution, and recovers valuable raw materials. The detailed kinetic analysis of the decomposition process is essential for optimising the process and improving its environmental benefits.
Light Pollution Filters: Effective Solution or Marketing Gimmick?
You may want to see also
Energy recovery by incineration
The process of incineration involves burning non-hazardous waste to generate energy. This reduces the volume of solid waste sent to landfills and also recovers energy from the waste-burning process. The heat released during incineration is captured in the form of pressurised steam, which can then be used directly for heating or converted into electrical energy through a turbo-generator.
In terms of environmental impact, incineration can reduce carbon emissions by offsetting the need for energy from fossil sources and decreasing methane generation from landfills. However, it is important to note that incineration can also contribute to environmental pollution, especially when compared to other methods such as feedstock recycling of waste polymers by thermal and chemical methods, which is considered more environmentally friendly.
The European Union aims to achieve climate neutrality by 2050, and clean energy technology deployment is crucial to meeting this goal. While incineration has its place in waste management and energy recovery, there is a growing emphasis on reducing waste generation and increasing recycling efforts to achieve sustainability. Recycling and reusing materials from municipal solid waste (MSW) can lead to energy conservation and a reduction in the accumulation of waste.
In conclusion, energy recovery by incineration remains a viable option for waste management and energy generation in certain regions with specific constraints. However, it is not without its drawbacks, and the focus should be on exploring more environmentally friendly alternatives, such as thermal cracking in molten metal, and promoting waste reduction and recycling initiatives to achieve long-term sustainability.
Developing Countries: Polluters or Victims?
You may want to see also
Heavy metal pollutants from incineration
Incineration is a widely used method for treating municipal solid waste (MSW). However, it has come under scrutiny due to the production of hazardous byproducts, including heavy metal pollutants. These heavy metals are present in the waste stream fed to the incineration facility and can be concentrated in the resulting ash.
Heavy metals, such as lead, cadmium, mercury, zinc, copper, chromium, arsenic, and nickel, are of particular concern due to their potential environmental and health risks. They can be emitted into the atmosphere during incineration, contributing to air pollution, or they may contaminate the surrounding soil, threatening human health through the food chain. The concentration of heavy metals in incinerator ash is particularly high in developing countries, where the rate of waste separation is lower.
Studies have shown that the combustion chamber temperature plays a crucial role in determining the fate of heavy metals during incineration. Higher temperatures can stabilize heavy metals and reduce their volatility. However, some volatile heavy metals, such as lead, cadmium, zinc, and copper, may evaporate from MSW incineration fly ash, mainly in the form of chlorides.
The use of air pollution control devices (APCDs) and specific waste screening practices can help reduce heavy metal emissions from incinerators. Additionally, the application of hydrated lime sorbents and activated carbon can aid in capturing volatile heavy metals and removing acid gases during the incineration process.
The stabilization of heavy metals in incinerator ash is essential to prevent their leaching into the environment. For example, the use of molten salts in thermal treatment has shown promising results in stabilizing heavy metals and reducing their leaching compared to raw fly ash.
The Hudson River: A Polluted Past and Present
You may want to see also
Thermal methane cracking
The main reaction in TMC is endothermic and has strong kinetic limitations due to a high activation energy, which falls between 356 and 452 kJ/mol. The reaction can be thermal, catalytic, or a combination of both. The thermal route does not use a catalyst, while the catalytic route employs one to reduce the operating temperature to below 800°C. The combined process likely refers to using a catalyst in the thermal process.
The main problem with methane cracking, regardless of whether it is catalytic or not, is the cumulative deposition of coke, which can plug the reactor. A possible solution is to carry out the reaction in a molten medium, such as molten salts or molten metals. Molten metals show higher catalytic activity than molten salts. In particular, Ni, Pd, Pt, Co, and Fe exhibit high catalytic behaviour, while In, Ga, Sn, Pb, and Bi are considered inert metals with low catalytic activity. However, combining these inert metals could result in unexpected performance. Additionally, molten metals can homogenize temperature, enhancing methane decomposition.
The use of regenerative reactors can help overcome the challenges of reactor blockages and supplying heat for the endothermic reaction. In a regenerative reactor, the first cycle stores heat in a medium like ceramic packing, and the second cycle passes the heat to the endothermic reaction stream. The storage medium also acts as a bed for carbon deposition and can play a role in storing and releasing heat to the gas stream.
The methane feed rate to the reactor is inversely proportional to residence time. At a constant temperature, increasing the feed rate decreases the percentage of hydrogen in the reactor output. Increasing the temperature reduces the intensity of hydrogen reduction when the methane feed rate is increased.
Measuring Pollutants: Techniques and Tools for Environmental Monitoring
You may want to see also
Frequently asked questions
Thermal cracking in molten metal incineration is a process used to convert waste plastics into fuel. This method is more environmentally friendly than incineration.
Pollutants are produced in all incineration processes. However, thermal cracking in molten metal produces fewer pollutants than incineration. For example, it does not emit greenhouse gases.
The outputs of this process are a fuel-like mixture of hydrocarbons and raw materials.
Thermal cracking in molten metal is more environmentally friendly than other incineration methods. It has a high exergy efficiency of around 79.5%.